The Different Grades And Types Of Stainless Steel Tank
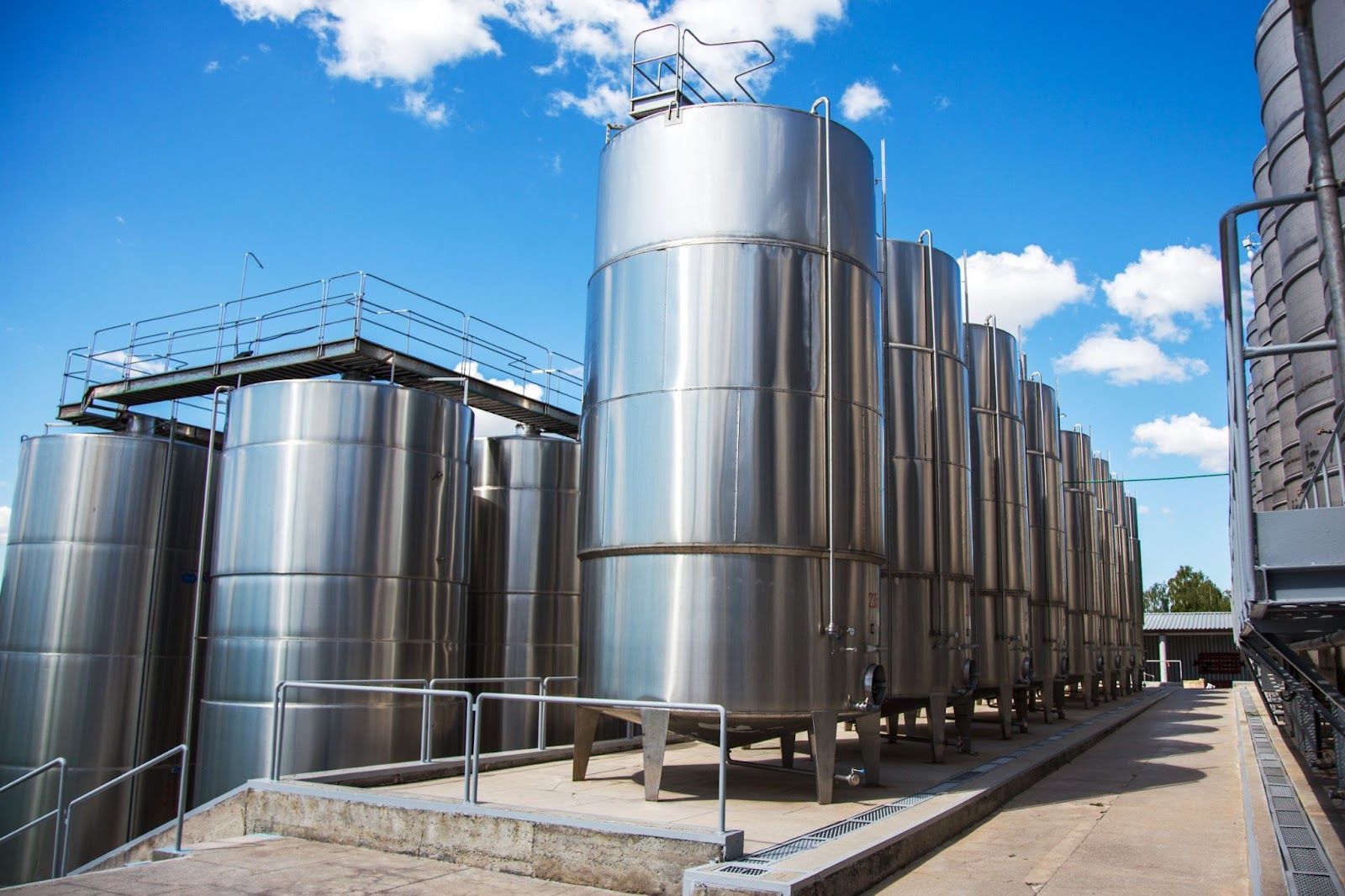
In manufacturing procedures involving food, drink, dairy, medicine, cosmetics, and other products where cleanliness and purity are crucial, stainless steel tanks are frequently used. They are also utilised in industrial facilities for storing gases and chemicals when a high level of resistance to chemical deterioration is required.
Stainless steel is a form of iron alloy that contains a specific amount of chromium, which gives the metal corrosion resistance. By forming a thin film of metal oxides that serve as a defence against corrosive substances, corrosion resistance can be achieved.
Since their construction is easily adaptable to different end uses, stainless steel tanks have a wide variety of applications. So, let's dive deeper into the different grades and types of stainless steel tanks that are available.
The Various Grades In Stainless Steel Tank
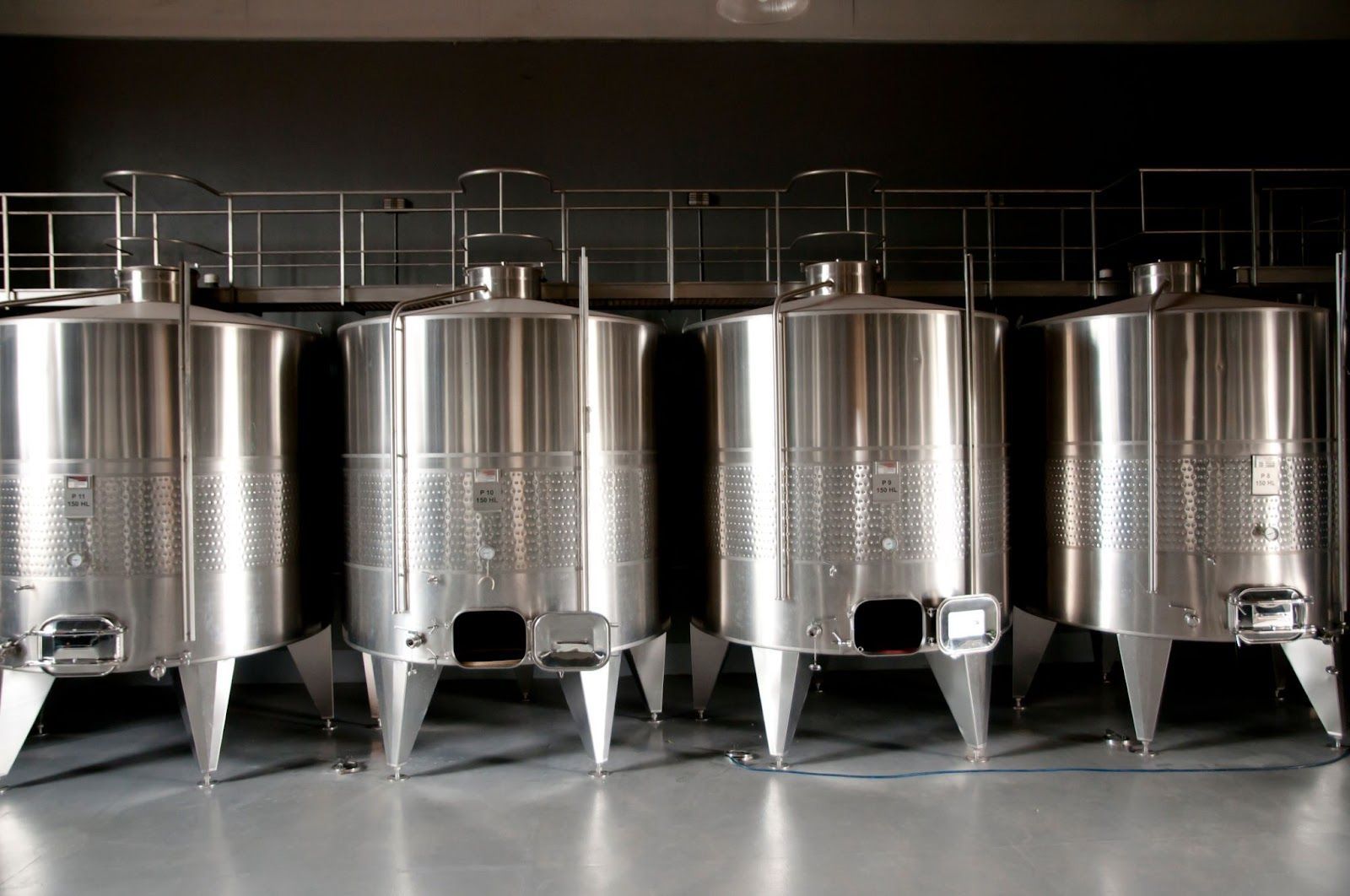
There is a huge variety of stainless steel grades available for handling different chemicals. As such, the performance at both high and low temperatures as well as corrosion resistance, strength, and toughness, differ between grades. The following three grades are commonly used to manufacture stainless steel tanks.
Stainless Steel 304 and 304L
With the exception of steel-forming alloys, stainless steel 304 is made up of 18–20% chromium, 8–11% nickel, and 2% manganese. This type of stainless steel is the most popular since it is less expensive than other grades and offers sufficient corrosion resistance for the majority of uses. It is versatile and suitable for the formation of a wide variety of products due to its austenitic metallurgical structure.
Similar amounts of chromium, nickel, and manganese can be found in stainless steel 304L. The decreased carbon content makes it different from stainless steel 304 and prevents the process known as sensitisation. Chromium carbides are created when alloyed chromium and carbon atoms in steel react at high temperatures, causing sensitisation.
There is less chromium left over to create the passive film since some of it has already been converted into chromium carbides. The steel structure is susceptible to intergranular corrosion because they develop at the grain boundaries.
This procedure can be problematic when stainless steel is used in high-temperature processes or applications. By reducing the carbide content, less chromium carbide is formed, and corrosion resistance is kept even at high temperatures.
Stainless Steel 316 and 316L
The following elements are found in stainless steel 316:
- 16–18% chromium
- 10–14% nickel
- 2% manganese
- 2-3% molybdenum
Due to the molybdenum addition, this grade is more corrosion-resistant than stainless steel 304. To combat the increased molybdenum's ability to create ferritic minerals, it contains more nickel.
Chemical storage tanks and tanks in marine environments are two common applications for stainless steel 316. The lower carbon grade, 316L, of stainless steel 316 is similar to that of stainless steel 304. For high-temperature applications, lower carbon content is also employed to avoid sensitisation.
Duplex Stainless Steel
Duplex stainless steel contains the following elements:
- 20-28% chromium
- 2-5% molybdenum
- 5-8% nickel
This grade of stainless steel has greater corrosion resistance and mechanical strength due to its increased chromium and molybdenum content. Due to its lower nickel content and higher strength for a given thickness, Duplex stainless steel is more affordable to use than 316 since it allows for the use of thinner plates and sheets.
The standard duplex, or 2205 stainless steel, is the grade of duplex stainless steel that is most often used.
The Different Types Of Stainless Steel Tanks
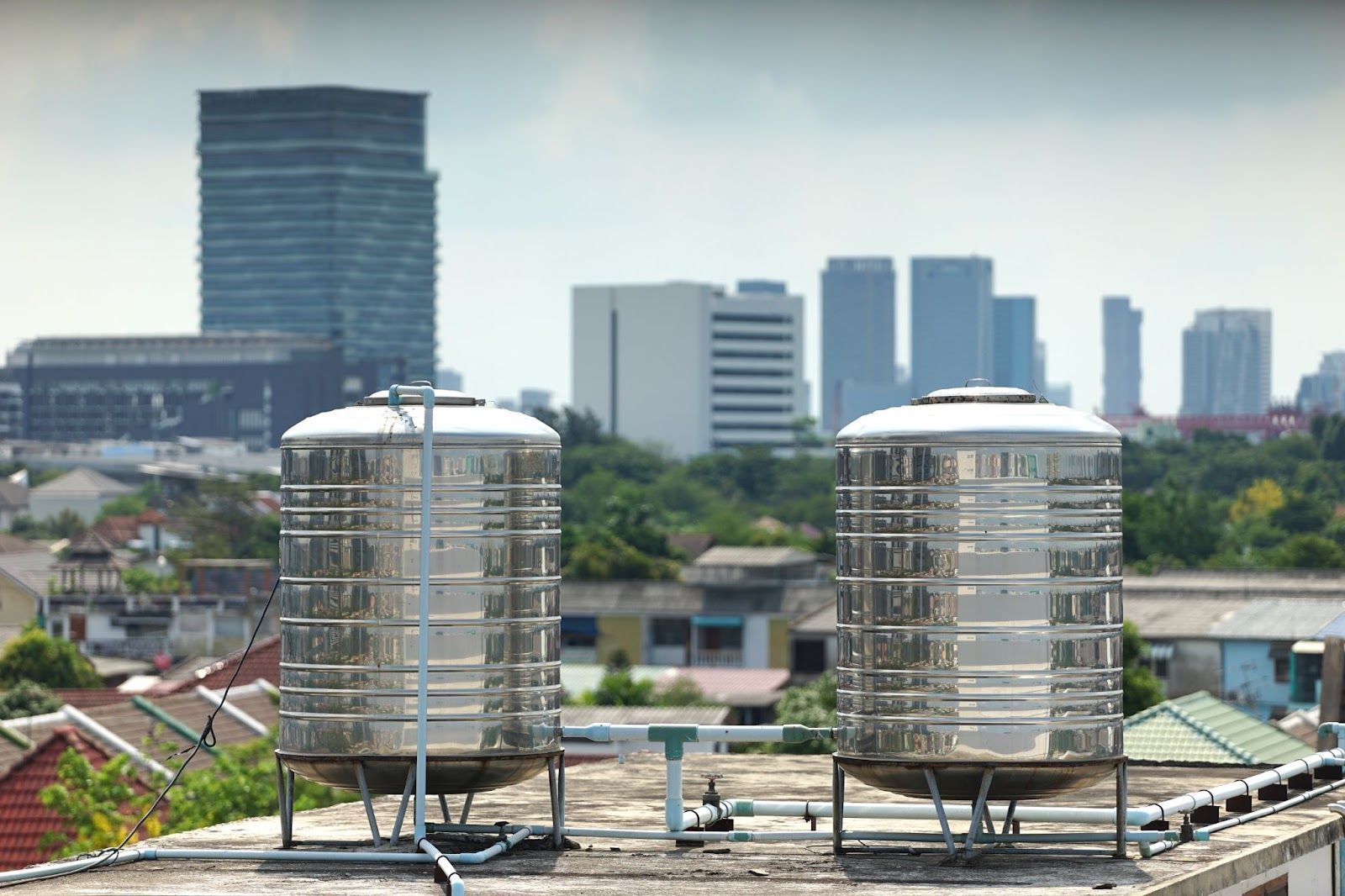
Tanks made of stainless steel can be customised to a great extent. For a particular application, several functionalities can be incorporated.
Additionally, stainless steel tanks come in a variety of configurations, including single- or double-walled, vertical or horizontal, insulated or heated, and more. The following are general classes of stainless steel tanks based on function and construction.
Single-walled Stainless Steel Tanks
These are the most basic stainless steel tanks, and they are typically cylindrical in shape. Depending on the use and size limitations, these can be positioned either vertically or horizontally.
The tank's internal and external surfaces are both shielded from corrosive substances owing to the single wall. They are primarily utilised in manufacturing facilities that require liquid raw materials as well as home water storage.
Double-walled Stainless Steel Tanks
They are utilised in applications where supplemental spill containment is necessary. Depending on the location where corrosion resistance is required, double-walled tanks may have one or both walls made of stainless steel.
Some stainless steel tanks have insulation between their twin walls. The insulation shields the product from changes in outside temperature.
Stainless Steel Clad Tanks
Construction of big, thick-walled stainless steel tanks is both costly and impractical. To address this, it is possible to build the tank using carbon steel plates that will withstand the static weight and pressure of the process fluid while also being covered in a thin layer of stainless steel cladding to prevent corrosion.
Carbon steel plates with a stainless steel coating are created by pressing and melting the two metals collectively. In the process, a metallurgical link is created.
Stainless steel sheets can be bonded on one (single-side cladding) or both sides (double-side cladding). In addition to pressing, there are other methods, including:
- Hot roll bonding
- Cold roll bonding
- Explosive bonding
Jacketed Stainless Steel Tanks
The majority of procedures that call for additional heating, cooling, or thermal stability employ these kinds of stainless steel tanks. In the area between the two stainless steel plates or sheets, a heating or cooling fluid circulates. Through the inner wall, heat is then transferred. After heat transfer, the cooling or heating liquid is redirected to the utility systems.
Stainless Steel Process Tanks
In most manufacturing and industrial facilities, stainless steel tanks of this kind are used for the following process:
- Blending
- Dissolving
- Homogenising process components or ingredients
The agitator or mixing head is these tanks' most distinguishing element. There are numerous agitator designs that can be used, such as:
- High-shear mixing heads
- Mixing paddles
- Impellers
- Helical agitators
Parameters, including temperature, pressure, and level, are being monitored by instruments that have been fitted. By using double walls, stainless steel process tanks can have extra advantages like insulation and heating.
High-pressure Stainless Steel Tanks
Low-pressure tanks are typically rated at atmospheric pressures up to 1 barg, making them suitable for household and commercial use. For example, the ASME Boiler and Pressure Vessel Code must be followed for design and construction when the operating pressure exceeds 1 barg. This is done to make sure that the vessel's stored energy won't endanger the environment or workplace security.
The tank specifications include compliance markings that are added as certifications. Regardless of type, all vessels must adhere to high-pressure vessel regulations.
Compressed Air Tanks
Since the majority of compressed air systems for industrial and manufacturing plants operate at pressures of 5 to 6 barg, this type of tank is likewise covered by the ASME Boiler and Pressure Vessel Code.
Air receivers and air buffer vessels are frequently constructed from stainless steel tanks. The purpose of wet-type air receivers is to store air while reducing moisture by allowing water vapour to condense inside the container and then be drained to the tank blowdown. It is vital to utilise corrosion-resistant materials because air and moisture are present.
Knowing The Different Types And Grades Of Stainless Steel Tank Is Vital For An Effective Usage
When searching for a stainless steel tank, understanding the different characteristics of the various grades is essential for both safety, durability and functionality.
Looking for a quality stainless steel storage tank fabrication company in Malaysia? Choose Choong Ngai Engineering!
So, if you're looking for stainless steel tank fabrication in Malaysia, visit us at
Choong Ngai Engineering today to speak to our experts. We at Choong Ngai Engineering have years of experience and knowledge to answer your doubts or concerns, and we ensure to provide you with the quality solution you're looking for.
Call us now!