Stainless Steel Fabrication: Top Industrial Application Methods
Stainless Steel Fabrication: Top Industrial Application Methods
Stainless steel appears in all sorts of everyday items—from the reusable water bottles many of us carry, to sleek kitchen appliances. It’s also a vital component across numerous industries, thanks to its durability, corrosion resistance, and versatile properties.
Below, we explore the industrial methods used in stainless steel fabrication, highlighting cutting-edge techniques, forming processes, and finishing options that help maintain the metal’s integrity and appearance.
Welding Techniques
If you’re working on a stainless steel project, welding is likely to play a major role in its construction. While many of us picture a welder in a protective helmet, torch in hand, and bright sparks flying, there are three primary welding methods commonly used for stainless steel.
Let’s take a closer look at each:
TIG Welding
If you’re working on a stainless steel project, welding is likely to play a major role in its construction. While many of us picture a welder in a protective helmet, torch in hand, and bright sparks flying, there are three primary welding methods commonly used for stainless steel.
MIG Welding
MIG (Metal Inert Gas) welding uses a continuous spool of wire that automatically feeds into the weld area, serving as both the electrode and filler material. Because MIG also relies on shielding gas, it’s sometimes confused with TIG (Tungsten Inert Gas) welding. However, the main difference is that TIG employs a non-consumable tungsten electrode and a separate, hand-held filler rod, while MIG’s wire electrode is consumed during the welding process. The efficiency of MIG welding often makes it the go-to choice for large-scale jobs or thicker stainless steel sections.
Spot Welding
Also referred to as resistance spot welding, this method uses two electrodes to deliver a high electric current through the overlapping edges of thin stainless steel sheets. This current produces localised heat, fusing the sheets at those precise points. Spot welding is especially popular for large-scale production runs where efficiency is crucial.
Cutting Processes
Stainless steel fabrication is a step-by-step process that begins with cutting. Achieving accurate cuts sets the stage for the rest of the workflow, ensuring each subsequent step can be carried out efficiently. Depending on factors like thickness, design complexity, and end-use, different cutting methods may be employed.
Here are the most common techniques.
Laser Cutting
This technique uses a high-powered laser to achieve precise cuts in stainless steel. It’s often chosen for its ability to produce clean, accurate edges that require little to no additional finishing, making it ideal for complex shapes or designs with tight tolerances.
Plasma Cutting
Plasma cutting uses a stream of electrically charged gas (plasma) to slice through stainless steel quickly. It’s well-suited for thicker plates and offers a good balance of speed and efficiency, though it typically produces a larger heat-affected zone compared to laser cutting.
Waterjet Cutting
The main difference between waterjet cutting and the previously mentioned methods is that waterjet cutting is a cold process. Because it uses a pressurised jet of water, often mixed with an abrasive, it generates no heat, preserving the structural properties of stainless steel and reducing the risk of warping.
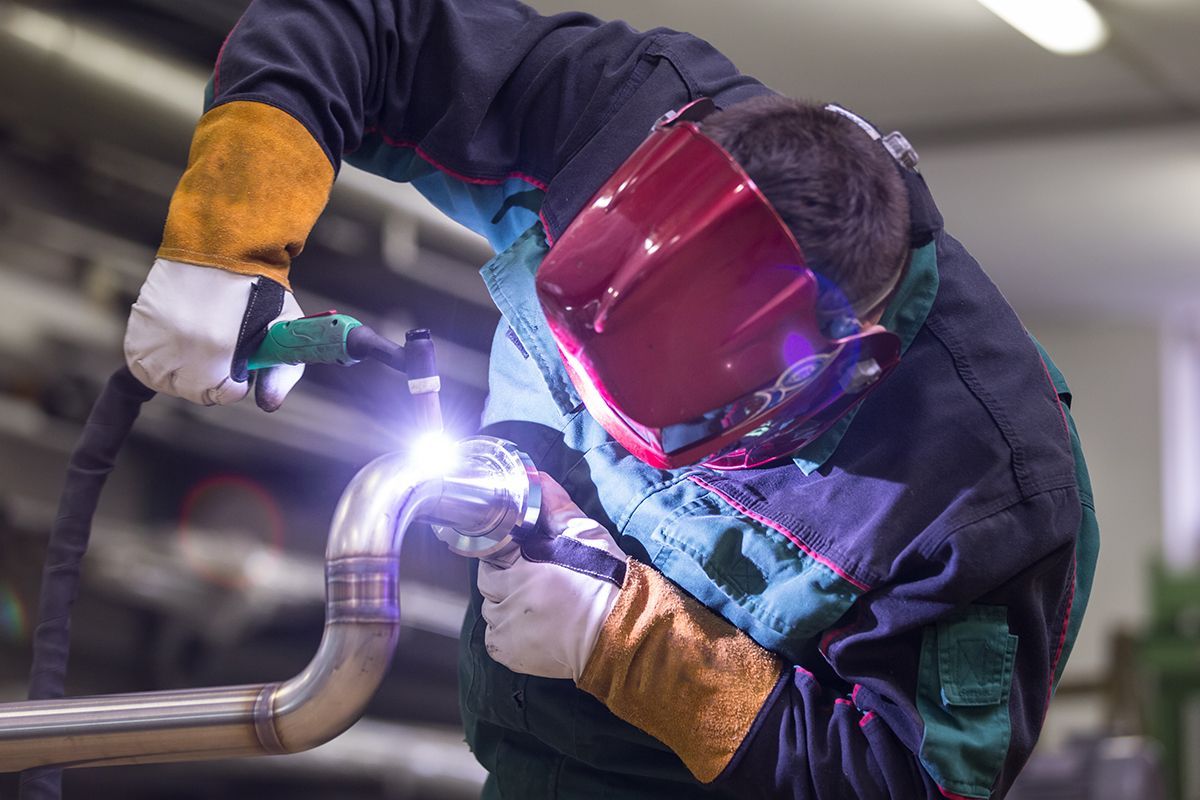
Environmental Conditions
Forming transforms flat or raw stainless steel into the shapes required for final assembly, The choice of method depends on several factors, thickness, complexity, and overall design requirements. Below, we highlight three widely used forming techniques in stainless steel fabrication.
Rolling
Rolling involves passing stainless steel through a series of rollers to change its shape. For instance, a plate can be rolled into a cylindrical or conical form for applications like storage tanks and pressure vessels. Rolling is favoured for large-scale industrial projects, where uniform curvature and precise dimensions are essential for structural integrity.
Press Braking
Press braking is used to bend stainless steel sheets or plates into specific angles or forms. A punch and die set apply force on the metal, creating accurate bends. This method is efficient for producing items like brackets, enclosures, and frames. Modern press brake machines often feature CNC (Computer Numerical Control) technology, enabling consistent, repeatable results.
Hydraulic Press Forming
Hydraulic press forming uses hydraulic cylinders to deliver controlled force onto a workpiece. This process is ideal for forming stainless steel components that require multiple bends or complex shapes, as the hydraulic press can apply steady, precise pressure across the metal surface. Consistent forming results are crucial in projects such as automotive body parts or custom-engineered assemblies.
Finishing Options
This is the final step of stainless steel fabrication where everything comes together. At this point, the goal is to enhance the metal’s appearance, corrosion resistance, and overall quality.
Polishing
From the name, you can probably guess what this process is all about. Polishing removes minor imperfections to refine the surface finish and can achieve anything from a subtle satin appearance to a highly reflective mirror polish. If aesthetics play a key role in your project, polishing is a great way to make your stainless steel components stand out.
Electroplating
If you’re looking for a balance between durability and aesthetics, electroplating could be the perfect fit. This process coats the stainless steel surface with a thin layer of metal such as nickel or chromium to boost corrosion resistance and overall strength.
Grinding
Grinding removes excess material, like burrs and leftover weld metal, using abrasives to level out any uneven spots. By doing so, it effectively eliminates surface irregularities such as scratches and oxidation, resulting in a cleaner, smoother finish. This step can stand on its own or serve as a foundation for additional finishing methods, making it a versatile choice in many stainless steel fabrication workflows.
Looking for a quality stainless steel fabricator in Malaysia? Choose Choong Ngai Engineering!
If you need a partner who delivers precision results along with attentive support,
Choong Ngai Engineering is your answer. Our dedicated team specialises in delivering quality stainless steel fabrication and reliable service.
Contact us to discuss how we can bring your vision to life.