Factors to Consider When Choosing Your Stirring Impeller
Are you thinking twice about how to choose your required stirring impeller?
Stirring impellers are the component of the industrial mixer which imparts flow to the mixing process.
Their purpose is to transfer the energy driven by the motor to the contents of a tank as quickly and efficiently as possible.
That's why choosing an impeller based on what your mixer needs is vital to ensure smooth, safe and cost-efficient processing.
In this article, we'll discuss the different types of stirring impellers available in the market and what factors you need to consider when choosing it!
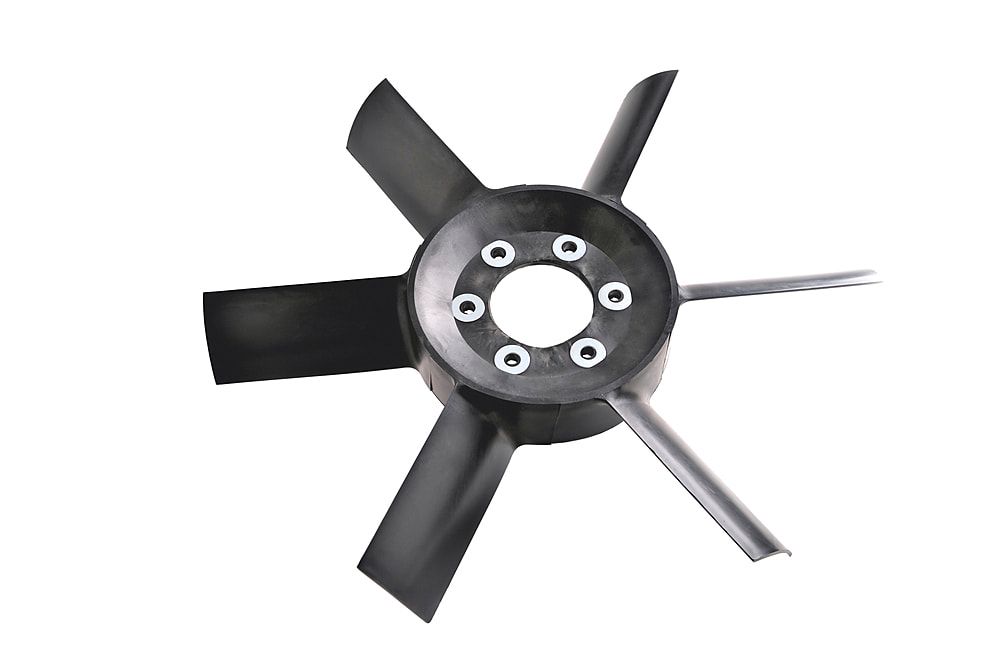
What are the types of stirring impellers available in the market?
Pitch-blade impellers
Pitch-blade impellers are commonly used for mixers that require an axial flow. They are known for their shear sensitivity and efficient mixing at low impeller tip speeds.
Radial flow impellers
These types of impellers are typically available in 4 or 6 blade designs. They are known to provide more shear and less flow per unit of applied horsepower than axial flow designs, and in comparison, radial flow impellers do not have a high tank turnover flow.
Mixed flow impellers
These are angled pitch-blade impellers result in a mixed flow, where the vertically angled blades move the liquid in axial as well as radial directions.
Distributed flow impellers
These are helical type impellers, which provide equally distributed shear plane as well as gradients in all directions. Such impellers are frequently used for solid substrate or high viscosity fermentations.
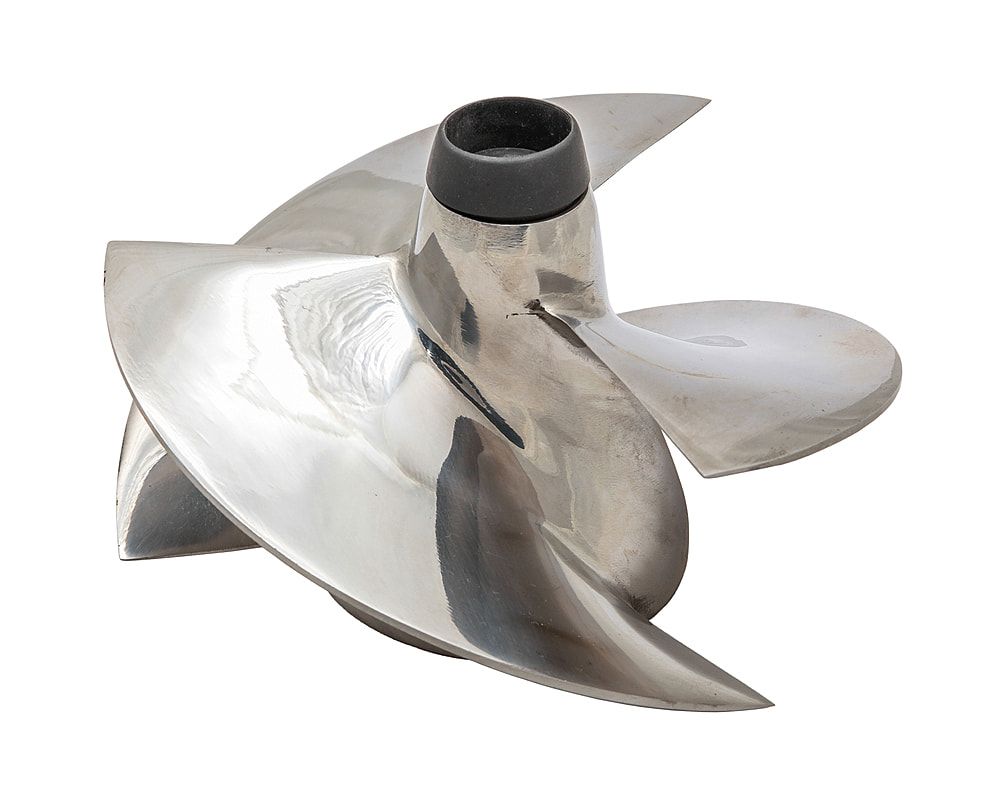
What are the factors you need to consider when choosing your stirring impeller?
The viscosity of your mixing material
The primary factor to be taken into consideration when selecting the impeller type is material viscosity.
Viscosity affects several aspects of impeller design and selection. Highly viscous liquids also require a longer length of time to completely mix, so this detail should also be taken into consideration when selecting an impeller.
In many cases, a hydrofoil impeller blade is well-suited for lower viscosities, while an axial flow or turbine pitched blade is better for mixing highly viscous substances.
Furthermore, the density of a substance is an important characteristic related to viscosity.
The mixing time required for your operations
The mixing time needed is a key factor for consideration.
It is an indication of how long the materials needs to be stirred as well as at which speed to obtain an optimal state of homogeneity.
Usually, the shorter the time, the better the mixing properties of the impeller and the balance of shear force within the mixer.
The power input of your mixer
Power input can be determined through the torque that acts on the impeller shaft while it is rotating.
The power input is an important factor due to its association with shear forces, and is also a key parameter during scale-up processes.
Since the impeller can also affect the quality of the product, it is valuable to determine the power input.
Other techniques exist including electrical power draw or calorimetric methods.
The placement of your mixing tank
The size and dimensions of the mixing tank also determines the type of impeller you choose.
The aspect ratio of the vessel is an important figure, and ideal mixing occurs when it’s as close to unity as possible.
Improper impeller placement can result in disuniformity throughout the contents of the vessel and staged flow patterns.
A common misconception assumes that vortexing and swirling in a mixture are both favourable indicators of quality.
While the contents of a vessel are in motion with swirling or vortexing, they can be merely rotating rather than actually mixing with one another.
How will the impeller be placed with your mixing tank
Tank design is the principal aspect in determining the impellers necessary to achieve equal mixing in an application.
Volumetric specifications, as well as the shape and positioning of a mixer (vertical, horizontal and etc) are both essential units in calculating the type and quantity of impellers.
As the tank gets larger, more impellers will need to be added in order to accomplish proper mixing.
The size of the impeller itself is primarily determined by the desired mixing intensity of a particular application. Intensity is related to the diameter when greater intensity is needed for adequate emulsification and mixing.
The materials that the impeller is constructed from
A common and suitable material for impellers in many different applications is stainless steel.
Stainless steel is exceptionally resistant to corrosion and contamination, which further extends the lifespan of an impeller.
Cleanliness is a necessity, especially in sanitary applications. Stainless steel is easy to clean and maintain.
Impellers can be manufactured in various grades of stainless steel. Other common choices include carbon steel, titanium, and nickel alloys.
They can also be finished with different coatings to cater to the needs of an application, and reinforced to extend their lifespan.
The compatibility of the impeller to your machine
Before choosing and finalising your mixing impeller, be sure that all parts are compatible.
For example, the shaft must fit the overhead stirrer's chuck; the impeller or blade must fit the shaft.
If the impeller requires affixment by screw, make sure that the shaft diameter fits the bore.
Note that larger impellers and shafts require higher torque from the overhead stirrer's motor to turn effectively.
This is absolutely vital when mixing high-viscosity samples. Attaching a high-viscosity impeller to an underpowered stirrer rarely works out well. Make sure that your stirrer has sufficient torque for your application!
Keep in mind the near-future needs of your facility. Not all impeller types are suited for production-scale mixing!
Looking for an expert in manufacturing stirring impellers? Try Choong Ngai Engineering
Now that you've discovered the different factors you need to know when choosing stirring impellers, it's time to make a decision!
With Choong Ngai Engineering's veteran technicians and engineers, we can provide a start-to-end manufacturing and troubleshooting process of fabricating mixing impellers for your business.
Most importantly, we'll work alongside you and your team to understand and define your exact requirements, and this process ensures that we provide the best solution to your unique maintenance requirements.
We've been servicing happy customers for over 10 years. Learn more about our services and previous projects on our web site or contact us at https://www.choonngaiengineering.com