7 Benefits Of Metal Fabrication In The Medical Industry
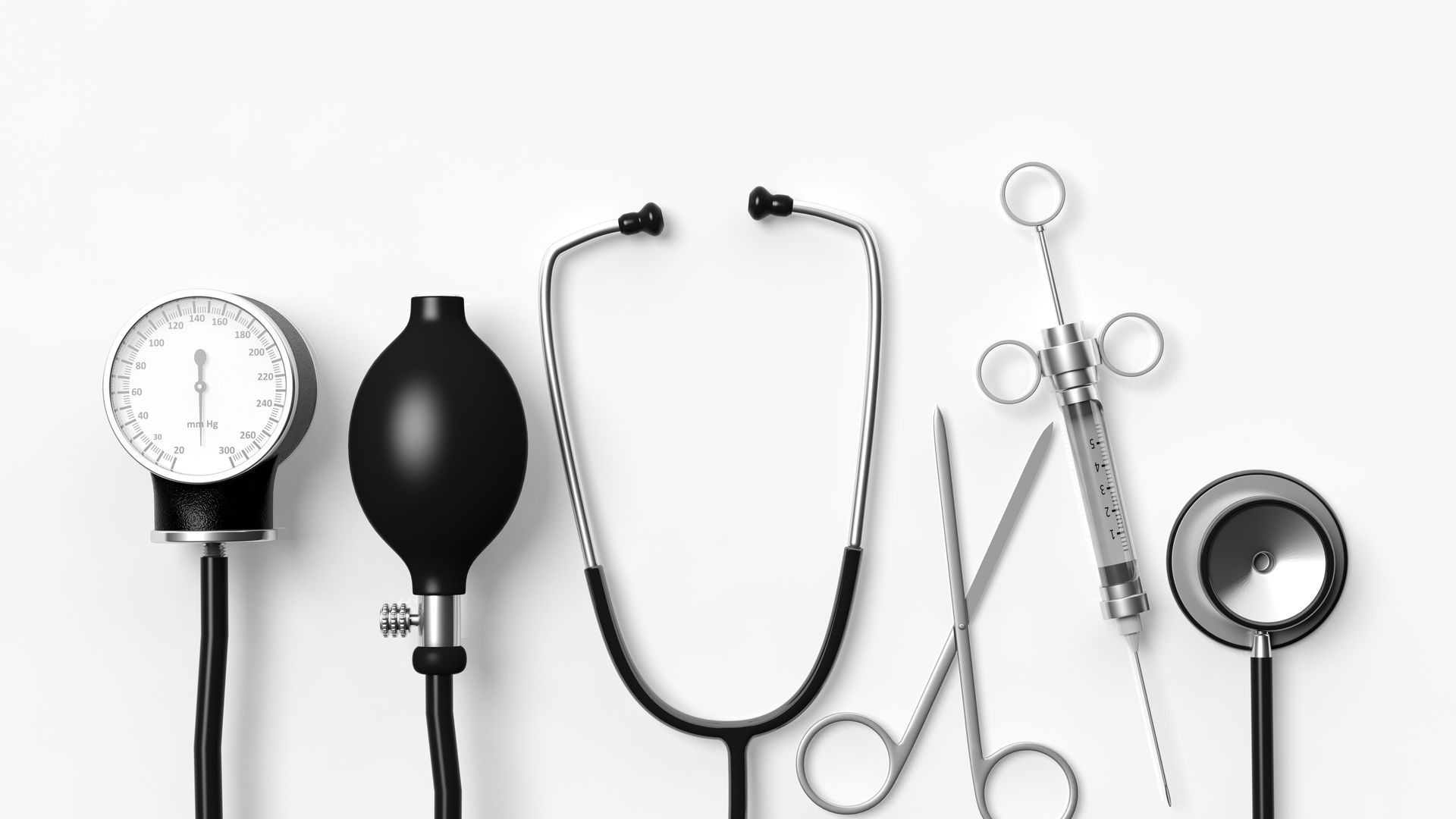
There is no denying that metal fabrication has numerous advantages for the medical sector, which is why the two have a long-standing relationship. The medical industry relies heavily on metal items, and the majority of their instruments are produced using various manufacturing techniques.
All kinds of equipment, systems, as well as tools utilised by hospitals and clinics around the globe, are made up of these components. Metal fabrication is still one of the most effective methods to fulfil medical industry standards since valuable metal qualities are handled by advanced machinery and software.
How Does The Medical Industry Benefit From Metal Fabrication?
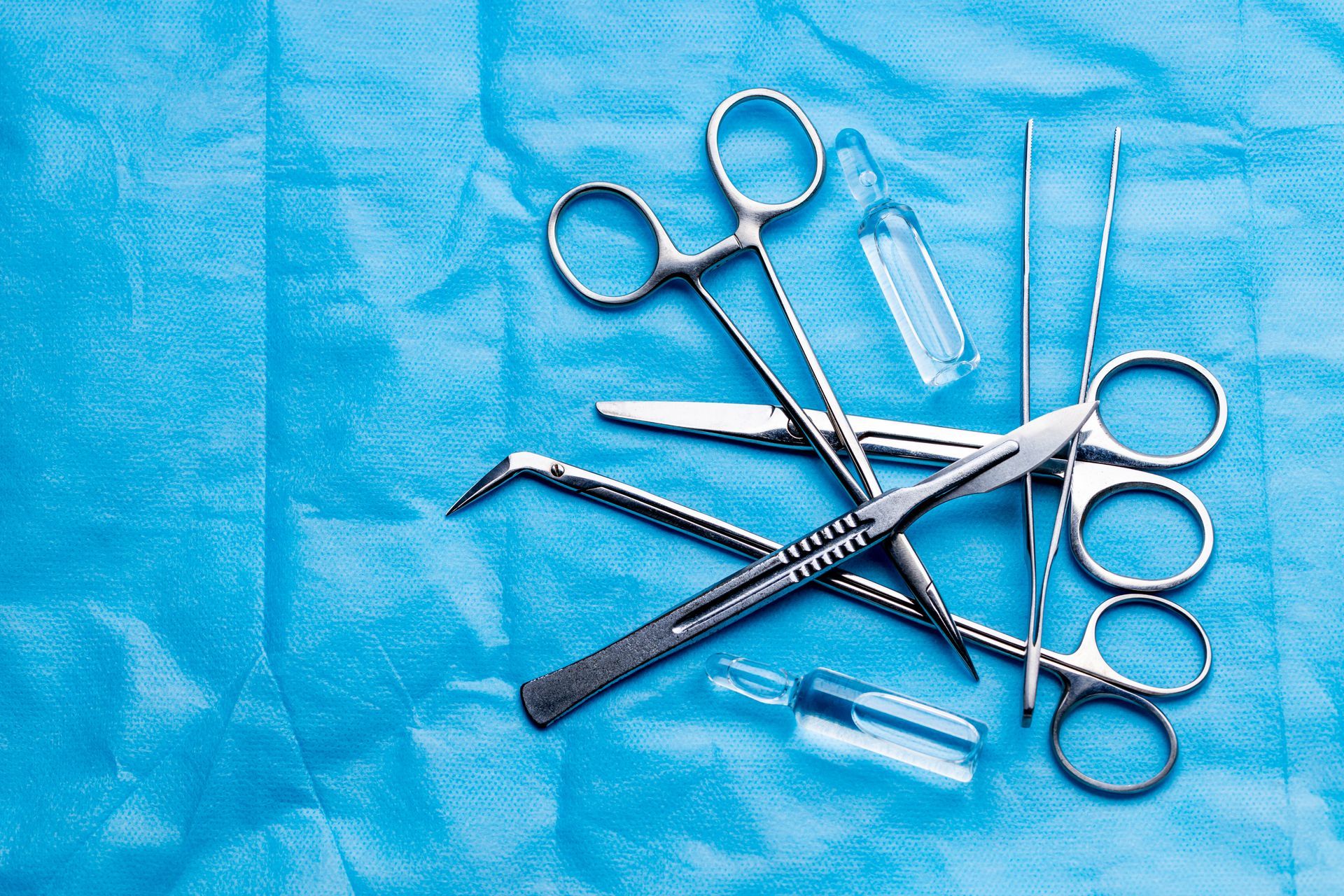
For the medical sector, custom metal fabrication is essential. The industry requires tools with specific features. Specific requirements of the medical industry can be met with this customised procedure by engaging a fabricator to produce this distinctive medical equipment. Using custom sheet metal fabrication in the healthcare industry has a number of advantages.
Durability
Despite being more affordable, sheet metal is highly reliable and long-lasting. It is also resistant to corrosion and heat. The objects that are designed will hold up well throughout time with sheet metal. For example, ablation systems, which involve heating aberrant tissue to destruction, utilise equipment from these production methods.
Given these advantages, it is clear that custom sheet metal fabrication is a durable and affordable choice for producing incredibly precise modern tools for the medical sector.
Enhanced Accuracy
With any medical instrument, accuracy is vital. A patient could suffer greatly with a single uneven edge or misshaped device. There can be no errors when undergoing duties like surgery, post-operative care, and other medical treatments. All medical devices must be constructed with extreme precision without sacrificing quality in order to guarantee patient safety.
Before starting a production run with metal fabrication, most manufacturers conduct simulations. By doing this, potential flaws can be identified before they occur and give designers plenty of time to find a solution.
Modern technologies like camera vision systems and sensors further support this. Before a product leaves the production line, those gadgets can examine the metal's dimensions as it passes through various machinery and spot defective goods.
Furthermore, the majority of metal fabrication procedures are now automated, considerably reducing human error and increasing precision. Automated production methods are significantly better than manual labour since they can produce items that are highly accurate and in large quantities.
Cost Effective
Custom sheet metal fabricators can quickly produce the desired design using the latest computer-aided techniques. The fabrication process is more adaptable now than it has ever been, from the original sketching to the delivery of the finished product.
Additionally, even after manufacturing has started, redesigning can be done using the custom fabrication technique to integrate last-minute adjustments.
Customisation
Standard metal instruments are not appropriate for multiple medical procedures. The healthcare industry can use this fabrication technique to create specialised medical equipment, including tools and hospital beds. Depending on the requirements, the following features of the medical equipment can be customisable, including:
- Material
- Design
- Size
- Calibration
For example, automated devices utilising sensitive sensors and switches are used in system-level control mechanisms. With the help of this method of custom fabrication, instruments that are calibrated to the necessary dimensions can be created.
Shorter Turnaround Time
Regarding everything having to do with the medical sector, time is of the essence. As a result, it's imperative to manufacture new instruments, tools, and equipment quickly. To provide patients with the highest level of efficiency, hospitals need their requests for new equipment and stock to be fulfilled as fast as possible. Medical firms are able to quickly meet supply demands when they use metal fabrication methods.
A quicker turnaround time is also a result of this shortened production time. Rapid manufacturing capacity can help businesses keep up with new technology and equipment as the medical profession grows at an alarming rate. This can also allow a company to create new items and keep up with emerging care methods.
Inventive Equipment
The metal fabrication business regularly evolves to keep up with the latest innovations, especially in the medical sector. These days, techniques like laser cutting and metal stamping can produce thousands of intricate parts in a single minute. This speed and accuracy are valuable assets for businesses in medicine and healthcare.
The majority of medical devices need a wide variety of specially constructed metal elements to operate, such as:
- Gears
- Springs
- Brackets
These items are created using specialised machinery like water-jetting and laser-cutting devices.
Reliability
The services and fabrication techniques offered by any metal producer can vary. By selecting a reliable business, you can be confident that your orders will be completed using durable tools and machinery, which will influence both the output's speed and quality. Any minor production inefficiencies or mistakes can result in defective instruments and increase overall costs. The metal manufacturing business takes precautions to prevent this.
To make instruments, medical equipment producers must possess a specific certification. Some manufacturers will go above and beyond the standard and have extra regulations to guarantee quality. These strict criteria contribute to the development of an efficient sector capable of producing medical equipment.
Quality Control For All Medical Instruments Are Vital For The Industry
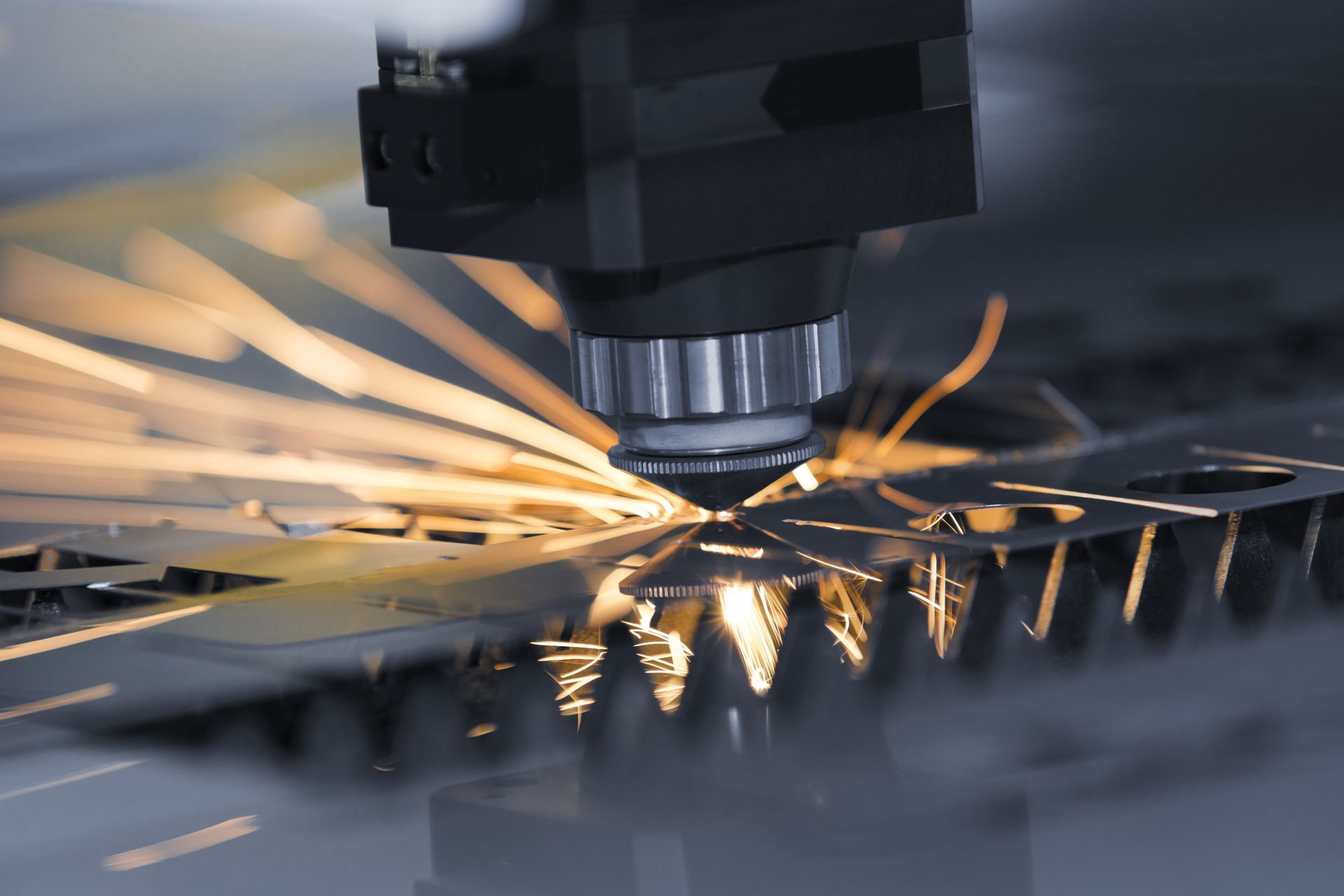
New Paragraph