Exploring 6 Techniques To Cut Sheet Metal: What To Know
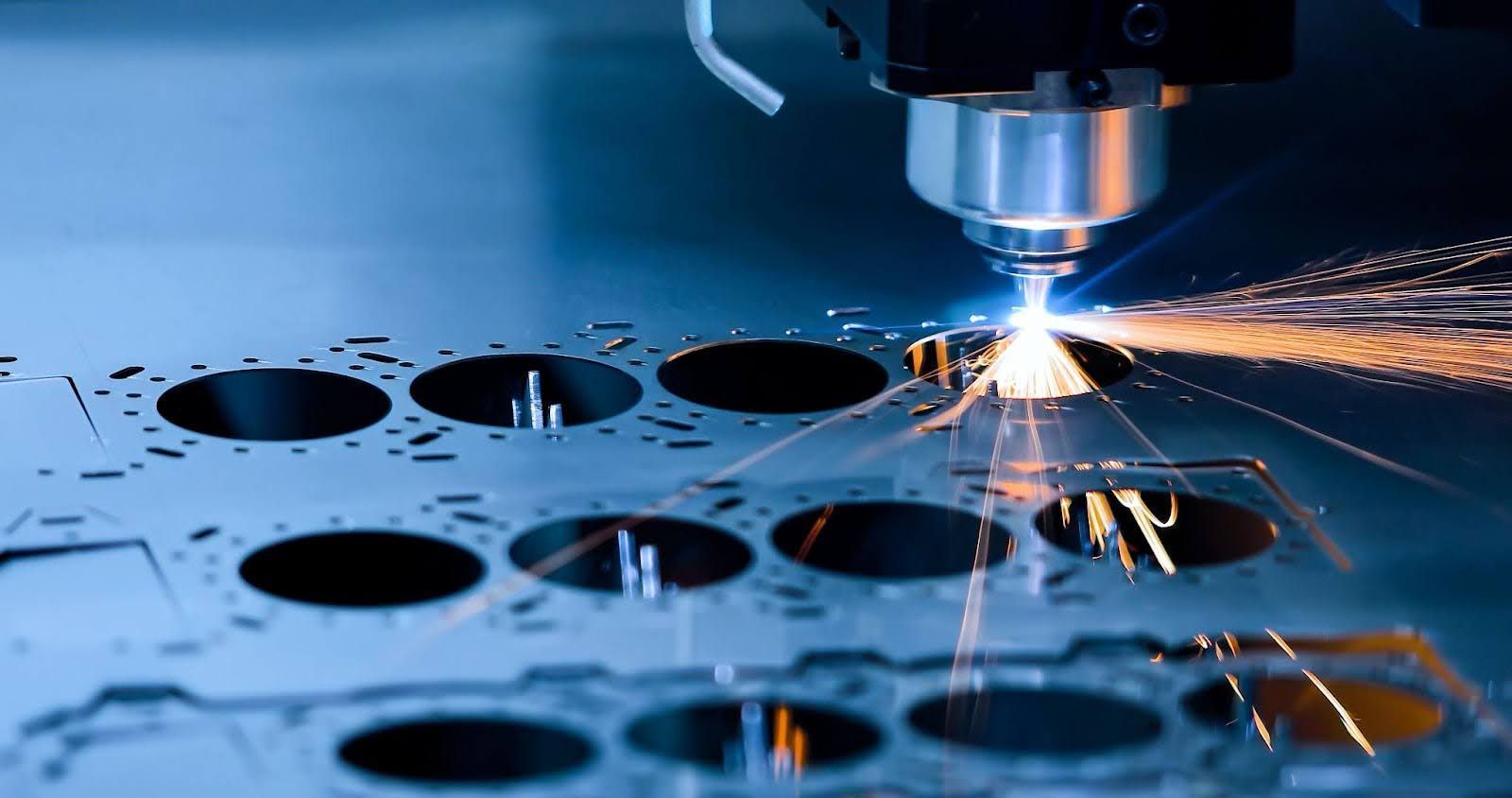
For many commercial and artistic endeavours, sheet metal serves as a versatile canvas. Unlocking its full potential requires learning the art of cutting. In this post, we'll examine a variety of cutting techniques, each of which has a unique set of benefits for different purposes.
These techniques can be helpful for anyone looking to improve the accuracy and adaptability of their work, from beginners to experts. So, if you want to improve your sheet metal fabrication skills, keep reading as we delve deeper into these techniques.
What Is Sheet Metal Cutting?
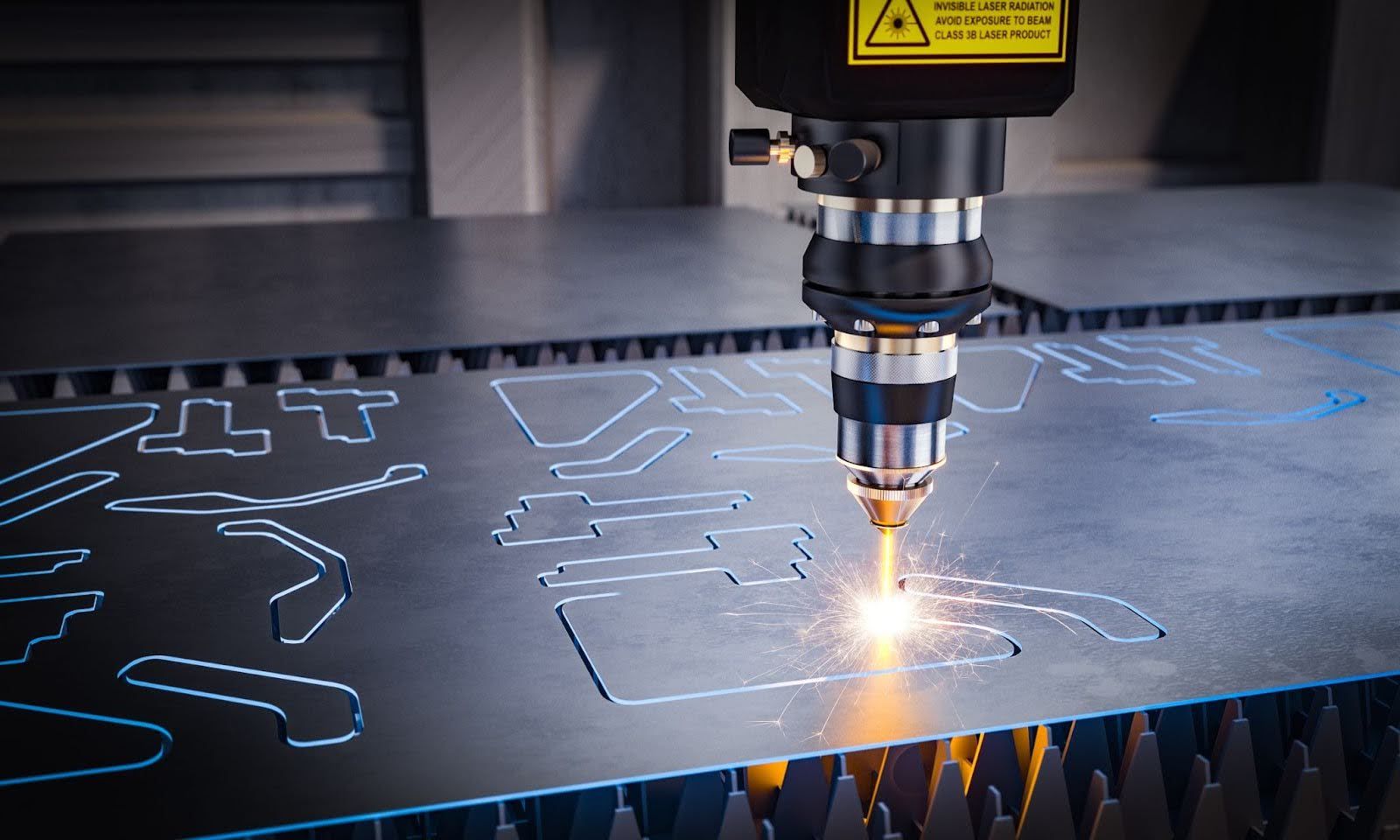
Sheet metal cutting refers to a wide range of sheet metal fabrication processes. The primary goal of sheet metal cutting is to remove sheet metal material by applying sharp, high-force cutting edges to the sheet metal in question.
For shearing processes, the material is cut with high-pressured blades called shears or dies. When the strength of a sheet of metal is less than the force of the applied shear stress, the cut is created.
In general, each piece of sheet metal is put between two different parts of the cutting process. The upper part is known as a punch, while the lower part is known as a die. Technically, each of these components can be referred to as a die, but to distinguish one from the other, the upper part is given a separate name.
The Various Ways To Cut Sheet Metal
The craft of sheet metal cutting involves a wide range of methods, each optimised for a specific set of conditions. Here, we'll explore the various techniques used to cut sheet metal.
Punching
Punching is a straightforward method of removing just a small amount of material from a sheet metal product. When a piece of sheet metal is punched, a slug is produced and, in most situations, thrown away as scrap.
When cutting sheet metal, punching can be done in many different ways. Typically, the type of punching procedure you need depends on the shape of the component that has been punched out and where it is placed.
The main types of punching techniques include the following:
- Piercing
- Lancing
- Notching
- Slotting
- Nibbling
- Perforating
Blanking
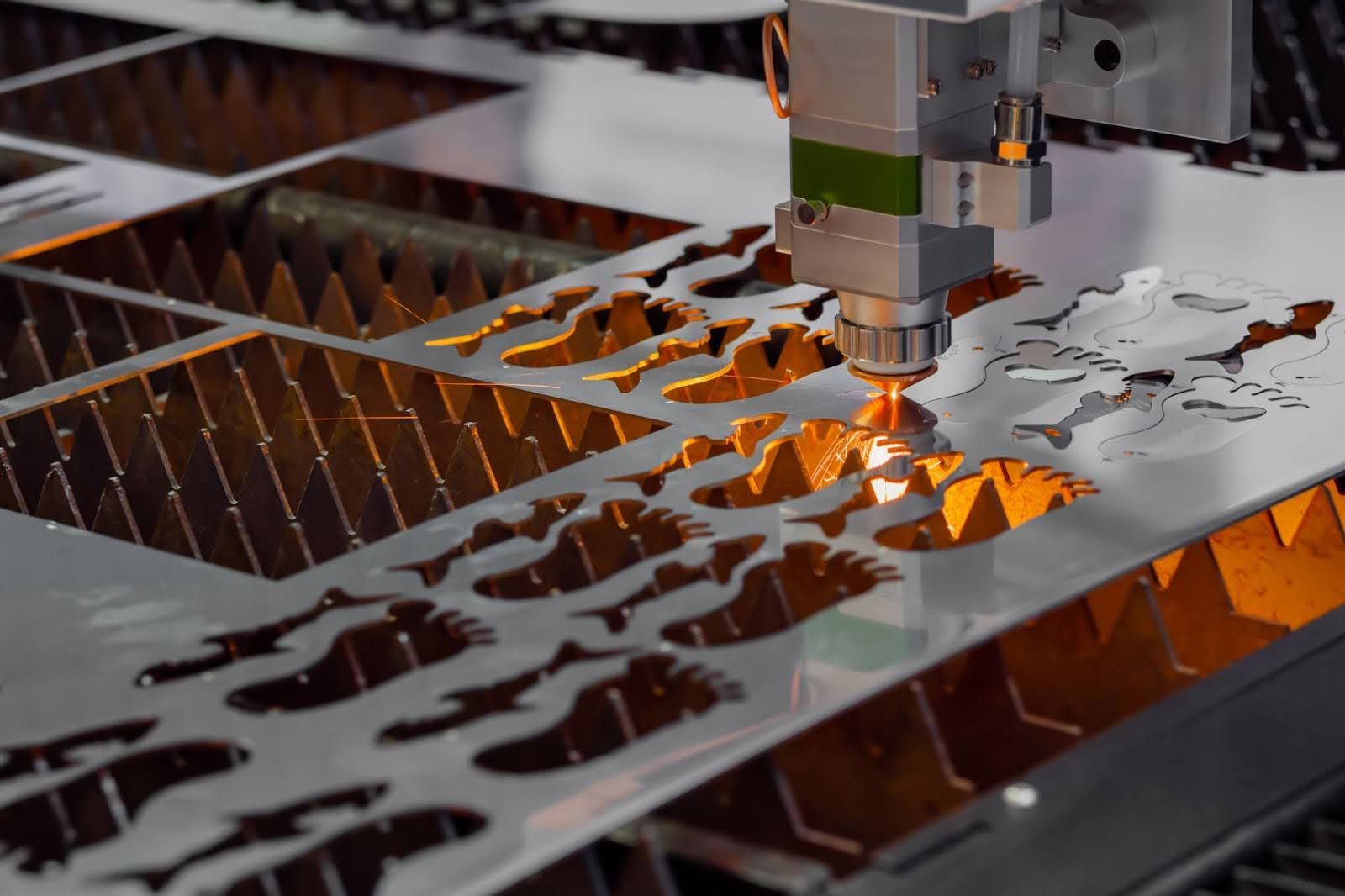
Blanking is a method of making intricate cuts in sheet metal by applying a tremendous shear force to a contained section. The punch, which is what applies the pressure, is meant to be the shape of the detail that is needed. This process creates the sheet metal part that separates from the metal piece as a whole.
One sheet of sheet metal can only be used to make so many identical copies of a finished product; hence, the entire piece that is left over is regarded as scrap, while the blanks are the actual finished product.
Shearing
When comparing shearing to blanking, there are certain similarities. Shearing can cut a piece of sheet metal in a straight line or at an angle. It's also often used to break up bigger pieces of metal into smaller ones that can be used further down the production line.
The primary distinction lies in the size and precision of operations. While blanking is mainly used for small details, shearing is a critical "preparation" step in many industrial processes. To accomplish it, just put a piece of sheet metal between two "blades" of the machine and push the upper blade, which is called the punch, downwards to cut off that portion of the material.
Slitting
In contrast, slitting is the process of cutting a piece of sheet metal with two circular blades that oppose each other. Slitting, in general, is similar to using a standard can opener because it can produce both straight and curved lines. The majority of the straight lines are cut with idle cutters, while manually operated metal cutters are used for curved slitting.
In order to produce sheet metal pieces of a certain width so that other machines can properly cut them, slitting is a crucial step in the total sheet metal fabrication procedure. Since sheet metal usually comes to the factory in coils, slitting is often the first step in the cutting process before something more special can be done.
Trimming
Trimming is a basic but crucial operation to remove excess material from the workpiece's edges. This is typically the last step in the fabrication process that utilises sheet metal working machinery.
Deburring
Like trimming, deburring removes extra material from a piece once it has been completed or is nearing completion. The difference between the two processes is that trimming is carried out by machinery, whilst deburring makes use of a smaller hand-sized tool to, as the term implies, remove the last of the burr on the workpiece to smooth off the edges and get rid of any splinters or rough edges.
Sheet Metal Fabrication Is An Adaptable Process That Includes Various Techniques
There are numerous techniques that exist in the broad and ever-evolving field of sheet metal cutting to meet any requirement or application. Whether you are creating a delicate work of art or a piece of heavy-duty equipment, the appropriate cutting method can make a huge impact.
Looking for a quality sheet metal fabricator in Malaysia? Choose Choong Ngai Engineering!
So, if you're looking for sheet metal fabrication in Malaysia, visit us at Choong Ngai Engineering today to speak to our experts. We at Choong Ngai Engineering have years of experience and knowledge to answer your doubts or concerns, and we ensure to provide you with the quality solution you're looking for. Call us now!