What Is Metal Spinning And What Are Their Advantages?
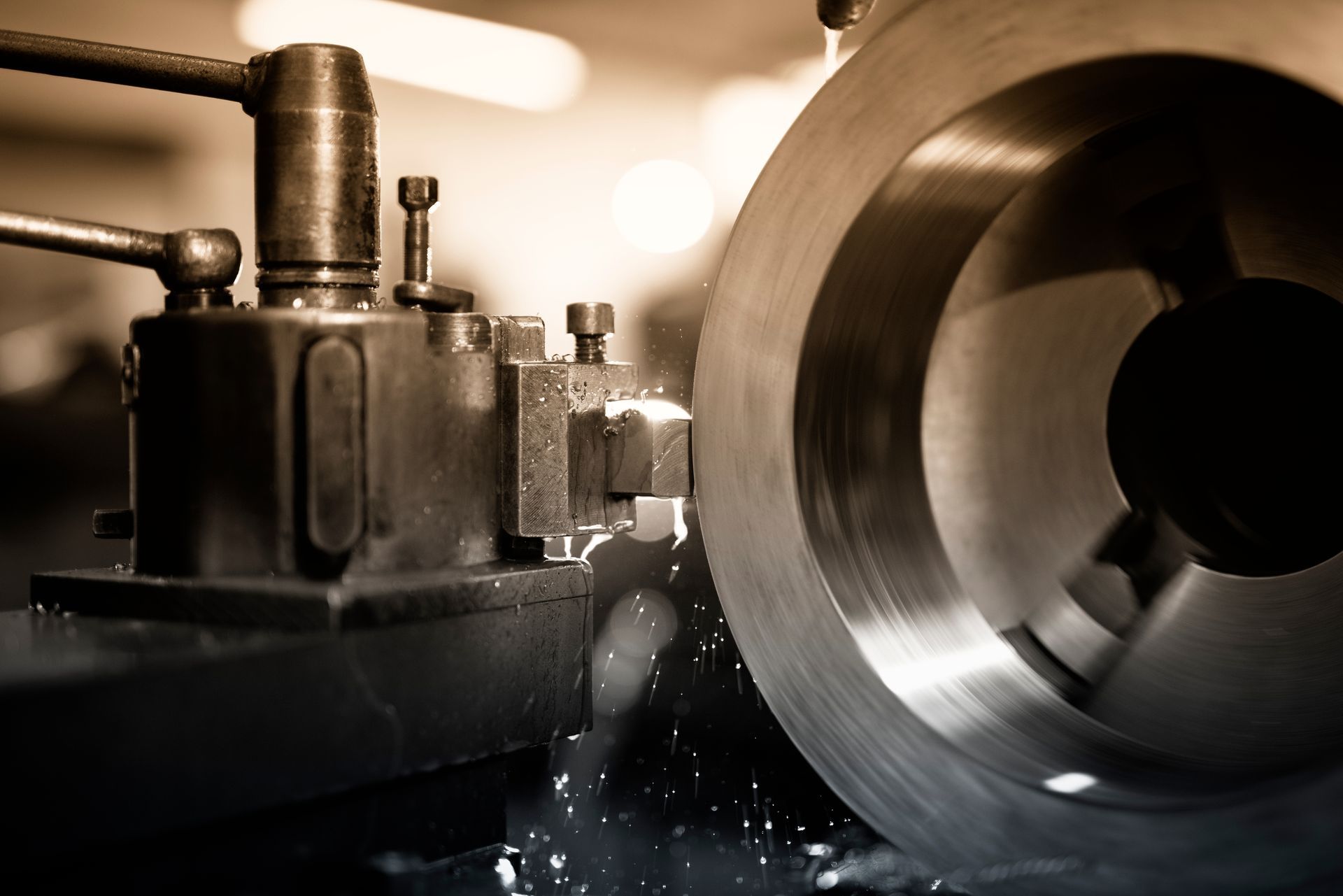
Metal spinning may sound like a dance move, but it's an intriguing art form that has been shaping metal into appealing and valuable forms for centuries in fabrication and crafting. If you're unfamiliar with the term, we're here to explain what metal spinning is and all of its excellent benefits.
So, whether you're an aspiring artisan, an engineering enthusiast, or simply interested in the magic that happens when metal meets spin, follow along as we explore the world of metal spinning and discover why it's more than just a mesmerising display of artistry.
What Is The Process Of Metal Spinning?
Metal spinning, or spin forming, is a metal shaping technique that creates axially symmetrical round structures from a flat, circular, blank or disc-shaped object. It is done by applying lateral force using a mandrel that is spinning quickly on its axis and a roller that is positioned up against the disc blank's surface.
The mandrel supports the workpiece, which also gives it its final shape. A circular metal sheet is bent into various shapes during the metal spinning process without removing any metal from the workpiece. The disc blank is wrapped over the mandrel and spun while subjected to tensile and compressive forces.
Based on the type of metal spinning used, the thickness of the initial metal sheet can be lowered, which is a precision-controlled characteristic to ensure the processed metal meets the specified criteria.
The Different Types Of Metal Spinning
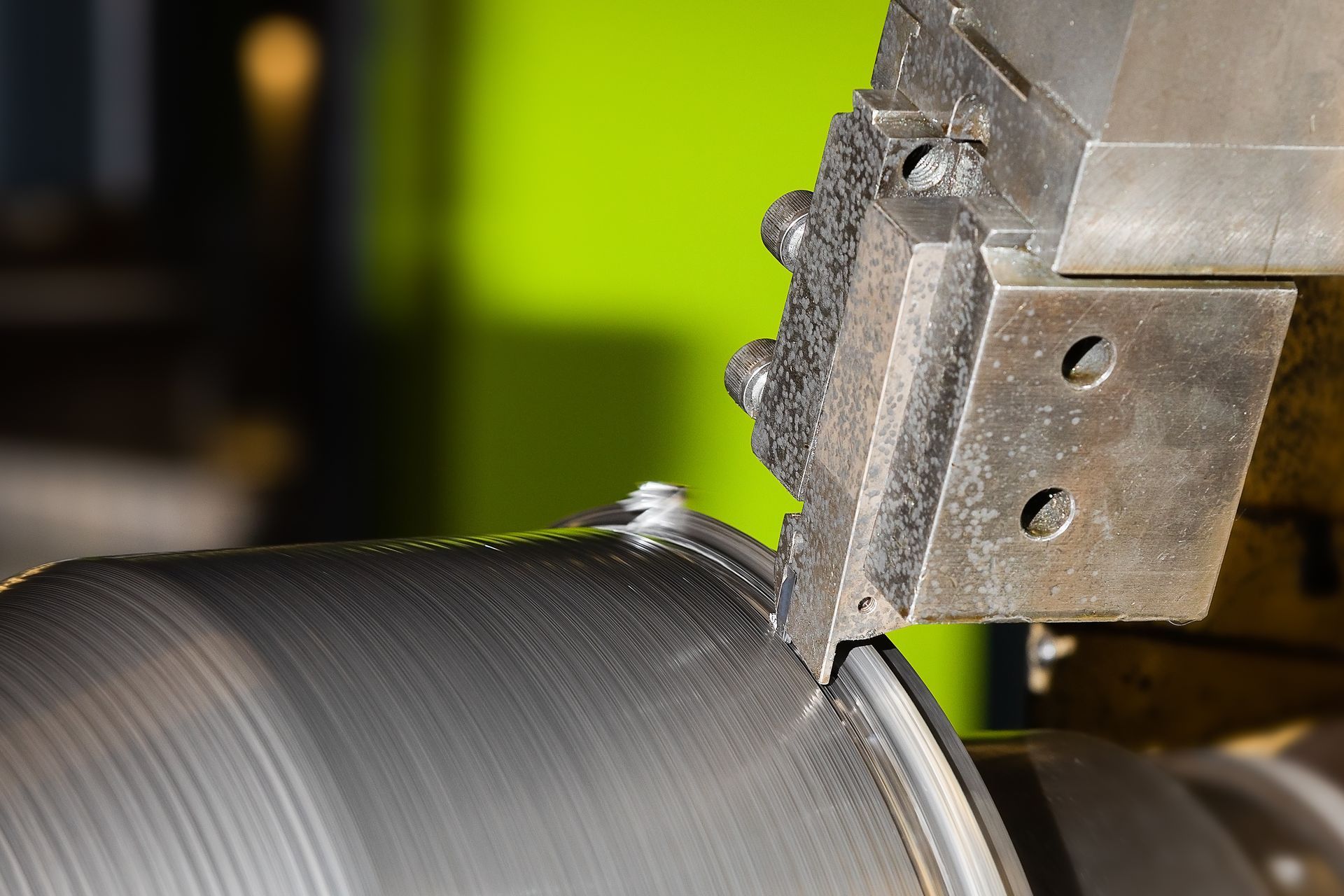
Metal spinning is not a one-size-fits-all process; it is a diverse metal shaping art with various techniques that cater to diverse demands and outcomes. Let's take an in-depth look at the different types of metal spinning processes, each of which offers a special set of characteristics and uses.
Conventional Metal Spinning
In conventional spinning, the workpiece is pushed by the roller across the mandrel's shape. During the entire process, the workpiece's material thickness is constant. After the metal shaping process, the workpiece's diameter is decreased while its depth increases.
It is regarded as the most basic form of metal spinning and calls for less complex equipment and tools.
Shear Spinning
During shear spinning, the object moves along the mandrel's contour under the force of the rollers. While the final part's material thickness is lower than it was in its initial blank form, its diameter doesn't change. As the workpiece gets deeper, so does its depth. Since the workpiece is subjected to more compressive forces, its mechanical qualities improve.
Shear spinning influences the component's dimensional accuracy and surface finish, requiring a more durable tooling design and accurate machining control. It increases the amount of friction on the workpiece and wear on the mandrel. Since this metal shaping method produces a lot of heat, coolant is required.
Hot Spinning
In hot spinning, a heating torch is used to increase the workpiece's temperature to forging levels. The workpiece is pressed over the mandrel with the heating flame. Hot spinning is used when a material has low ductility and malleability or if the metal sheet is excessively thick and, therefore, challenging to deform at room temperature.
Hot spinning significantly deforms the workpiece because it is already distorted due to its plastic condition, and it also refines the grain structure, giving the workpiece better physical qualities like greater durability. But the metal that has been heated quickly oxidises. The whole process is more expensive and challenging to manage.
Tube Spinning
Tube spinning is a type of shear spinning used to lengthen and compress the walls of hollow cylindrical tubes. The tube is initially placed and clamped in the mandrel. By placing three or more rollers evenly spaced around the tube, the tube is drawn over the length of the mandrel. The axial flow of material moves in a similar manner to how rollers move.
Tube spinning can be done in the mandrel either externally or internally. During external tube spinning, the tube is stretched across the mandrel's exterior surface. Internal tube spinning includes stretching and spinning the tube inside of a hollow mandrel.
The Various Advantages Of Metal Spinning
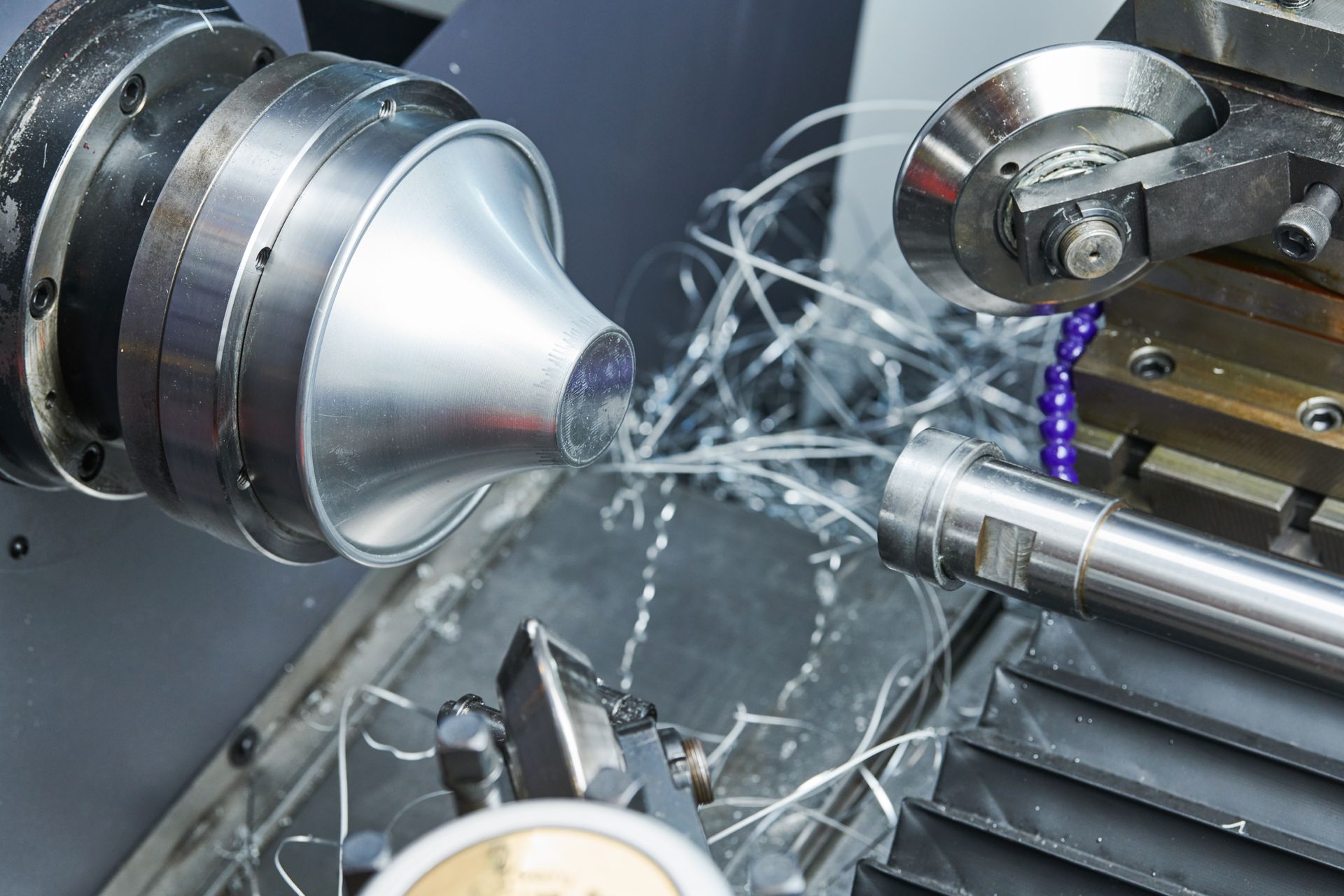
In this section, we will look at the outstanding advantages of metal spinning and explore how its adaptability, effectiveness, and precise outcomes make it a vital tool for fabricators and designers.
Budget Friendly
Metal spinning requires the least tooling and setup compared to other metal shaping techniques. This correlates to less expensive tooling and quicker turnaround times, making it a cost-effective option for both production and prototyping.
Quick Turnaround Time
Metal spinning allows for quick part fabrication due to its easy process and streamlined tooling setup. This is beneficial for sectors with tight deadlines or evolving needs for design.
Flexibility
Metal spinning is excellent at creating intricate, symmetrical, seamless structures that might prove difficult or expensive to accomplish with traditional methods. Additionally, this metal shaping technique offers exceptional design versatility, allowing for the creation of spheres, cones, and complex shapes.
Metal Shaping Is A Technique That Promotes Efficiency And Creativity
In addition to being a centuries-old technique, metal spinning is an incredible example of engineering and craftsmanship that has a number of benefits. This metal shaping technique is useful in a multitude of industries and applications due to its low cost and ability to shape intricate shapes, as well as its efficiency in manufacturing a high-quality surface finish.
Looking for a metal bending service in Malaysia? Try Choong Ngai Engineering
If you're looking for metal bending services in Malaysia, visit us at
Choong Ngai Engineering today to speak to our experts. We at Choong Ngai Engineering have years of experience and knowledge to answer your doubts or concerns, and we ensure to provide you with the quality solution you're looking for.
Call us now!