Characteristics of Welding For Stainless Steel Alloys
Known for its corrosion resistance and outstanding durability, stainless steel can withstand harsh conditions few metals can match.
This makes it ideal for a range of industries -- from medical equipment to chemical processing.
However, when working with metal, welding is often required to fabricate complex shapes, construct large structures, or reinforce critical design components.
Stainless steel alloys offer advantages when used for welding — in this article, let's discover the types of stainless steel alloys used for welding and their common characteristics.
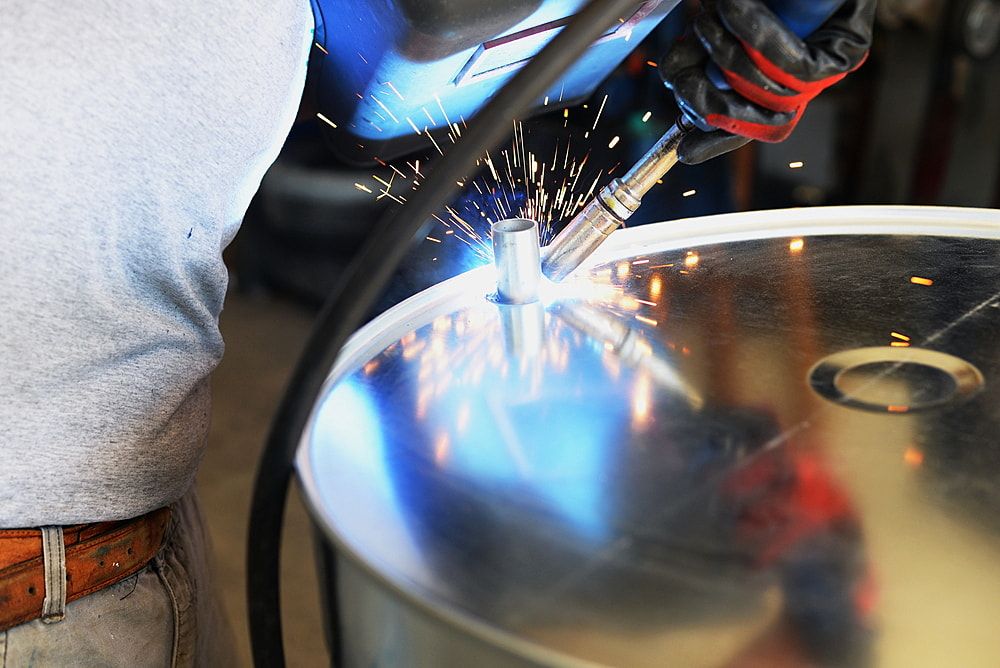
Firstly, what welding methods work best with stainless steel?
Most welding methods work well with stainless steel as long as the filler material and temperature requirements of the metals to be joined are considered carefully.
The methods include:
Metal Inert Gas (MIG) Welding or Gas Metal AC Welding (GMAW)
Tungsten Inert Gas (TIG) Welding
Spot Welding
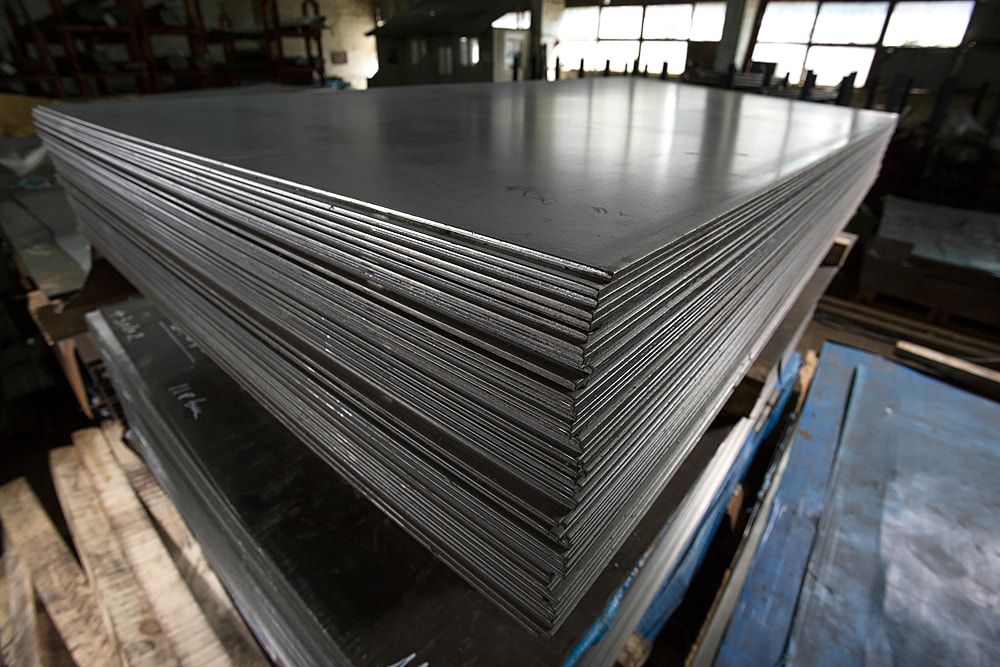
What are the characteristics of common welding stainless steel alloys?
Austenitic stainless steel alloys
Austenitic stainless steel is a type of alloy that is highly resistant to corrosion and is considered extremely malleable.
Additionally, they’re also exceedingly weldable. In fact, austenitic stainless steels are the most weldable stainless steels on the market.
Austenitic stainless steel can be welded without the use of any heat treatment whatsoever. Most typically, when welded, specific alloys of austenitic stainless steel are welded to identical species of austenitic stainless steel.
Ferritic stainless steel alloys
Ferritic stainless steel are categorised as strong yet resistant to corrosion. However, it is noted to lack ductility and are prone to cracking when exposed to hot temperatures.
For these reasons, they are seldom used for their welding capabilities, only occasionally chosen to be welded in the form of thin sheets.
Martensitic stainless steel alloys
Martensitic stainless steel is strong and durable. The downside is that they perform poorly when in corrosive environments!
Also, since they are vulnerable to cool cracking, they don’t weld easily.
However, this does not mean that it’s impossible to weld martensitic steel.
In fact, manufacturers do so on a regular basis, usually by welding together pieces of metal with identical carbon and chromium percentages.
Duplex stainless steel alloys
Possessing both austenitic and ferritic characteristics, duplex stainless steels possess a solid combination of toughness, durability, and ductility.
Their biggest strength, however, is their strong resistance to corrosion.
That's one of the reasons why they are chosen to be welded on a regular basis.
However, when welding duplex stainless steel, one must be very careful with temperatures. Using either too little or too much heat can compromise the structural integrity of the steel.
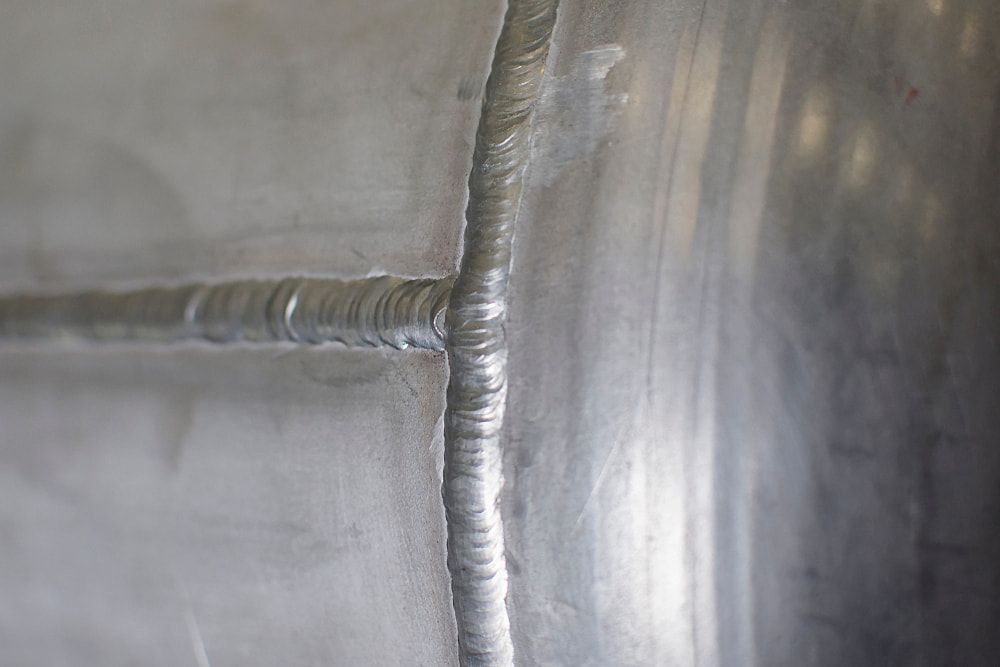
5 tips to ensure safe, long-lasting welding of stainless steel alloy
1. Always clean stainless steel surfaces prior to welding
Stainless steel is subject to contamination by high-carbon steels and other metals.
When this happens, it significantly reduces the corrosion resistance of the stainless steel.
Cleaning the surface of your stainless steel not only helps to reduce contamination risks but will strengthen the weld.
2. Choose a filler material similar to the metals you are welding
Choosing the appropriate filler material is essential to both ensuring a strong weld and maintaining the corrosion resistance of your stainless steel.
When choosing a filler, consider both the grades of steel and any suffixes involved.
3. Use a reliable tool to track material temperatures
Efficient, effective welding of stainless steel is all about controlling temperatures.
Monitoring temperatures throughout the welding process is a simple way to ensure long-lasting results and avoid compromising the quality of your stainless steel.
4. Watch for warping on thinner stainless steel parts
Overheating stainless steel can impact its corrosion resistance and strength.
However, when working with thin stainless steel parts or sheets, there is an additional risk to high temperatures -- warping.
To help minimize warping risks, start with low temps and use tack welds to secure pieces before filling in the weld later.
5. Always consider corrosion resistance of welds
If you are not using a corrosion-resistant filler, be sure to treat weld sites to avoid corrosion.
Primer or clear paint treatments can help to improve corrosion resistance and ensure your welds are as durable and long-lasting as the stainlesssteel surrounding them.
Looking for an expert in welding for stainless steel alloys? Try Choong Ngai Engineering
With Choong Ngai Engineering's veteran technicians and engineers, we can provide a start-to-end manufacturing and troubleshooting process of welding for stainless steel alloys.
Most importantly, we'll work alongside you and your team to understand and define your exact requirements, and this process ensures that we provide the best solution to your unique maintenance requirements.
We've been servicing happy customers for over 10 years. Learn more about our services and previous projects on our web site or contact us at https://www.choonngaiengineering.com