Basics Of The Metal Forming (Shaping) Process
Metal forming is a fabrication process that creates structural parts and components out of metal sheets or tubing.
The basics of the metal shaping process will bend or deform a metal workpiece to a desired geometric shape. In many ways, metal forming is not only the foundation of modern industrial manufacturing but a vital industry of and in itself.
This guides look at the main sheet metal fabrication processes and explains how they work and what they are used for.
What Are The Most Common Types of Metal Forming Techniques?
In manufacturing industries, there are different types of metal forming processes utilized for mass production. Some of the more common processes are bending, stretching, deep drawing, and roll forming.
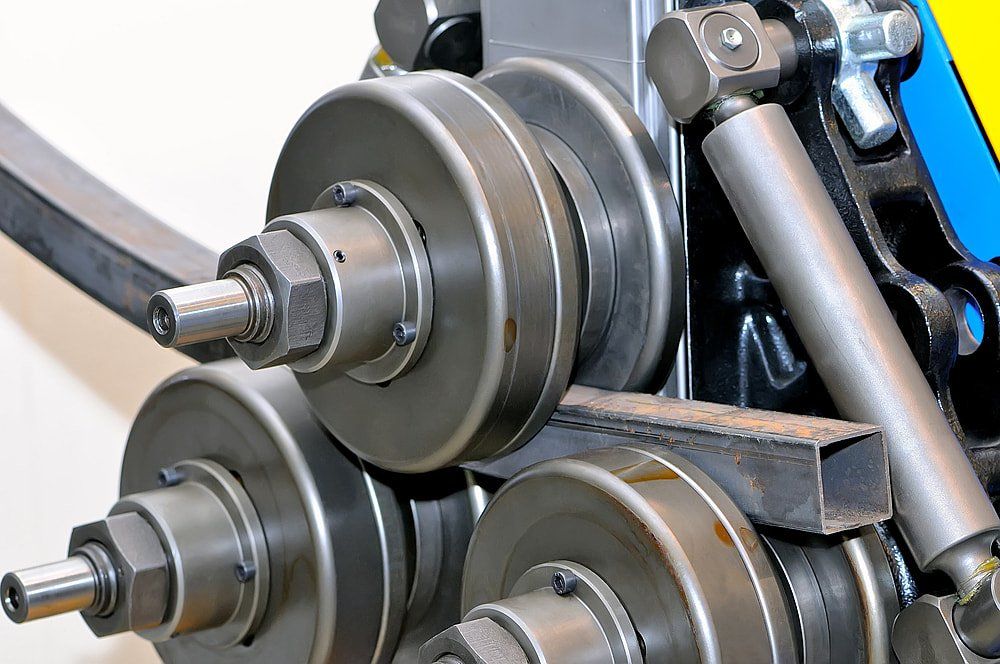
Roll forming involves the continuous bending of a long strip of sheet metal (typically coiled steel) into a desired cross-section.
The strip passed through sets of rolls mounted on consecutive stands, each set performing only an incremental part of the bend, until the desired cross-section, or profile, is obtained.
Roll forming is ideal for producing open profiles or welded tubes with long lengths or in large quantities.
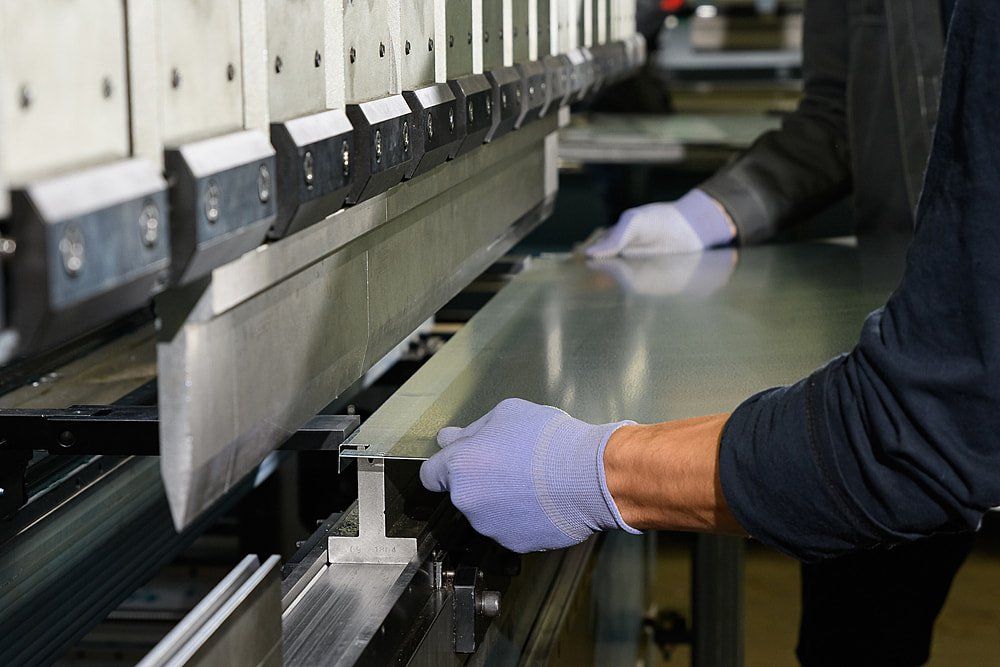
Press brake forming is used for forming long, thin sheet metal parts.
During the process, a piece of sheet metal is formed along a straight axis with the use of a V-, U-, or channel-shaped punch-and-die set.
Despite the simplicity of the process, it can be difficult to maintain accuracy with factors like the press, tooling, and workpiece material influencing the outcome.
Air bending is the most common press braking process and relies upon three-point bending. In this case, the die has a sharper angle than the required bend (typically 85 degrees for a 90-degreebend) and the upper tool is precision-controlled while it pushes the metal down to form the required bend.
Extrusion forming is done when objects with fixed cross-sectional profiles are created with the process of extrusion by pushing metals through a die of the desired cross-section.
This is beneficial for creating very complex cross-sections because the material is only exposed to compressive and shear stresses.
One key advantage is the excellent surface finish. Another is the increased strength of metal objects produced with extrusion.
Two types of extrusion exist — continuous or semi-continuous. Continuous extrusion involves the production of an indefinitely long material; semi-continuous involves the production of many pieces.
The material can be either hot or cold. Extrudate is the term for objects produced with extrusion.
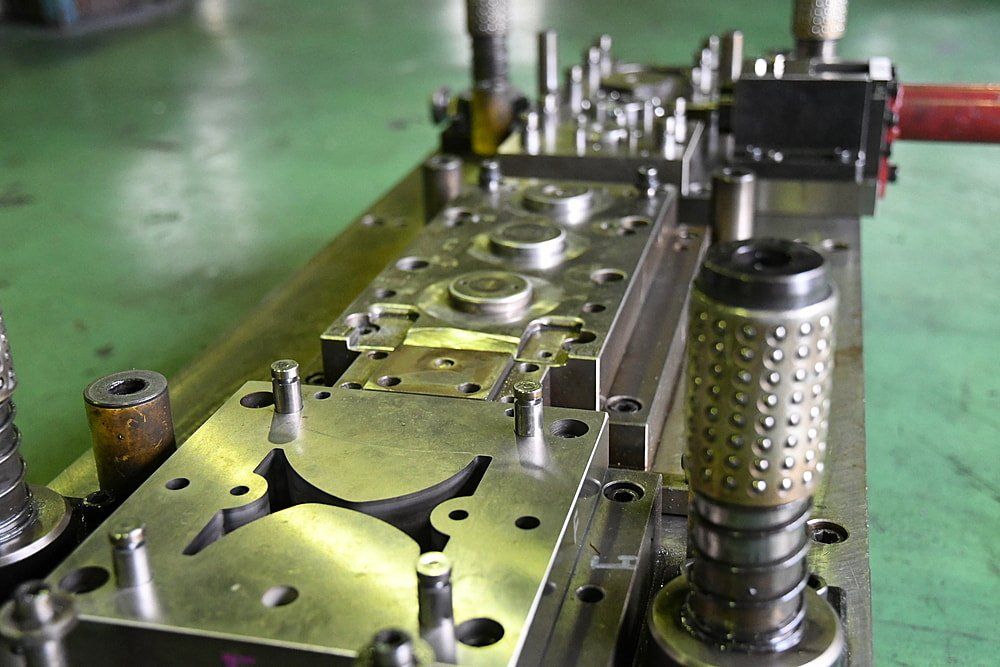
Stamping, also known as pressing, entails using a stamping press to form a net shape from either blank or coil form flat sheet metal with the use of a tool and die surface.
Similar to the processes used to form sheet metal, stamping also encompasses punching (with a machine or stamping press), blanking, embossing, bending, flanging, and coining.
It is possible to carry out a stamping process in either a single operation or by a series of stages.
Forging is a manufacturing process that forms metal with the use of compressive forces and a hammer, most often a power hammer, or die.
The hammer is used to deliver what is known as a “blow” and the forging process is classified according to temperature such as cold, warm, or hot forging.
When working at increased temperatures, a metal is heated, usually in a forge.
Temperature plays a crucial role in forging even if the above processes can be performed at various temperatures. They are classified either as above or below the recrystallization temperature and in one of three categories: hot, warm, or cold.
Hot forging is faster and more precise, while cold forging usually results in work hardening of the piece.
Choose a workshop with metal shaping services you can trust
We hope you've discovered all about the basics of metal shaping process. You expect a lot out of your custom metal requirements. That's why we work closely with skilled technicians to create custom designed, precision-manufactured custom metal for your business.
Most importantly, we'll work alongside you and your team to understand and define your exact requirements, and this process ensures that we provide the best solution to your unique requirements.
Why not give Choong Ngai Engineering a try? Learn more about our metal shaping services and previous projects at www.choonngaiengineering.com