How to Choose the Right Metal Coating for Your Project
How to Choose the Right Metal Coating for Your Project
When it comes to metal fabrication, selecting the right metal coating may be the last thing on your mind. You may think, “It’s just choosing a colour or texture, right?” But, in truth, it’s more complex than that. If this decision is left until the final stage, you risk additional delays, unexpected costs, and a final product that may not meet your performance standards.
Below, we’ll explore the key factors that go into choosing a suitable metal coating, from material compatibility to cost and beyond, so you can make a well-informed choice for your next project.
Consider Material Compatibility
The first step in choosing a metal coating is to look at how well it pairs with your base metal. Different substrates, like steel, aluminium, or copper, may require specialised coatings or surface treatments.
- Surface Interactions: Certain metals develop oxide layers that can hinder coating adhesion if not treated properly.
- Galvanic Corrosion: If your design involves multiple types of metal in contact with each other, a coating that prevents galvanic corrosion is crucial.
Prep Work: Many coatings, especially powder coatings, perform best when the surface is thoroughly cleaned, etched, or primed. A quick wipe-down won’t cut it if you want to avoid peeling or blistering later on.
Understand Different Types of Metal Coatings
There are so many different metal coating options out there that it’s easy to feel overwhelmed. To help you cut through the confusion, here’s a quick look at some go-to coatings, including their benefits and drawbacks.
Coating Type | Benefits | Drawbacks |
---|---|---|
Powder Coating | • Highly durable, chip-resistant finish. • Wide colour range and textures. • Low VOC emissions which makes it eco-friendlier than many paints. | • Requires curing in a powder coating oven (part must fit and withstand the process) • Setup costs can be higher for small batches. |
Galvanising | • Excellent corrosion protection • Cost-effective for large-scale steel projects | • Dull, rough industrial appearance. |
Paint Coating | • You can choose from multiple application methods such as spraying, brushing, and dipping. • Broad colour selection • Lower initial equipment investment | • May require multiple coats or primers for the best adhesion. • Can chip or fade over time if not maintained. |
Electroplating | • Offers decorative and reflective finishes (e.g., chrome, nickel) • Can provide conductive properties if you opt for copper plating | • Chemical baths require strict environmental controls. • Thinner coatings, which may be worn under heavy loads. |
Thermal Spraying | • Excellent for high-temperature or abrasive environments • Can apply metal, ceramic, or carbide materials • Creates a strong bond and thick protective layer | • Requires specialised equipment and skilled operators • Pre-treatment is critical for proper adhesion • Can leave a rougher surface compared to other finishes |
Environmental Conditions
Environmental conditions play a huge role in determining which metal coating is right for your project. This depends not only on what you’re coating but also on where it’ll be placed.
In a tropical climate like Singapore, high humidity can lead to a high risk of corrosion, so you might lean toward more heavy-duty coatings like galvanising or specialised paints formulated to withstand moisture.
However, if your metal parts are destined for an air-conditioned environment—such as an office, retail store, or data centre—there’s typically less stress from heat and humidity, allowing you to choose a slightly less robust (and often more budget-friendly) coating.
Performance Requirements
Constant maintenance and breakdowns can be an absolute headache—especially if you’re running industrial equipment or dealing with high-wear parts. Some common considerations include:
- Abrasion Resistance: If parts come into frequent contact with other surfaces, choose a coating that can handle ongoing friction.
- Temperature Tolerance: High-heat or sub-zero environments call for a finish that won’t crack or degrade under extreme conditions.
Chemical Exposure:
Harsh chemicals, solvents, or cleaners demand coatings formulated to resist corrosive damage.
Aesthetic Considerations
The biggest myth about metal coating is that it’s all about appearances. Sure, a bright pop of colour or a sleek finish can set your project apart, but looks aren’t everything. Coatings do so much more than make your piece look good—they protect against corrosion, wear, and other damage.
That said, aesthetics still matter, especially if your product will be on display, used by customers, or representing your brand. Talk with a metal fabricator like us at Choong Ngai Engineering, who can help you choose an option that meets both your performance requirements and design goals.
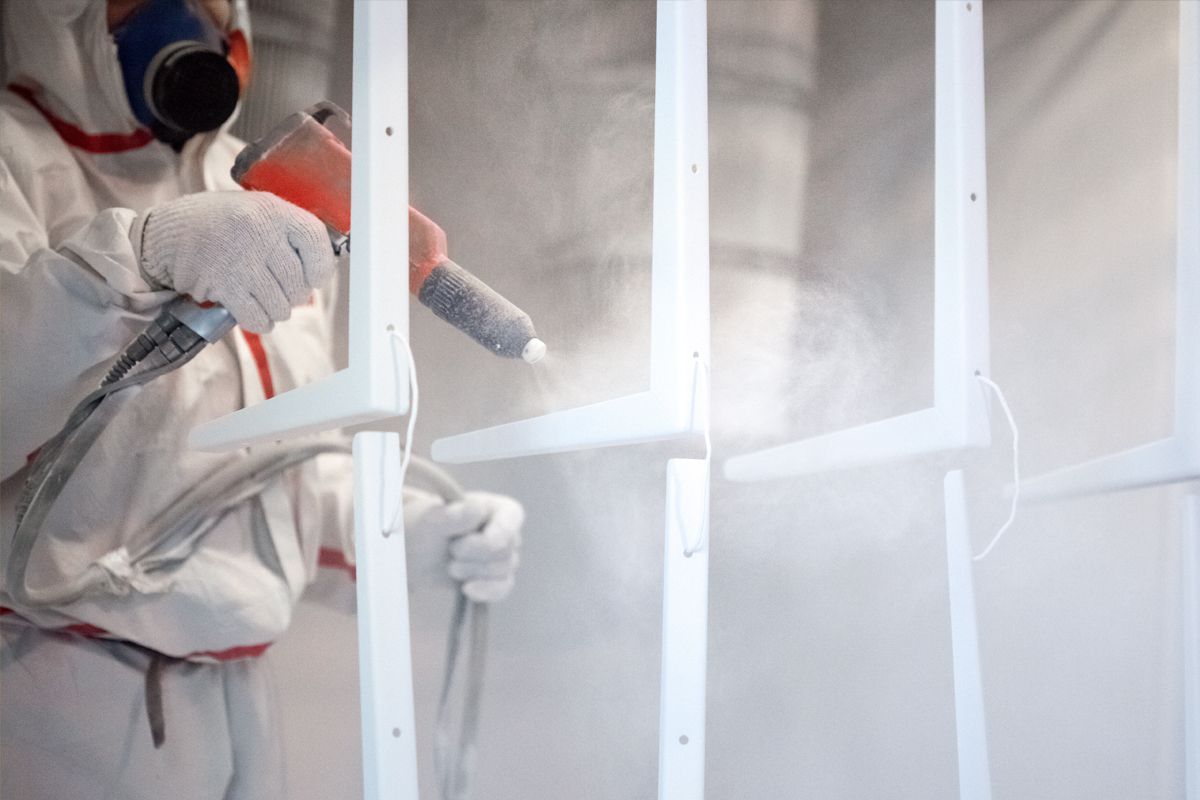
Application Methods
You might be thinking, “Why should I even care how my metal coating is applied? Isn’t that just the metal fabricator’s job?” Application methods can directly affect quality, overall cost, and lead times.
Here’s how some common methods work:
- Powder Coating: An electrostatic process where powder particles are sprayed onto the metal surface and then baked at high temperatures to cure and form a solid, uniform coating.
- Galvanising: The steel is dipped into a bath of molten zinc, which creates a protective metallurgical bond between the zinc and steel.
- Liquid Painting: Liquid paint is applied to the metal in multiple layers and allowed to dry or bake, with surface preparation being an important step for a lasting finish.
- Electroplating: Parts are submerged in a specially formulated electrolytic solution; an electrical current deposits a thin layer of metal onto the substrate for protection or aesthetics.
- Thermal Spraying: A material, often metal, ceramic, or carbide, is heated and sprayed onto the substrate, building a protective layer that can withstand extreme temperatures or heavy wear.
Cost and Budget
Budget is always one of the most asked-about aspects of any metal coating project. Yet providing a precise quote can be tricky because no two projects are alike.
Still, there are a few common considerations that typically influence the final price tag:
- Type of Coating: Specialised coatings, such as thermal sprays or high-grade powder formulations, often carry a higher material cost. At the same time, these coatings might offer additional benefits, like improved heat or wear resistance, that justify the investment.
- Size And Complexity Of Parts: Large or intricate parts usually require more prep, masking, or multiple passes during application. Deep recesses and tight corners take extra care, while oversized items may need special equipment or handling.
- Preparation Costs:
Coatings don’t adhere well to dirty, greasy, or oxidized surfaces. A thorough cleaning, possibly involving sandblasting or chemical treatments, can add to both time and labour costs.
Looking for metal spray coating services in Malaysia? Choose Choong Ngai Engineering!
Ready to get started?
Choong Ngai Engineering will guide you from initial consultation to final
metal coating application, helping you avoid the headaches of re-coating and ensuring your metal components stand up to both environmental and performance challenges.
Contact us to discuss your project details.