Surface Finishing Options For Custom Metal Parts To Consider
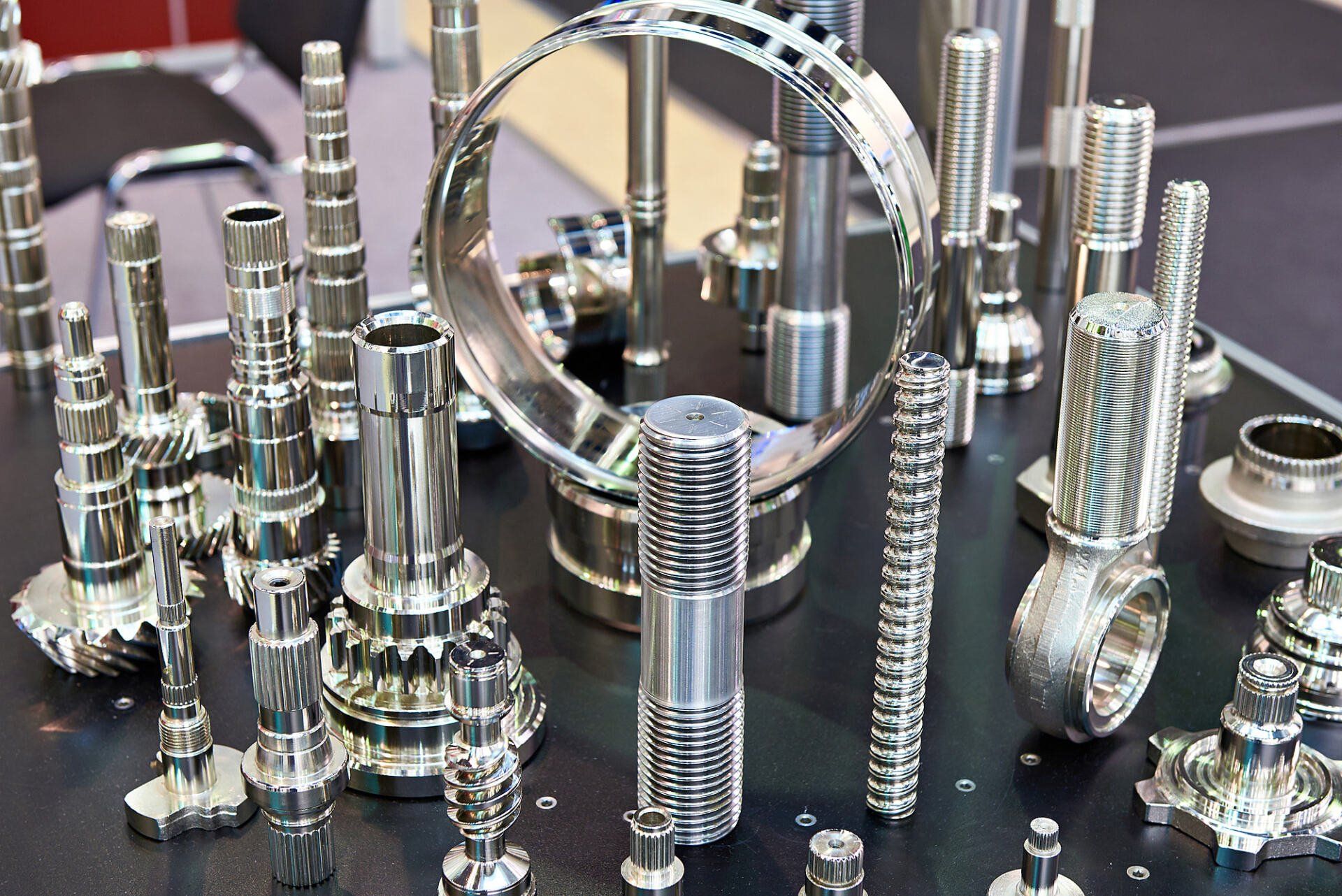
While there are various ways to make custom metal parts in Malaysia, one of the most economical and adaptable methods is through utilising sheet metal. Parts that use sheet metals frequently need to be post-processed or finished after they have been made to improve their physical or aesthetically pleasing qualities.
Because of this, just like there are different kinds of metals, there are also several types of metal finishing processes that metal fabricators apply to these metals. Lack of knowledge about the proper metal finishing processes for a project can lead to material waste and increase manufacturing costs.
Here are some different options for surface finishing.
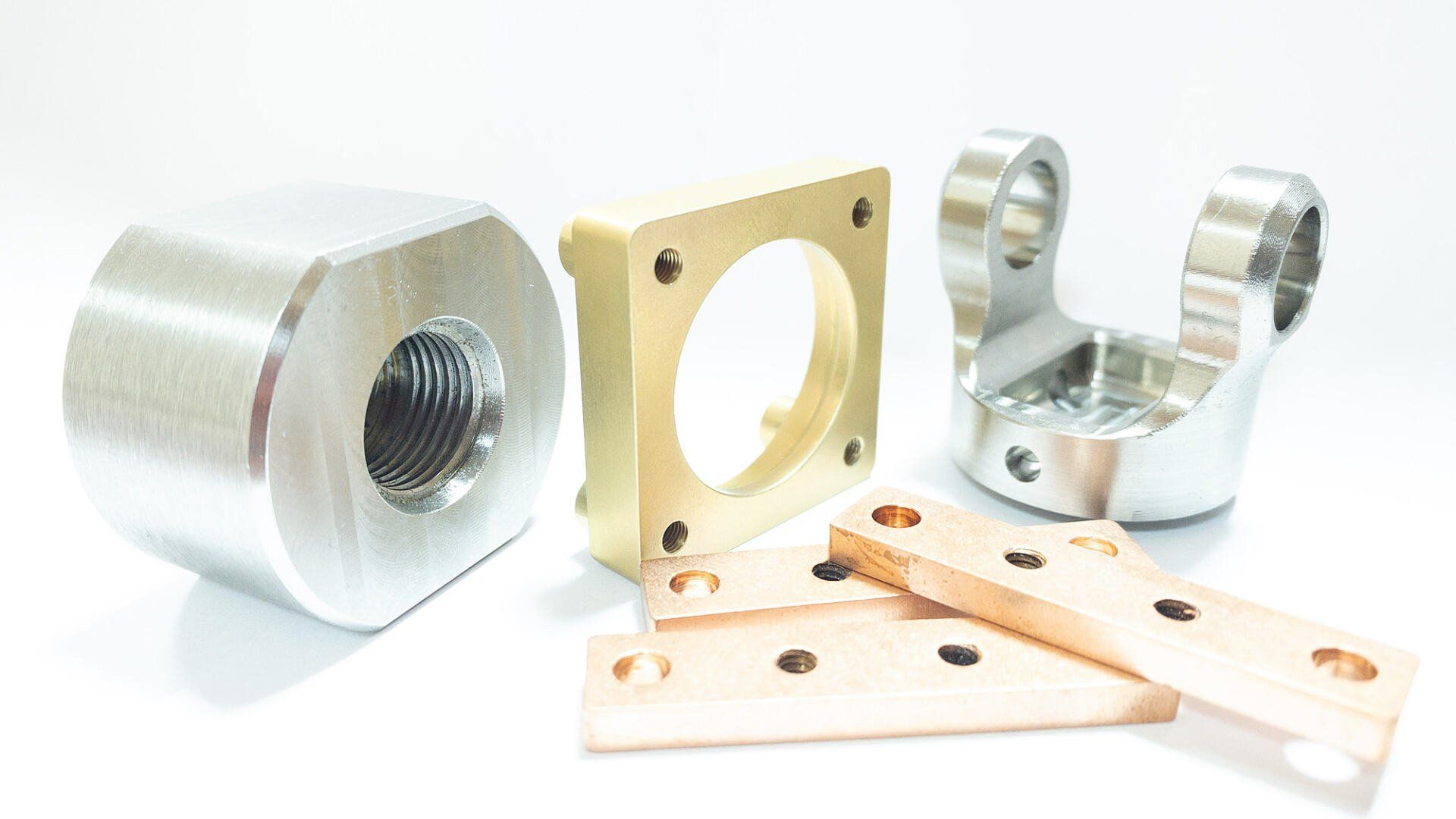
Understanding your options is crucial when choosing the best coatings for sheet metal parts. Here are some of the different types of surface finishing options that are quite common for custom metal work in Malaysia.
Standard Finish
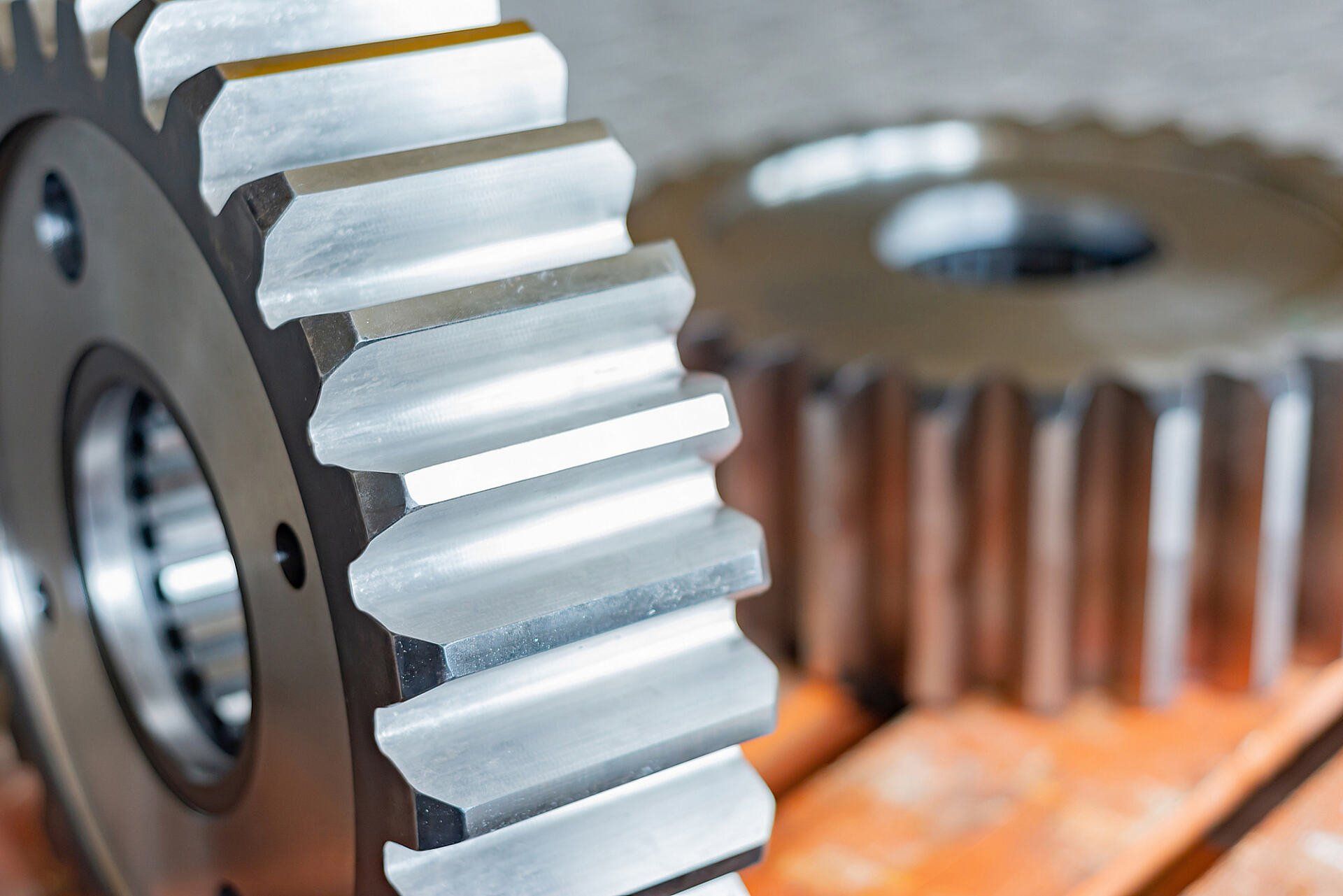
As the name suggests, a standard finish consists of no finishing work being done to the finished product. This industrial finish for sheet metal is often applied when the base material is already adequate for the application environment.
Due to the metal's inherent suitability for corrosive environments, it would typically not require further polishing even when utilised in a corrosive setting. Besides that, the material's natural appearance is another reason for not finishing a part.
Anodising
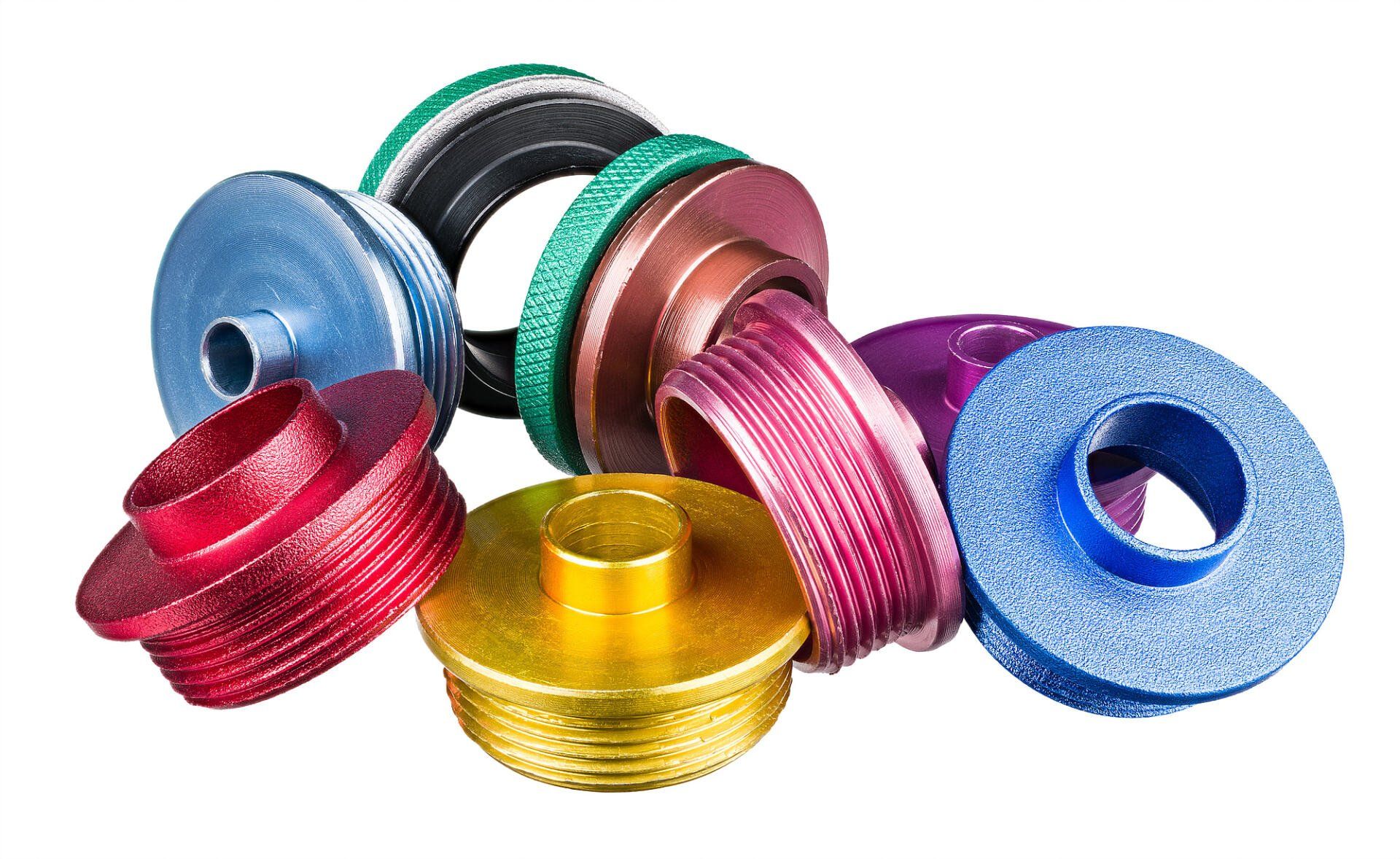
Metal fabricators utilise this electrolytic passivation method to thicken the natural oxide layer on the surface of metals. By anodising, the resistance of the metal to wear and corrosion will increase. Compared to other coating techniques, these oxide layers are quite thin but still incredibly durable.
This finishing also helps primers and glues adhere easily to metal surfaces compared to ordinary metals. However, when you anodise a metal, the microscopic texture of the surface of the metal will be altered.
Powder Coating
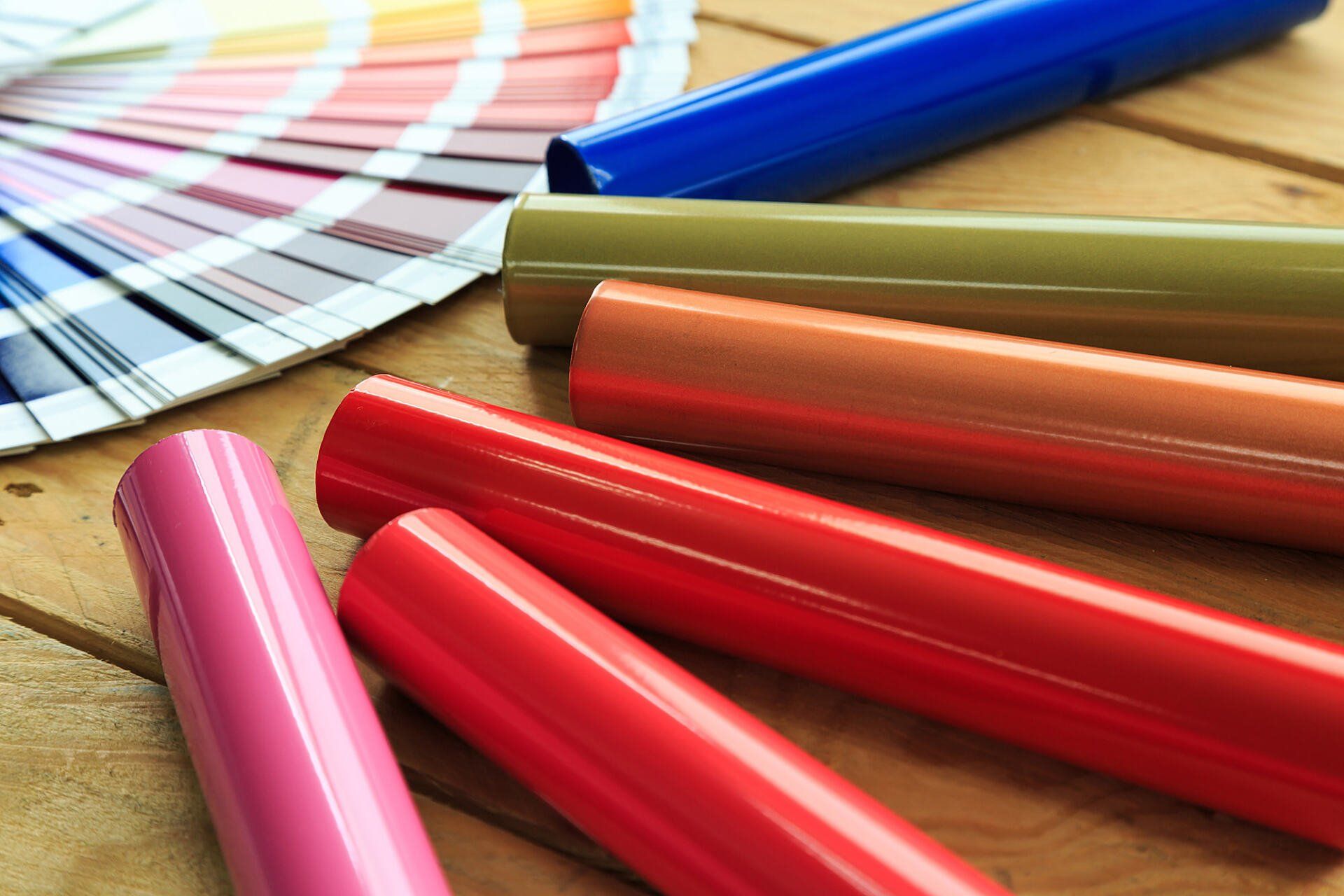
Electricity is used in this process to deposit a dry powder on the metal surface. When the metal has been electrostatically coated with powder, the metal fabricator places it in an oven to undergo a chemical reaction that will improve the powder's adhesion to the metal surface.
Powder coating offers a wide variety of colours for aesthetic purposes and is generally more corrosion-resistant than paint. However, it is not as good as anodisation or chemical coatings when it comes to preventing corrosion.
Pickling
This method of metal finishing can remove contaminants and surface imperfections from metals. Which is why pickle liquor, an acidic chemical, is required for this procedure. The pickle liquor also serves numerous functions, including metal corrosion prevention.
With the numerous benefits of the pickling process, metal fabricators use pickling in almost all metal manufacturing processes. However, due to the acidic level of the pickle liquor, the process itself may cause corrosion.
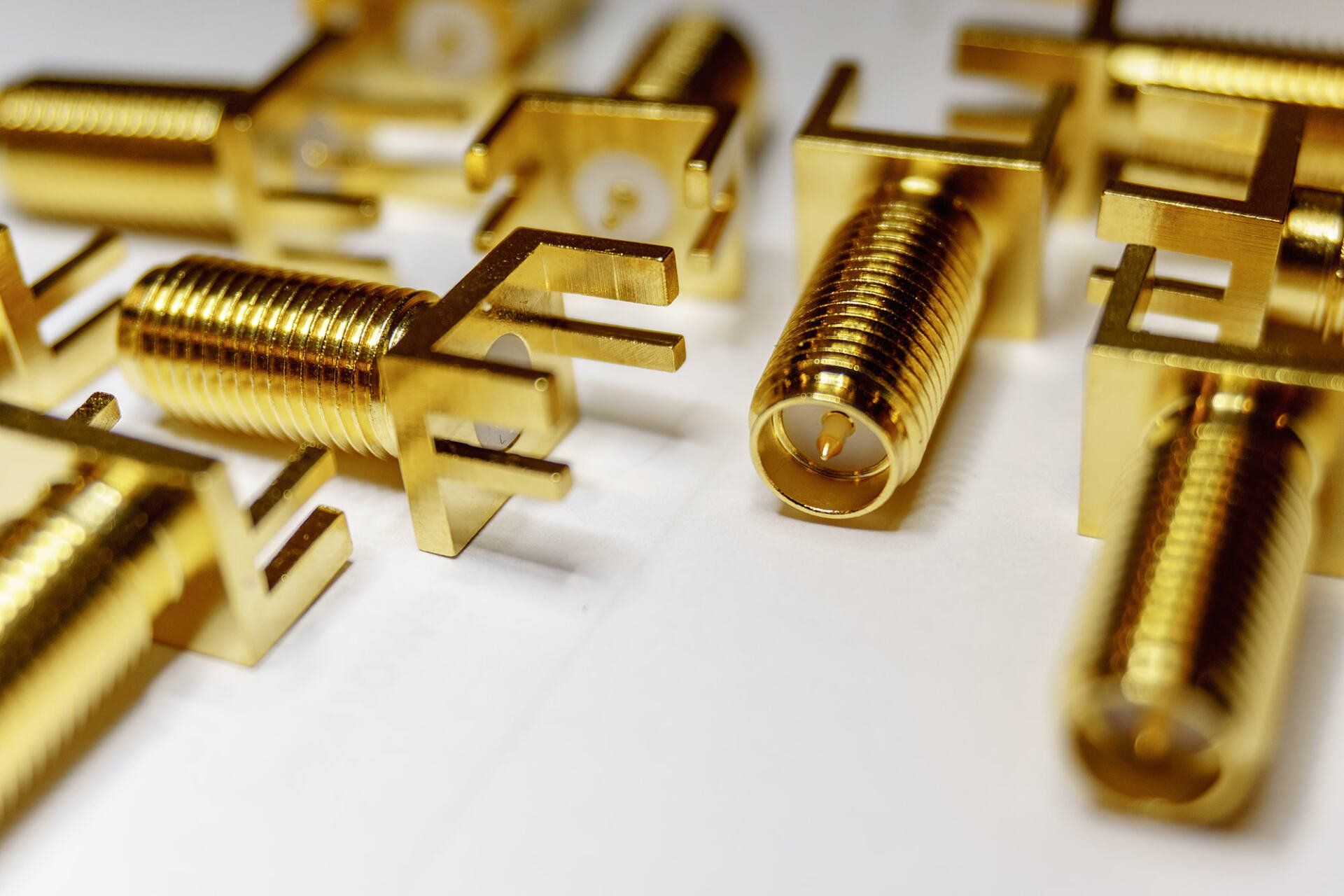
Besides being a great conductor, gold is also resistant to corrosion, tarnish, and oxidation. As such, it is the perfect coating for electrical contacts. Gold also has good solderability, increasing its usefulness in electronic components.
There are various types and classes of gold plating, which mainly refer to thicknesses and the purity of the gold used in plating.
Why Are Surface Finishes Important For Metals?
Surface coatings for metals are important in many different ways. Here are some of the benefits.
Enhances Aesthetic
The product's aesthetics are just as crucial as how well it functions for many clients. With metal surface treatment, your metal surface will look as good as new. Besides that, the improvement of metal's overall appearance is among its most important aspects. There are also a variety of procedures that are being used to finish the metal, including:
- removing any sharp edges
- washing the surface
- sanding the metal
Enhances the Metal's Ability to Withstand Corrosion
Corrosion is one of the main causes of metal surfaces and components being destroyed. This is why a proper surface finish is important to ensure the metal surface is well protected to increase its longevity.
Makes Cleaning Process Easier
By default, an unfinished metal is rough and has an uneven surface. Consequently, chemicals are needed when cleaning an unfinished metal. However, the chemicals that are being used to achieve the ideal clean surface on unfinished metal will increase the rate of the metal wear.
In contrast, contamination and adhesion are reduced with polished metals. Hence, the time needed to clean polished metal is reduced.
Looking for high quality metal parts? Visit Choong Ngai Engineering now!
Choong Ngai Engineering is a leading heavy equipment spare parts fabricator in Malaysia. With over 19 years of experience, we are your one-stop solution for all your heavy equipment spare parts needs. Contact us or call us at +6012-2726971 today to get started!