7 Common Types Of Welding Defects And How To Prevent Them
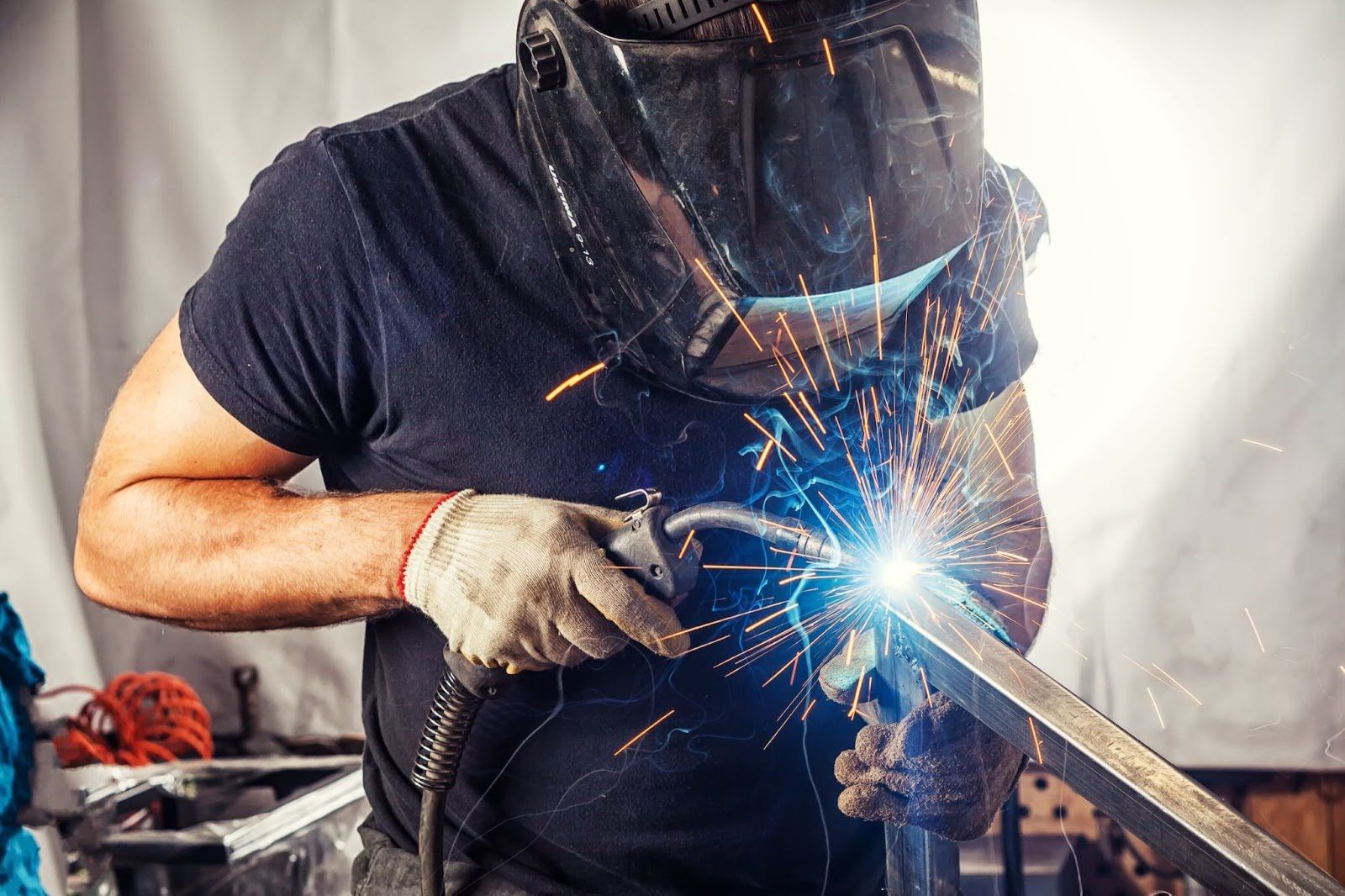
Welding, the modern industrial world's "alchemy," joins metals and other substances with the skill of a surgeon and the durability of a titan. However, flaws can occur in this complex combination of heat and metal. Welding flaws are sneaky rivals that can weaken structures and jeopardise integrity.
In this piece, we'll take a tour of the welding world and look for the most common mistakes. We'll examine every imperfection, from porosity to cracks, identifying their causes and exploring methods to stop them from recurring.
So, whether you're an expert welder or a newbie enthusiast, come along with us as we strive to perfect our craft and make every weld a shining example of our expertise.
Overlap
Overlap happens when the weld's face goes past its toe. As the filler material spreads over the entire weld joint and cools, fusing to the foundation material is difficult.
Proper welding is the best way to avoid the overlap welding defect. The operator may avoid overlap by keeping the welding rod held at the proper angle and moving at a moderate pace. Welding too slowly can also result in an overlap.
Craters
Craters are a frequent welding flaw that develops during aluminium welding. They form at the weld bead's tip. Ignoring craters will create stress points, which will ultimately cause the weld to crack.
Craters can be avoided by properly terminating the weld bead. They occur when the welding is halted before a pass is completed. Additionally, craters can be avoided by filling the space between the tack welds and the weld bead.
Even in the unlikely event that craters form, they can usually be repaired, provided the weld bead is intact. Simply fill in the crater by creating an arc from a point immediately beyond the hole and going back over it.
Porosity
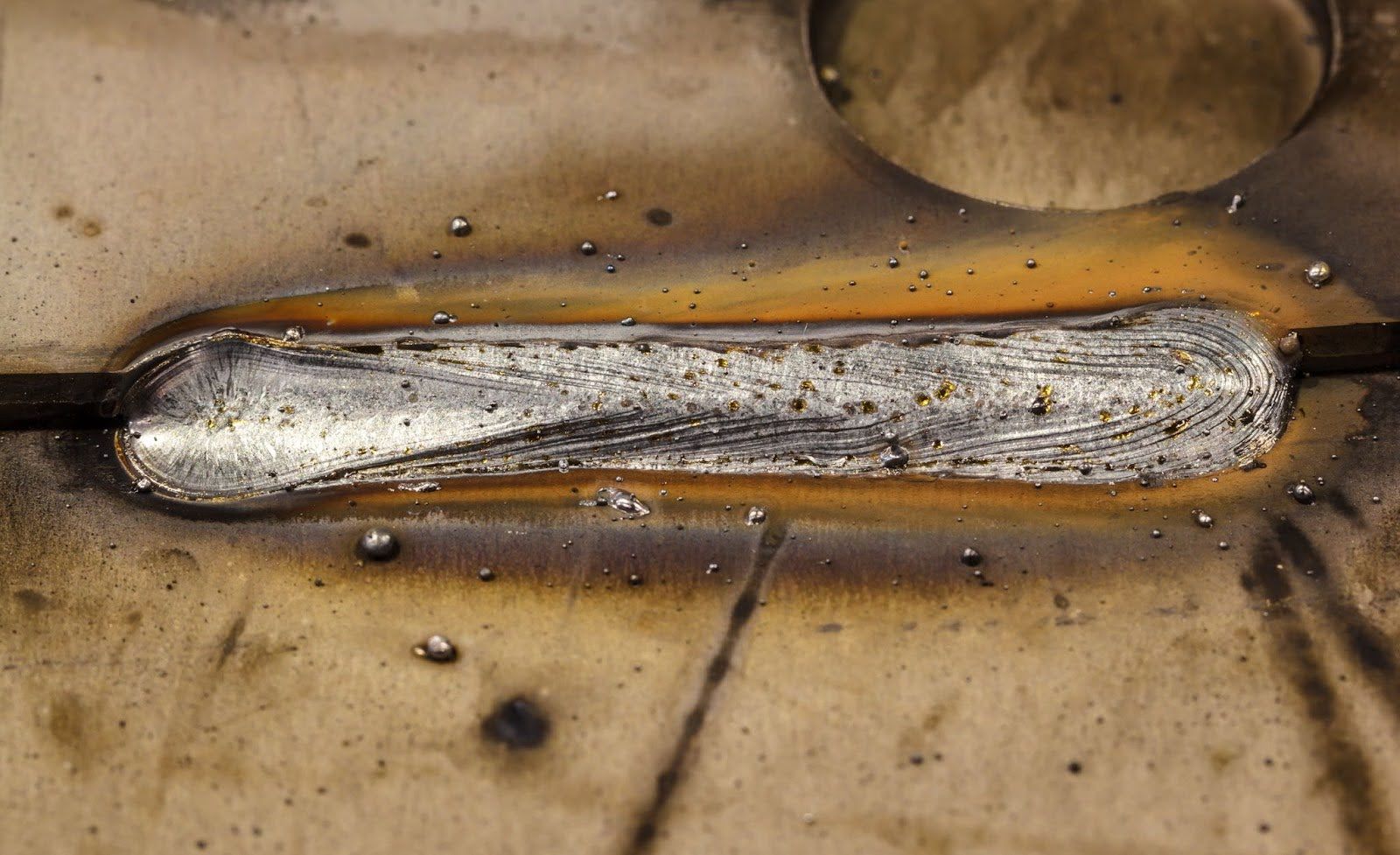
The presence of gas bubbles inside the weld indicates porosity; as gases reach the weld pool, bubbles form. Once the weld pool has cooled, these bubbles cannot be properly eliminated since they are irreversible. Porosity is more than just an aesthetic concern.
A welded joint may collapse as a result of excessive porosity, which weakens the weld. Porosity is something that local fabrication companies and construction codes need to treat seriously. The hollow cavities compromise the weld bead's strength. The good news is that a variety of easy preventative methods exist to protect against the onset of excessive porosity.
Keeping things clean is the first step in preventing excessive porosity. Contamination, either from the air around the weld site or the surface of the base metal, is a major contributor to porosity. Controlling the airflow in your shop or project area is the first step towards preventing porosity.
When choosing a location for your welding equipment, keep ventilation in mind. While ventilation is undoubtedly necessary to remove welding fumes, an uncontrolled flow of air bubbles is not what you need.
Before beginning the welding process, the base metal must be thoroughly cleaned. Excessive porosity and metal cracking can be caused by impurities in the base metal. Impurities in base metals can include:
- Dirt
- Debris
- Dust
- Grease
- Rust
An angle grinder and a stiff brush are required to clean the base weld. It is necessary to remove the galvanising layer from a galvanised steel piece using an angle grinder to avoid problems that could come from the weld having too many holes in it.
Burn-Through
Burn-through is the result of the filler material or weld metal entirely passing through the weld metal. This flaw is especially dangerous when welding materials that are thinner than ⅛ inch or around 12 gauge. Avoid burn-through by adjusting weld temperatures.
When welding from a vertical angle, it's best to begin at the top of the weld spot and work your way down. This technique works exceptionally well for welding thin materials with a GMAW (MIG) welder.
You can also help stop burn-through by lowering both the power and the speed of the wire feed. Too much heat exposure to the weld site is likely to occur if the voltage and wire feed speed are set too high.
Incomplete Fusion
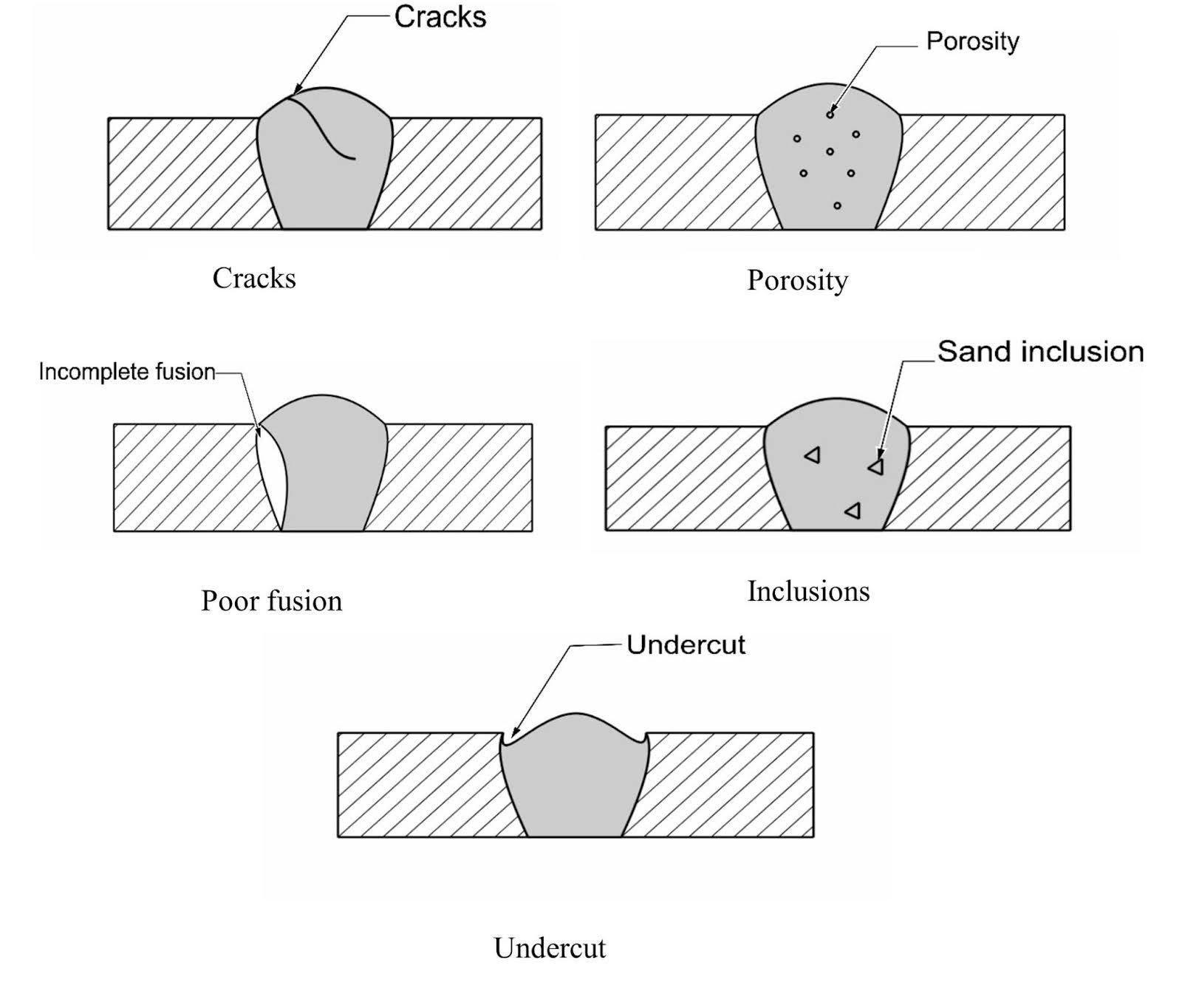
In welding, fusion is the process of combining two or more separate metal components into a single, continuous piece. To put it another way, this is the overall goal of the welding process. Two distinct deficiencies may cause incompletion of fusion.
The following are some ways that incomplete fusion can show up:
- Interpass Cold Pass
- Lack of sidewall fusion
A few stages must be carried out to ensure that the fusion of two or more pieces of metal is complete. After welding, you should always clean up the slag. Incomplete fusion and other structural discontinuities can be caused by leaving slag behind.
As with many of the other defects mentioned here, incomplete fusion is usually caused by bad technique. In addition, improper travel speed and welding angle will make it difficult to fully fuse different pieces of metal together. Lastly, it is also crucial that you choose the appropriate welding method for the intended use.
Poor Joint Penetration
Poor joint penetration or the absence of joint penetration is another common defect that is easily avoidable. This problem happens when the welding rod's arc can't go deep enough to make a thick enough weld. When this happens, the weld will fail and fall apart, often right away.
Like many welding flaws, this one is frequently the consequence of using the incorrect welding equipment. Additionally, using the wrong methods is also commonly the cause of poor joint penetration.
Spatter
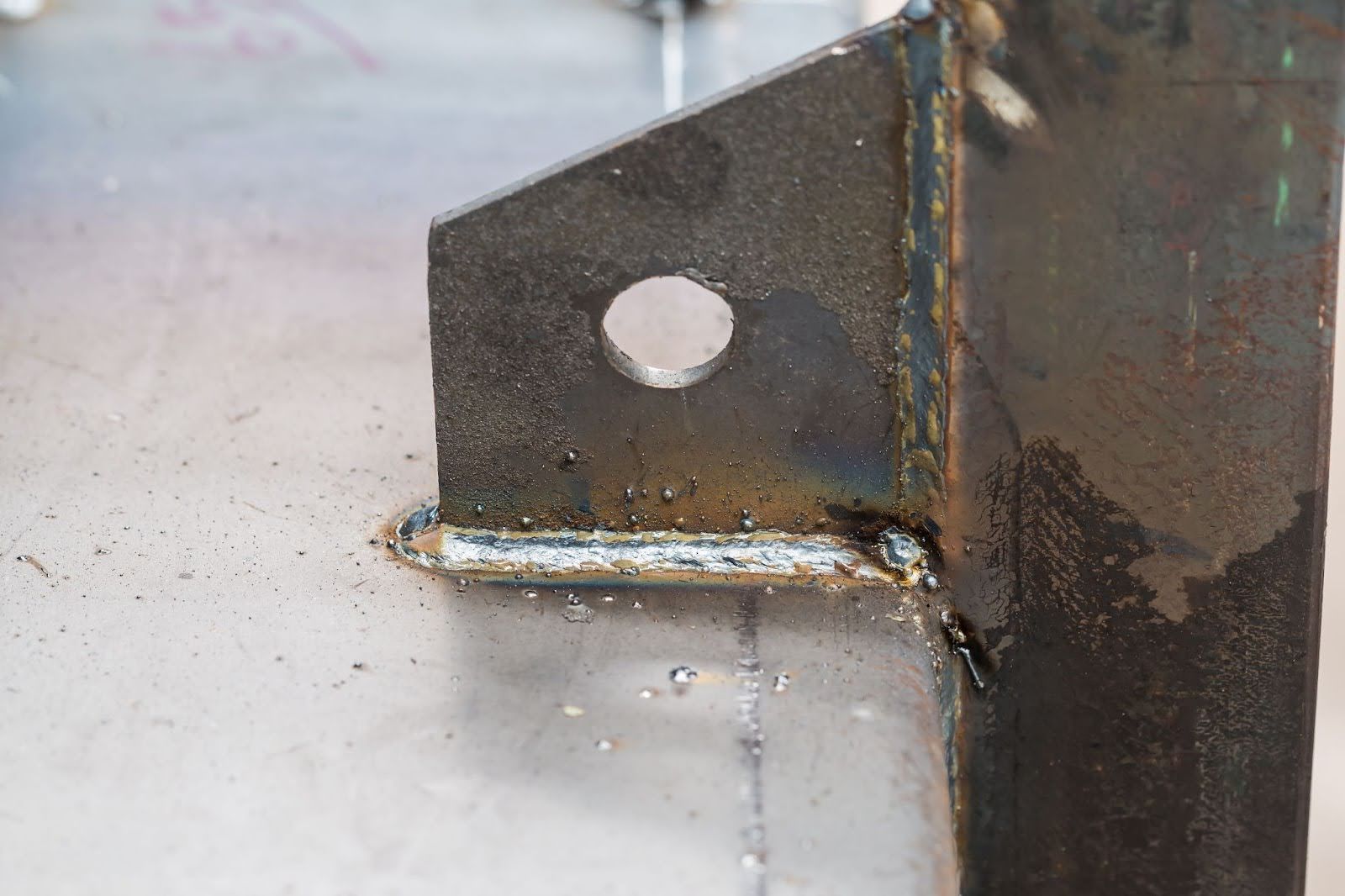
Spatter is described as welding metal droplets that come out of the molten pool of metal. These droplets then cool and solidify along the sides of the weld bead. Spatter is mostly an aesthetic defect. However, excessive spatter might cause other issues since the workpiece's integrity may be compromised during the intense cleaning process to get rid of the spatter.
Excessive spatter can arise from a number of factors, such as:
- Wire feed speed
- Excessive voltage
- Improper polarity selection
The first step in preventing excessive spatter in GMAW welding is choosing the suitable shielding gas for the job.
Ensure The Success Of Your Welding Project By Having A Proper Understanding Of The Process
By learning the causes of common welding defects and taking preventative measures, welders are able to produce stronger, more dependable joints. Every stage of the welding process, from the careful management of heat to the careful preparation of materials, contributes to the creation of flawless connections.
Looking for metal welding services in Malaysia? Visit Choong Ngai Engineering now!
If you're looking for a reliable quality welding services provider in Malaysia, look no further than Choong Ngai Engineering Works. We are a leading provider of quality welding services Malaysia and provide the best possible service to our clients. Contact us now!