The Various Types Of Cutting Tool Materials And Their Uses
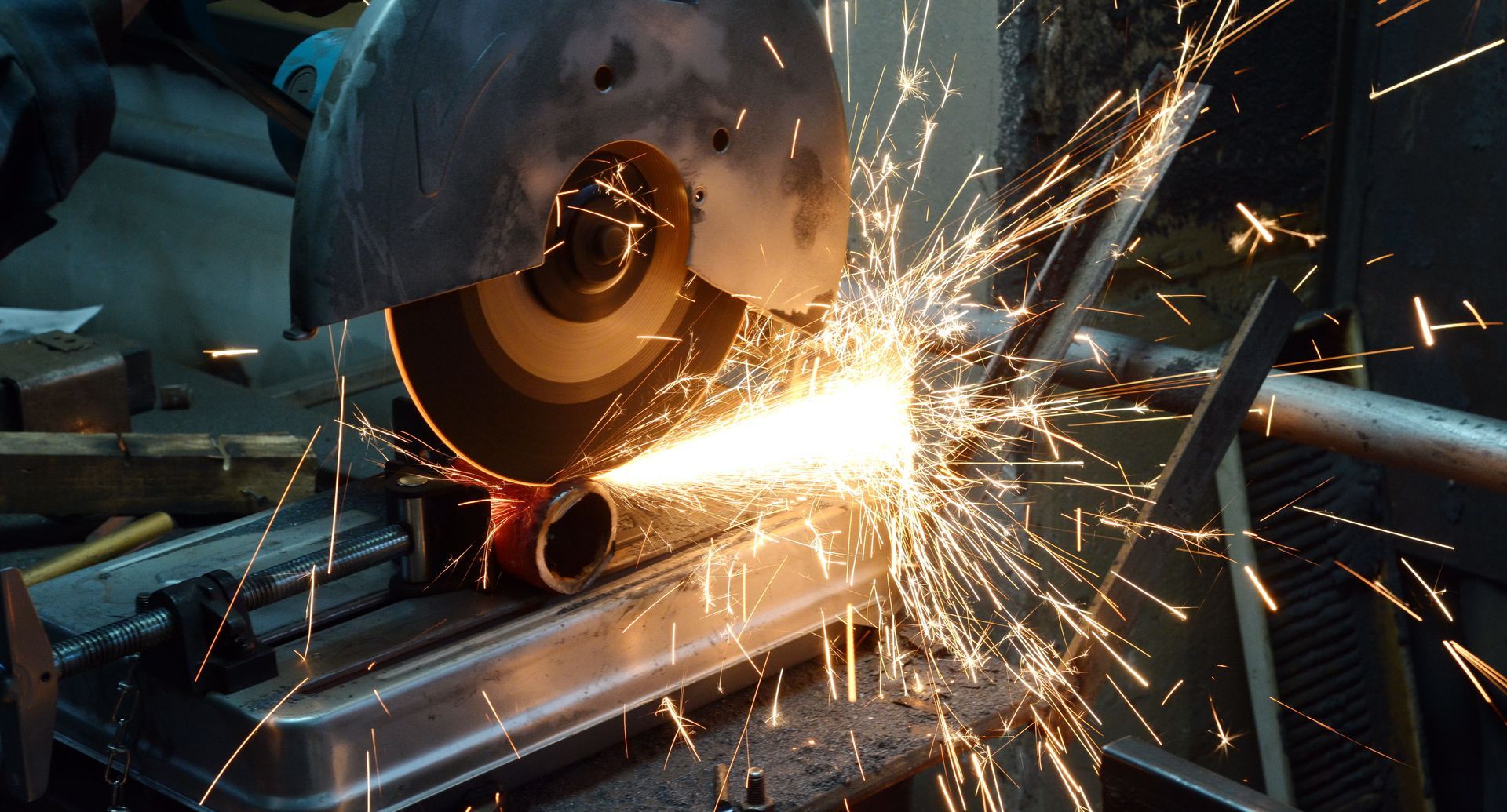
With the swift growth of tool materials, various new tool materials' physical, mechanical, and cutting capabilities have substantially improved. This also means the various ways to apply these tools have also grown throughout the years.
However, with cutting tools being exposed to friction, stress, vibration, high pressure, and high temperature, the material used in your cutting tools plays a major factor. Hence, the material for the tools should possess fundamental qualities such as toughness, heat resistance, and durability.
Here’s what you need to know about the types of cutting tool materials and more.
What Are The Various Types Of Cutting Tool Materials?
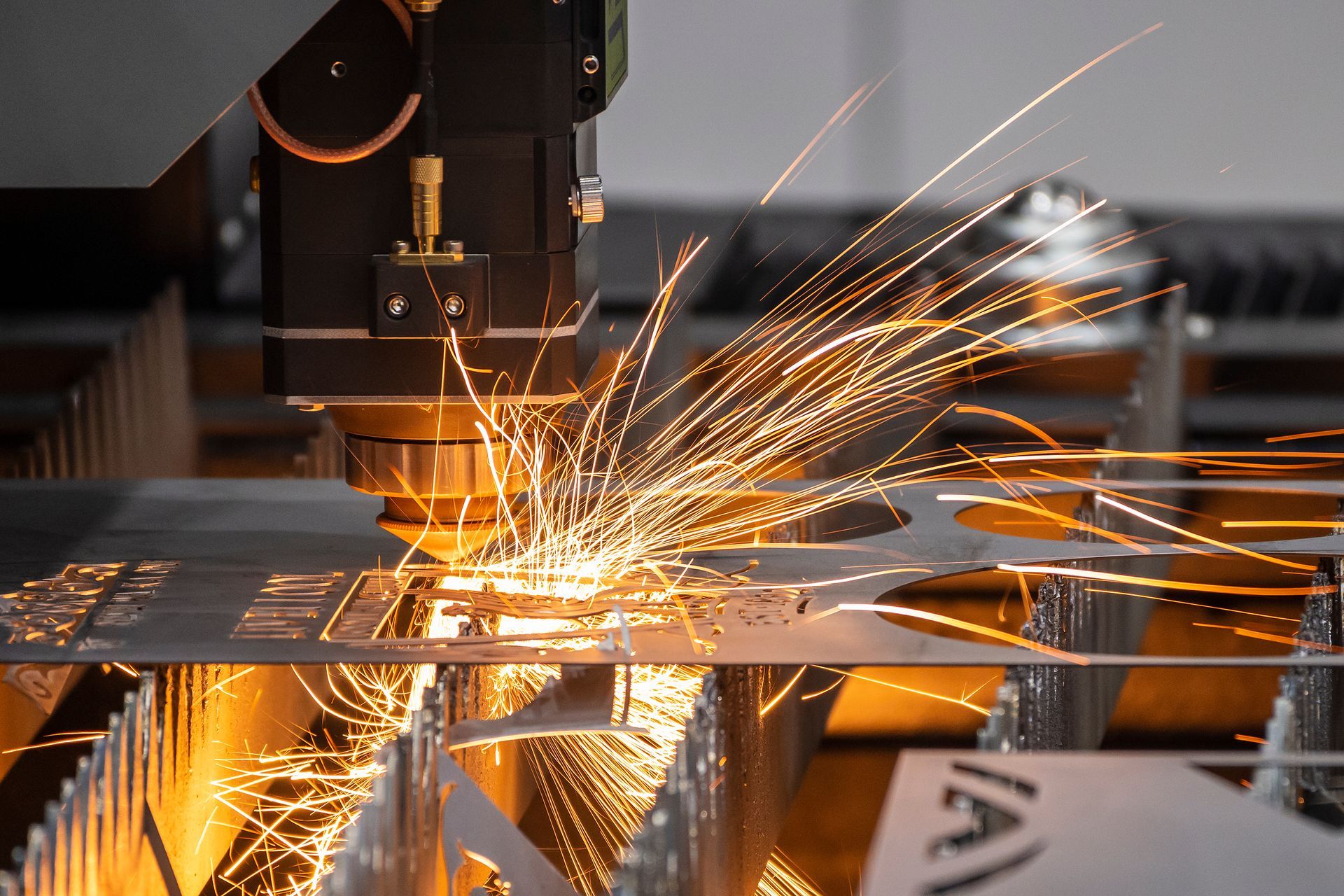
Currently, the most common CNC (computer numeric control) tool materials include diamond, cubic boron nitride, ceramic, coated, carbide, and high-speed steel tools. There are several overall grades of tool materials, and they offer a wide range of performance.
The type of machining to be done on the workpiece and the tool material must be chosen before beginning a CNC machining operation. However, the material choice for the tool must be suitably matched to the processed item.
To achieve the longest tool life and highest cutting efficiency, it is vital to match the following properties of the cutting tool material and processing product:
- Mechanical
- Physical
- Chemical
So, let's take a look at the various types of cutting tool materials.
Diamond
The most resilient material ever discovered in nature is an allotrope of carbon, which is present in diamonds. In the fabricating of non-ferrous and non-metallic materials, diamond tools are frequently employed due to their following characteristics:
- High hardness
- Enhanced wear resistance
- High thermal conductivity
Diamond tools are the type of cutting tools that are challenging to replace, particularly in the high-speed cutting of aluminium and silicon-aluminium alloys. Modern CNC machining relies heavily on diamond tools that achieve great efficiency, high stability, and extended life.
Non-ferrous and non-metallic materials are cut and drilled with diamond tools at high speeds. It can process a wide range of wear-resistant nonmetals, including glass fibre-reinforced plastic powder metallurgy blanks, ceramic materials and more.
Cubic Boron Nitride
Next only to diamonds in regards to hardness and thermal conductivity, cubic boron nitride (CBN), which is produced using a process similar to that used to make diamonds, also possesses exceptional thermal stability. It can be heated to 10,000 degrees Celsius in the environment, and oxidation will not take place. Due to its exceptionally stable chemical features for ferrous metals, CBN is often used in the production of steel products.
Cubic boron nitride can be used to finish a variety of hardened steel and other challenging-to-cut materials, including:
- Hard cast iron
- Superalloys
- Cemented carbide
- Surface-sprayed materials
Coated
One of the key strategies for enhancing a tool's performance is coating it. A significant improvement in the cutting performance of tools has been obtained by coated tools. The coated tool has one or more layers of a refractory compound with good wear resistance applied to its robust tool body, combining the tool matrix with the hard coating to increase the tool's performance.
Tools with coatings can offer the following benefits, including:
- Increase machining productivity
- Increase machining accuracy
- Prolong tool life
- Lower machining costs
The most significant tool type in the field of CNC machining will be coated tools, which have incredible potential. To satisfy the demands of high-speed machining of various steels, coating technology has been applied to the following:
- End mills
- Reamers
- Drills
- Compound hole machining tools
- Gear hobs
- Gear shapers
- Shaving cutters
- Forming broaches
- Various machine-clamped indexable inserts
Ceramic
Ceramic tools are difficult to bond with metals, but it offers the following benefits:
- High hardness
- Outstanding wear resistance
- Exceptional heat resistance
- Chemical stability
In CNC machining, ceramic tools play a significant role, and they've emerged as one of the tools for processing materials that are challenging to machine and require high-speed cutting. Thus, ceramic tools are commonly utilised for the following tasks:
- High-speed cutting
- Dry cutting
- Hard cutting
- Cutting of difficult-to-machine materials
When compared to a carbide tool, the ceramic tool's ideal cutting speed can be 2 to 10 times faster, increasing the effectiveness of the cutting process. Furthermore, the earth's crust contains most of the elements that are used as raw materials in ceramic tool materials.
For semi-finishing and high-speed finishing, ceramic is one of the tool materials employed. Ceramic tools can be used to cut the following elements:
- Cast irons
- Steels
- Copper alloys
- Graphite
- Engineered plastics
- Composite materials
High-Speed Steel
With additional alloying elements included, high-speed steel (HSS) is an advanced alloy tool steel. Tools made of high-speed steel perform superbly overall in terms of strength, toughness, and manufacturability. High-speed steel continues to play a significant role in complicated tools and complex cutting tools, such as:
- Hole-making tools
- Milling cutters
- Threading tools
- Broaches
- Gear cutting tools
Additionally, sharpening the cutting edges of high-speed steel blades is easy.
Carbide
The most popular CNC machining tools are carbide tools, particularly indexable carbide tools. Indexable carbide tools have evolved from straightforward turning tools and face milling cutters to a variety of precise, sophisticated, and shaping tools. This, in turn, has also expanded the kinds of integral and indexable carbide tools or inserts to many cutting tool fields.
Carbide-cutting tools are employed for the machining of the following elements:
- Cast iron
- Non-ferrous metals
- Non-metallic materials
Knowing Which Cutting Tool Material Is Vital For A Successful Project
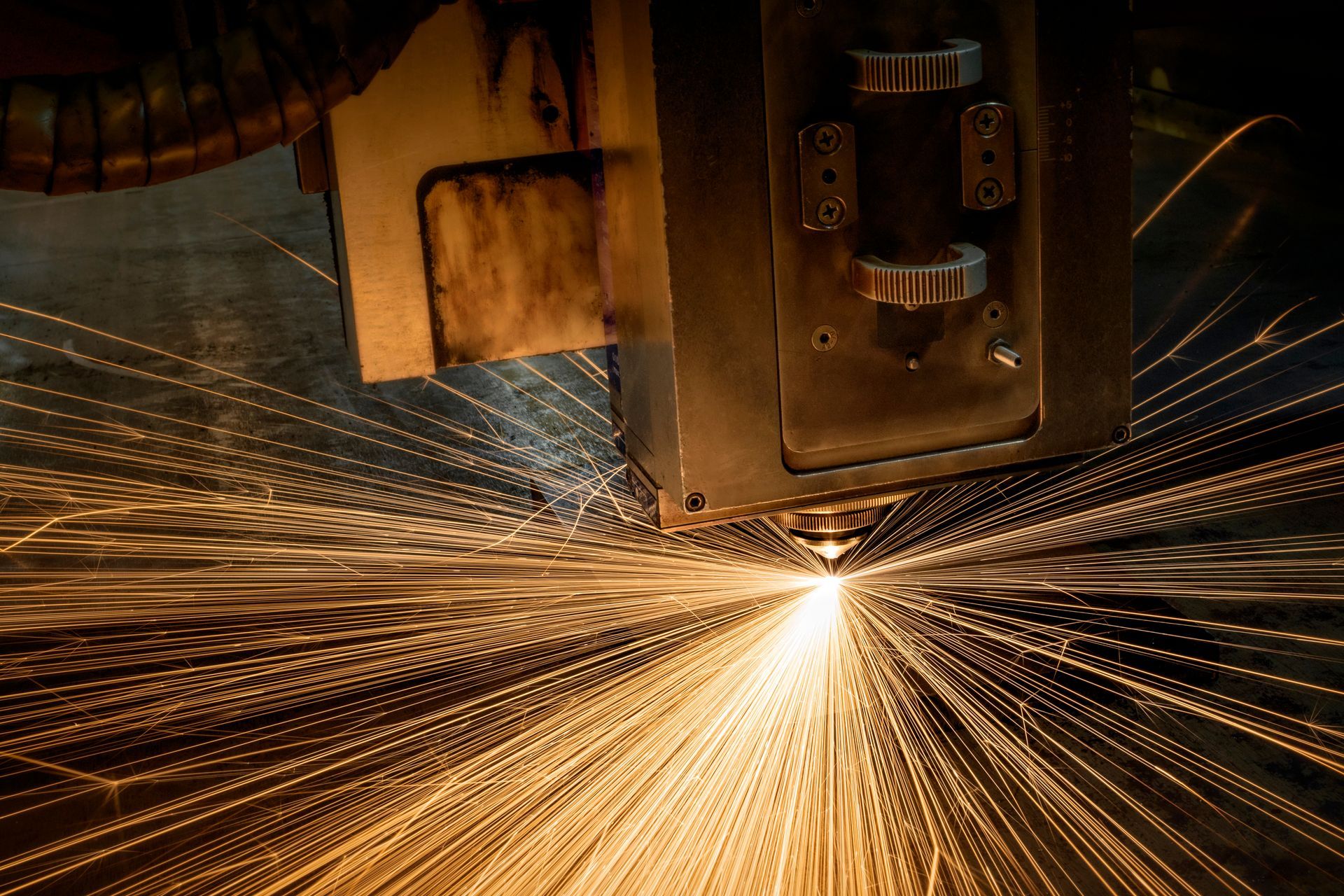
Cutting tools come in a huge variety of shapes, sizes, and materials to fit a variety of machining needs. Manufacturers and machinists can optimise their methods for effectiveness and accuracy by making educated decisions by knowing the properties and uses of various cutting tool materials. As technology and materials science improve, new cutting tool materials are expected to develop, expanding the boundaries of what is possible in metalworking.
Adopting these innovations while staying aware of the most recent improvements would promote innovation and development in the manufacturing sector.
Looking for a quality metal fabrication company in Malaysia? Choose Choon Ngai Engineering!
So, if you're looking for metal fabrication in Malaysia, visit us at Choong Ngai Engineering today to speak to our experts. We at Choong Ngai Engineering have years of experience and knowledge to answer your doubts or concerns, and we ensure to provide you with the quality solution you're looking for. Call us now!