What Is Arc Welding: Advantages And Disadvantages
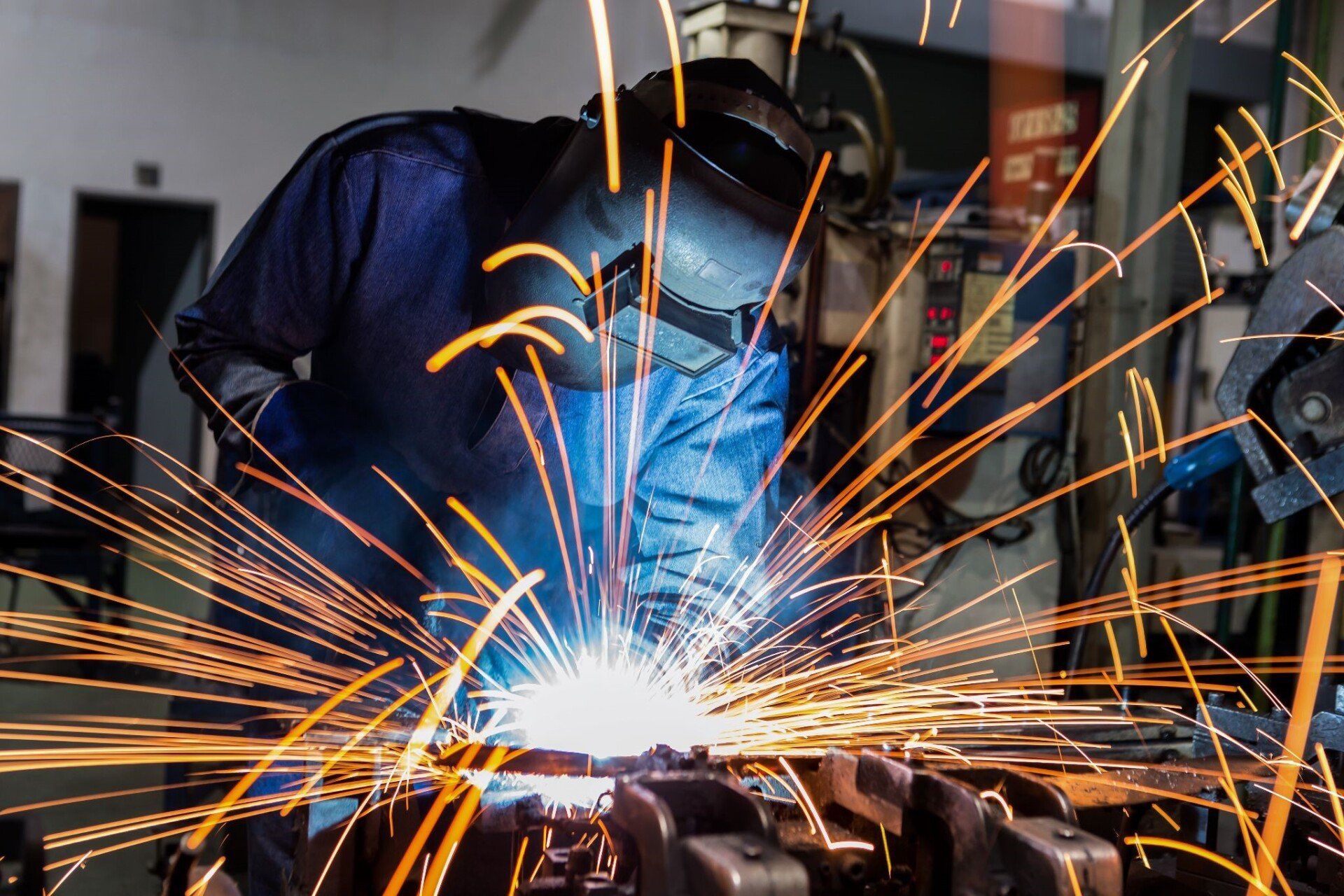
Welding is a connecting method that is utilized in nearly every industry. The engineers who work in the welding department must be well-versed in the specifics of the various joining methods.
Due to its simplicity, arc welding is the most popular type of welding method in the metal welding services in Malaysia. Despite the fact that the technique has a number of difficulties, there are specific applications for which it can be used.
So, what is arc welding, and what are the benefits and drawbacks that come with it? Let's take a closer look.
What is arc welding?
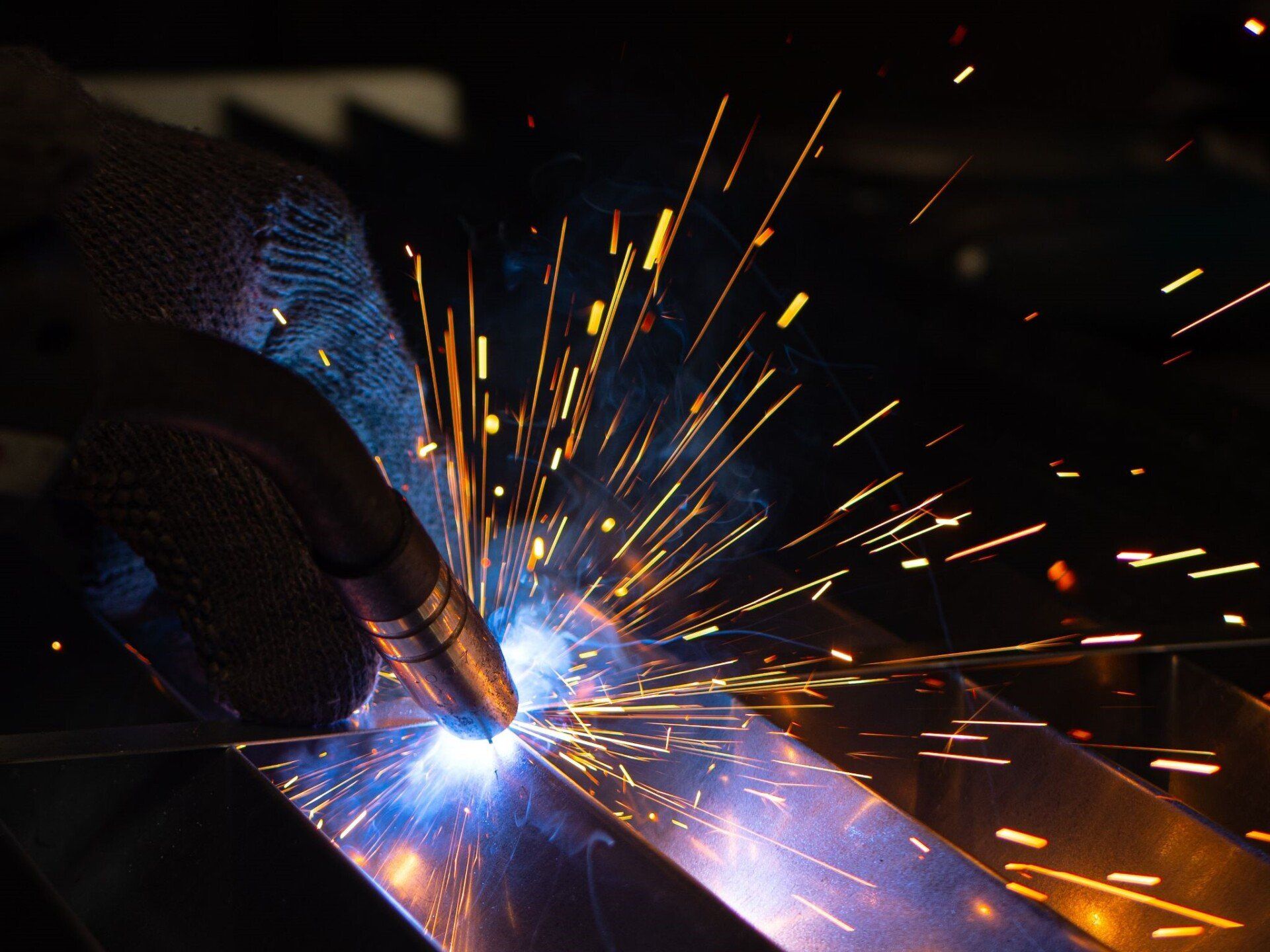
Arc welding uses electricity to join metal, in this case, steel. In contrast to the majority of other methods, which often employ gas, this method makes use of electricity to provide enough heat to melt the metal and join it together during cooling.
Arc welding is frequently used in a variety of significant building projects, such as:
- Heavy equipment repair
- Pipeline welding
- Steel erection
- Vessel manufacturing
- Tank welding
- Construction of ships, rails, bridges, roofs
- Pressure vessels
In the latter half of the 19th century, arc welding was initially created and was employed in shipbuilding during World War II. This procedure has emerged as one of the quickest and most popular welding methods in today's manufacturing businesses.
Advantages of Arc Welding
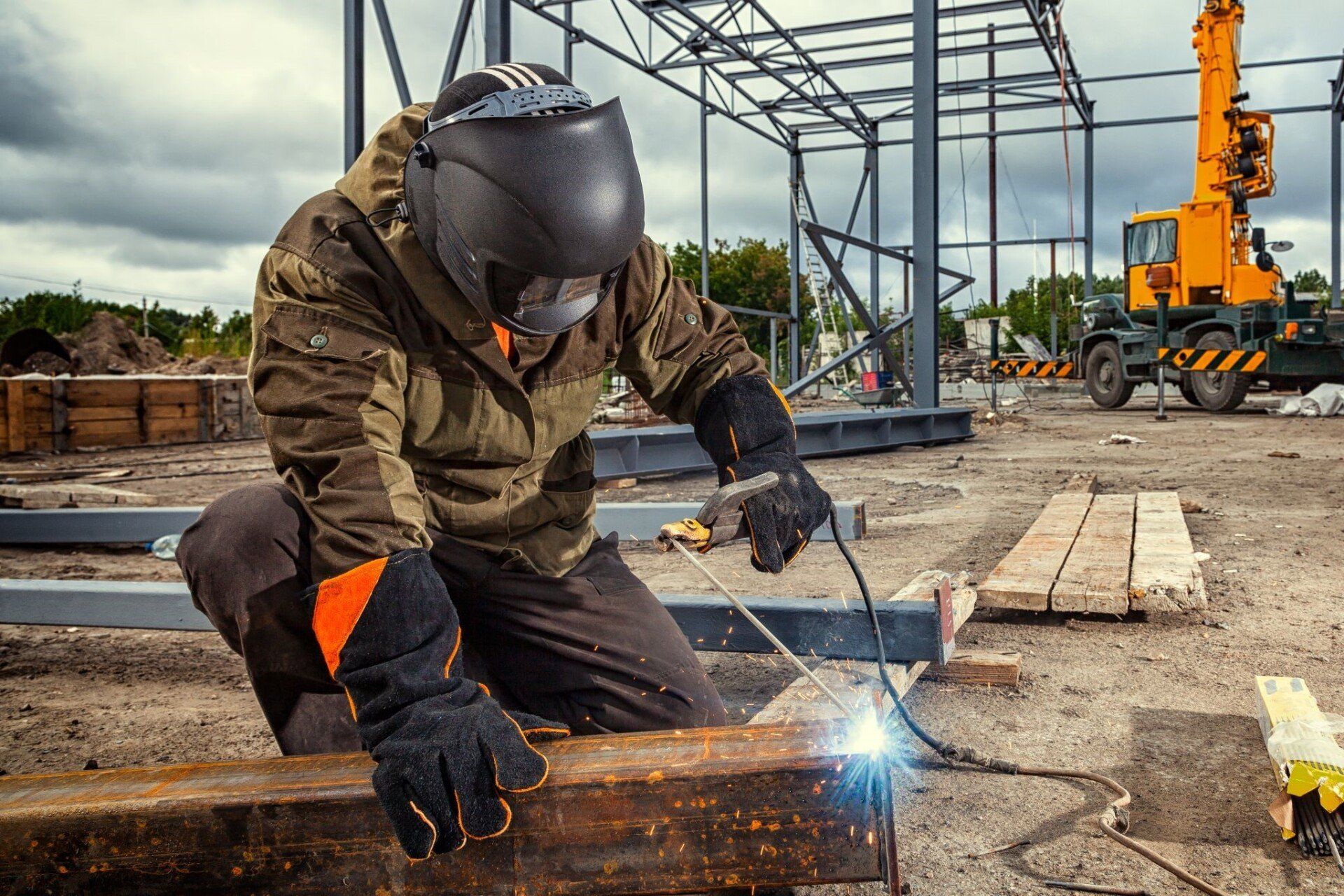
Compared to many other welding methods, arc welding has many benefits. Among the advantages of arc welding are:
Cost
Arc welding gear is reasonably priced and cost-effective, and since gas isn't used, the method frequently starts off needing less equipment.
Portability
It is simple to bring the welding equipment for operations outside because it is portable. Where there is electricity, its power source can be utilised. Alternatively, generators can be used as a backup if no electricity source is available.
Durability
There is no need to clean the surface, and the process of arc welding can be performed immediately on unclean metals. Besides that, it also has a high impact strength and low corrosion resistance. Any environment is suitable for the process of arc welding, and the beads can be used to make designs on delicate metals.
Great results
With arc welding, smooth welding and strong joints can be achieved with minimal distortion at a high speed compared to other welding techniques.
Minimal Storage Space
The equipment needed for arc welding is small and light; thus, there isn't much storage space required. Businesses with little storage space will find this to be beneficial because they can accommodate arc welding equipment without any issues or challenges.
Disadvantages of Arc Welding
Let's take a closer look at the disadvantages of arc welding and why some welders may want to use another method for their projects instead.
Lower efficiency
Arc welding typically produces more waste than many other techniques, which can sometimes result in an increase in project costs.
Requires high skill level
Arc welding project operators require a high level of expertise and training, which not all specialists have.
It does not work well on thin metals
Some thin metals cannot be welded using arc welding.
Safety Issues Relating to Arc Welding
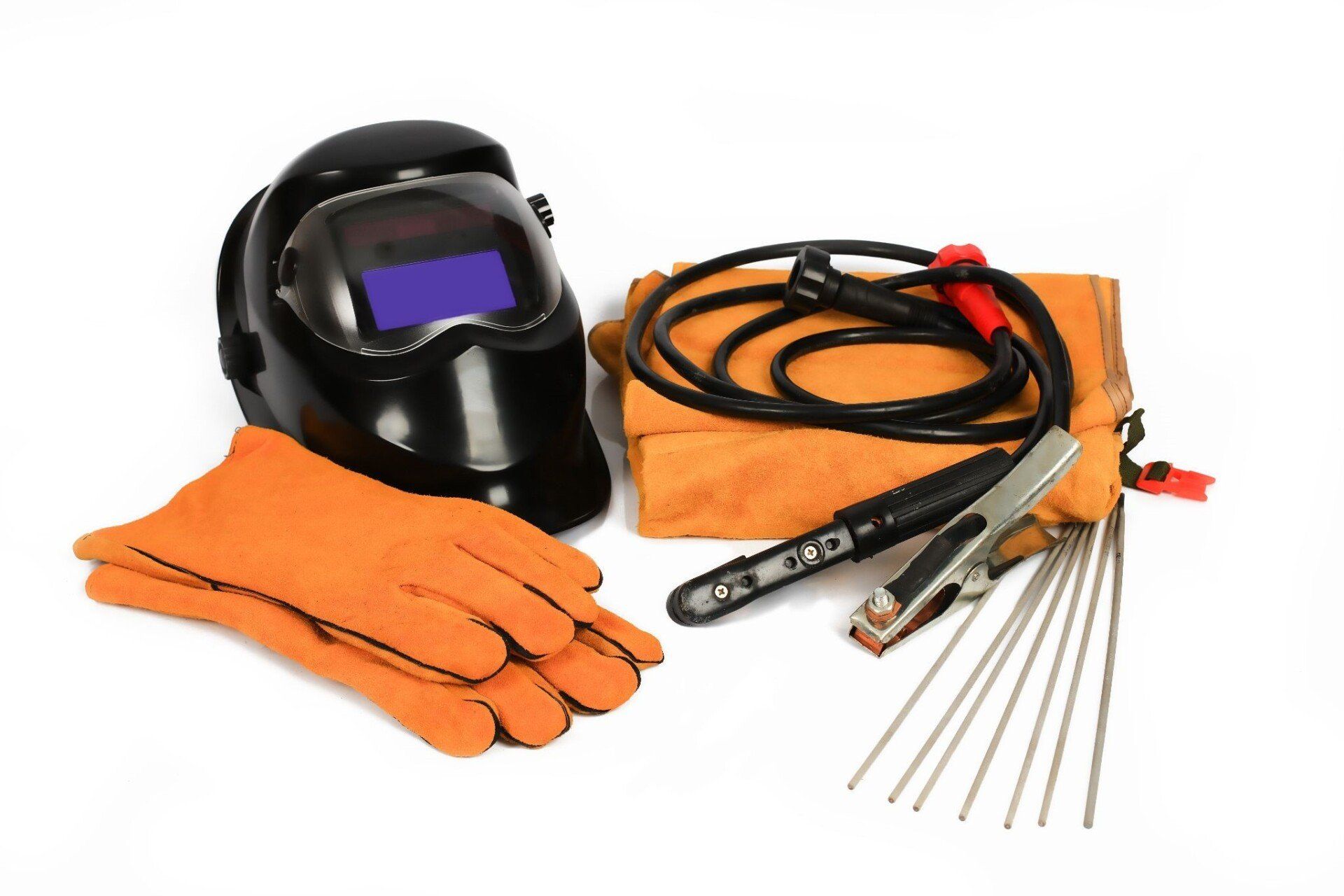
Improper safety measures can make welding a risky and harmful activity. Welding requires the use of an appropriate PPE (Personal Protective Equipment) Kit. The primary health-related issues are as follows:
Inhaled substances
Welders are exposed to a variety of potentially hazardous materials while welding. The smoke created, for instance, during flux-cored welding contains a number of hazardous oxides. Therefore, before beginning any welding procedure, we should shield our faces.
Potential harm to eyes
The eyes can sustain significant damage from the high-Intensity spark produced by this welding procedure. When looking at the welding process directly, the eyes can turn red and cause pain for days. As a result, welding goggles must be worn to safeguard the eyes while welding.
Heat, fire, and Explosion Hazards
Welding can generate a lot of heat since the temperature rise in the core can reach up to 3593 degrees Celsius. The sparks can land on the body, or an explosion could occur. As a result, we need to protect our bodies with appropriate gear while welding. Additionally, we need to watch out for any explosive materials that might be nearby the welding area.
Looking for arc welding services in Malaysia ? Visit Choong Ngai Engineering now!
Prior to selecting a welding technique, it is crucial to consider the complexity and quantity of the parts that will be welded. Time and cost plays an important role as well so be sure to keep that in mind.
If you're looking for a reliable quality welding services provider in Malaysia, look no further than
Choong Ngai Engineering Works. We are a leading provider of
quality welding services Malaysia and provide the best possible service to our clients.
Contact us now!