What Are The Principles Of Metal Rolling Processes?
Did you know that the metal rolling process is the most important and widely used metal forming process because of its lower cost and higher productivity?
In fact, over the last decade, growth in the metal fabrication industry is moving away from the traditional manufacturing process like casting and forging in favour of metal rolling!
That's because fabricating sheet metal reduces cost and offers high design flexibility. Metal rolling is a very common process used in the fabrication industry for sheet metal.
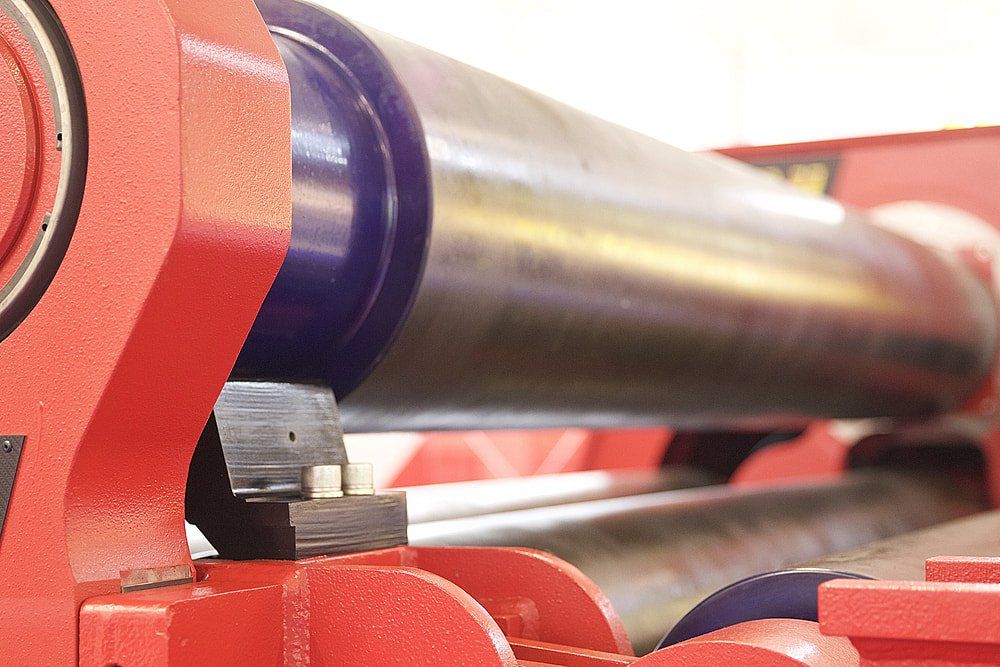
What Exactly Is Metal Rolling In Metal Fabrication?
Rolling in metalworking is a metal forming process that helps to reduce the thickness of metal and make the thickness uniform.
The metal stock is passed through one or more pairs of rolls to reduce the material.
Rolling is classified according to the temperature of the metal rolled. If it is hot rolling, the temperature of the metal is above its recrystallization temperature.
Otherwise, if the temperature of the metal is below the recrystallization temperature, it is known as cold rolling.
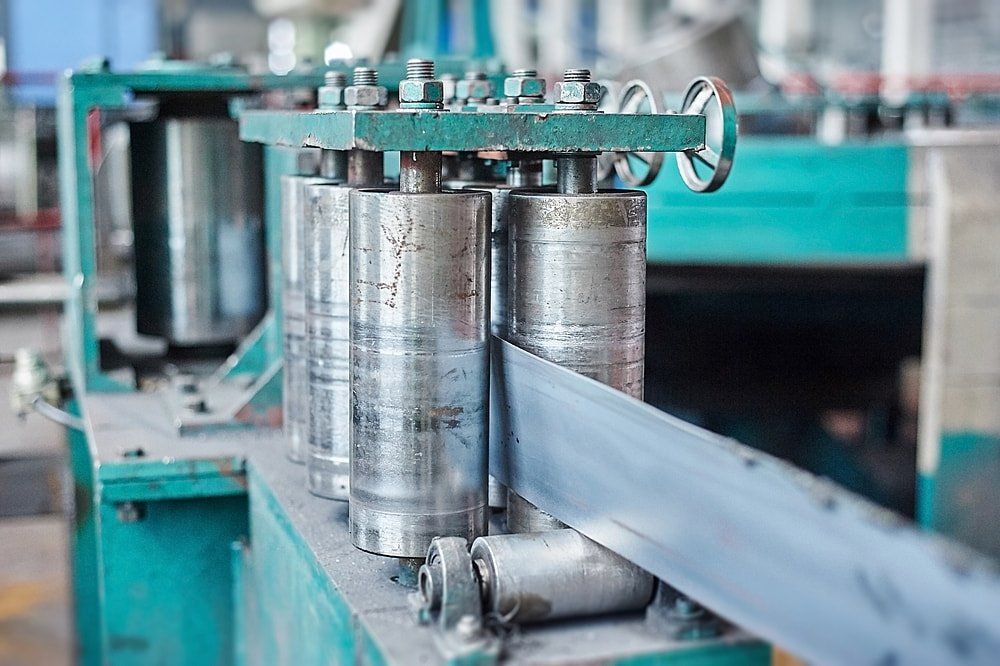
Flat Rolling
This is the most basic form of rolling in which the starting and end material both have a rectangular cross-section.
The material is fed in between two rollers, that rotate in opposite directions. The two rollers in flat rolling are called working rolls. The gap between the two rolls is less than the thickness of the starting material, which causes the deformity of it.
The material, which is pushed through due to the friction at the interface between the material and the rolls, even elongates due to the decrease in material thickness.
However, the friction between the rolls limits the amount of deformation possible in a single pass. The rolls just slip over the material and do not draw it in if the change in thickness is too great.
Thread/Gear Rolling
Thread or gear rolling is a cold-forming type of rolling process used to cut gear or threads on a cylindrical blank.
In this process, the threaded dies are fitted on cylindrical rollers of the rolling machine. The cylindrical blank presses the threaded roller and roll against the faces, which displace the material and form threads on the cylindrical blank.
The thread-rolling process has the benefit of generating threads with high strength (due to cold working), without any material loss (scrap) and good surface finish. It is often used for the production of screws, bolts, etc. in mass quantities.
Shape Rolling/Structural Shape Rolling/Profile Rolling
The shape rolling is used to cut different shapes on the metal workpiece. It does not involve any significant change in thickness.
It’s a special type of cold rolling that is suitable for producing molded sections such as irregular shaped channels and trim. It's used to roll construction shapes such as I-beams, L-beams, and U channels, rails for railroad tracks, and round and square bars and rods, etc.
The applications of shape rolling are -
- Construction materials
- Ceiling panel
- Metal furniture
- Household appliances
- Partition beam
- Steel pipe
- Automotive parts
- Roofing panels
- Door and window frames and other metal products
Ring Rolling
Ring rolling is a type of hot rolling that increases the diameter of a ring. Two rollers i.e. main and idler are arranged and rotated in the same direction to each other in this process.
Due to the rotation of the roller, the ring rotates and the rollers then start moving close to each other, with a decrease in ring thickness and hence this results in an increase in its diameter.
To maintain the height of the ring, a pair of edge rollers are used, which do not allow metal to flow in the direction of height.
This process gives material finish and high accuracy. Common applications of ring rolling include -
- Large bearings
- Turbines
- Air planes
- Railway tyres
- Gears
- Rockets
- Pipes
- Pressure vessels
Choose a workshop with metal rolling services you can trust
We hope you've discovered all about the principle of metal rolling processes. You expect a lot out of your custom metal requirements. That's why we work closely with skilled technicians to create custom designed, precision-manufactured custom metal for your business.
Most importantly, we'll work alongside you and your team to understand and define your exact requirements, and this process ensures that we provide the best solution to your unique requirements.
Why not give Choong Ngai Engineering a try? Learn more about our metal rolling services and previous projects at www.choonngaiengineering.com