Spare Parts Maintenance Metal Fabrication: How To Reduce Cost
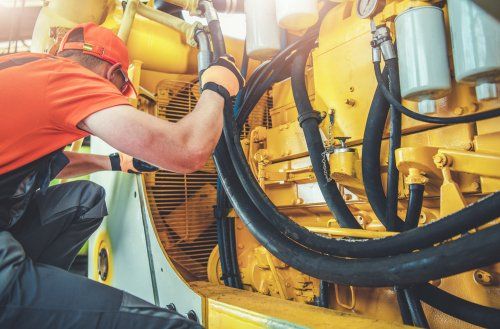
Metal manufacturers keep all the heavy equipment spare parts necessary for routine and urgent maintenance tasks on hand. The accessibility and efficiency of various manufacturing assets are improved by using these spare parts.
Some businesses suffer with spare parts management due to:
- Overstocking inventory
- Understocking inventory
- Lack of maintenance, repair, and operations (MRO) inventory
Reactive maintenance-based businesses spend more on repairs than proactive maintenance-based businesses. Additionally, the type and quantity of parts a company needs at any given time are determined by the number of manufacturing assets on the shop floor.
So, let's look at the different ways to reduce the cost of maintenance for heavy equipment spare parts in Malaysia.
How to reduce the cost of spare parts
A basic rule of thumb is that equipment maintenance expenditures should always be at most 5% of total asset value. As a result, it's best to invest in high-quality equipment. This guarantees a wise investment requiring less maintenance than second-hand or inexpensive machinery.
Undoubtedly, regular upgrades and inspections of high-quality equipment are necessary to lower the risk of failure. While ordinary equipment maintenance expenses differ (depending on your gear and required maintenance), it is in your company's best interest to budget around 2-5% of the entire replacement asset value (RAV). This amount can be calculated by:
- Sum up all maintenance-related expenses incurred for all of your assets over a year.
- Multiplying that total by 100.
- Dividing it by the entire cost to replace that asset.
Nevertheless, here are some suggestions for those using metal manufacturers and are looking to cut back on unnecessary expenditure on spare parts while maintaining optimal asset management.
Computerise all inventory management and maintenance procedures
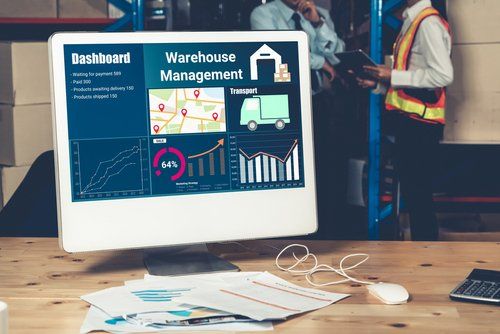
Better spare parts management is considerably supported by proper maintenance activity management. Businesses that use manual maintenance management systems cannot accurately track part use. As such, numerous digital technologies are made available, which are essential for coordinating and automating intricate maintenance procedures.
Computerised Maintenance Management Systems (CMMS) are being used on the manufacturing shop floor more frequently. Routine workflow can be automated by maintenance teams owing to this software. They enable technicians to automatically update maintenance, repair and operations (MRO) inventory and allow them to maintain thorough logs of all repair actions taken and spare parts used.
Automated MRO inventory tracking allows technicians to plan for upcoming maintenance activities. The business uses CMMS data to identify commonly used replacement components and to create a point at which they must refill. Additionally, the company can assess the quality of spare parts purchased from various suppliers.
When a company is aware of its statistics on spare part consumption, it can set up controls for MRO expenditures. They can also discontinue using components with high failure rates. It implies that the manufacturer can cut maintenance costs without endangering manufacturing processes or lowering the quality of maintenance operations.
Categories Spare Parts
Several pieces of equipment are needed for metal fabrication procedures. Each piece of equipment has specific maintenance requirements and uses a variety of spare parts. These components are grouped into the following:
- Critical spare parts
- Necessary spare parts
- Ordinary spare parts
The functionality of the equipment and process safety are greatly impacted by the availability of critical spare parts, which have longer lead times. For both planned maintenance and emergencies, these parts must be easily accessible. A thorough database of all the spare components required for routine operation should be developed by metal manufacturers.
After evaluating their spare parts need, companies should prioritise the items in order of importance and allocate budgets accordingly. Ordinary parts that are easily obtained can be kept in small quantities. But essential spare parts must always be accessible. Prioritising spare parts enables businesses to get rid of unnecessary inventory and retain a lean list.
Use original equipment manufacturer parts
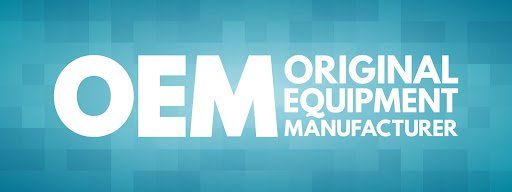
The average duration between failures is determined by the quality of spare parts required to keep manufacturing equipment running. Companies can select from the following:
- Original equipment manufacturer (OEM)
- Generic parts
- Aftermarket parts
Generally, OEM parts are more expensive than generic parts, but they are also of higher quality. Many companies spend more money on replacement parts because cheaper spare parts are less reliable. By minimising the usage of generic spare parts, metal manufacturers can lower their expenses on replacement parts. Since OEM parts are strong and long-lasting, production can continue longer with their use. It ensures that the company will experience fewer failures on average.
With fewer equipment failures, restocks for spare parts will be reduced. As such, the company can use the money saved by buying fewer spare parts to fund other facility improvement projects.
Manufacturers should select trustworthy vendors when developing a maintenance plan. Additional costs are associated with managing MRO inventories, such as insurance against theft and fire. By outsourcing inventory management-related risks to outside parties, businesses that choose vendor-managed inventories can save significant funds. In this manner, companies can purchase spare components at a discount and complete maintenance tasks on schedule.
Equip your employees
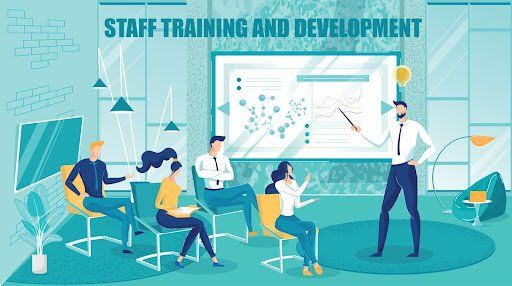
A staff member's carelessness could result in spare part waste. It occurs when the authorised staff fails to store items properly or uses inappropriate tools to repair them.
Sometimes when replacing equipment parts, technicians don't follow conventional operating protocols. These situations lead to early equipment breakdowns and a rise in defective or unusable stock. Over time, the business's cost of repairing minor or regular equipment faults increases.
For metal manufacturers to excel at inventory management and maintenance, their team must receive ongoing training. Those in charge of managing the following tasks should be familiar with the procurement and distribution of spare parts. The duties may include:
- New acquisitions
- Tagging spare parts
- Organising storage according to priority and acquisition dates
Maintenance employees should also receive training in the following:
- Equipment troubleshooting
- Workflow management with CMMS and Enterprise Resource Planning (ERP) software
- Proper tool use
These training sessions aim to ensure that staff members carry out the appropriate responsibilities during the initial trial. It avoids the need for rework, which necessitates more parts. It also ensures that spare parts are properly stored.
Employees in other departments can also benefit from digital skill training to better comprehend how specialised digital systems operate. As a result, they develop advanced skills to promote departmental cooperation.
Maintenance personnel can remotely check stock levels and manage their activities to maintain the smooth continuity of production operations. Additionally, procurement teams can receive restocking requests and approve them promptly.
Increase Your Savings With Proper Management
The financial success of metal manufacturing is impacted by cutting out wasteful spending on replacement parts. Your business can start by discovering the gaps and practices that result in inadequate spare part use. Establish internal management controls after that to help in keeping maintenance-related costs under control.
By making appropriate technical tool investments, you can also raise staff responsibility and process visibility. Finally, your business should train employees to foster a culture of continual improvement and promote excellence across the board in terms of productivity.
Looking for high-quality heavy equipment spare parts in Malaysia ? Choose Choong Ngai Engineering!
So, if you're looking for a sheet metal contractor in Malaysia, visit us at
Choong Ngai Engineering today to speak to our experts. We at Choong Ngai Engineering have years of experience and knowledge to answer your doubts or concerns, and we ensure to provide you with the quality solution you're looking for.
Call us now!