How Strong Is Welding, And Which Type Is The Strongest?
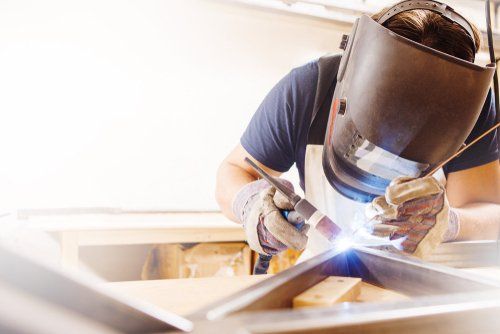
One of the most efficient methods for joining metal in fabrication is welding. In general, all welding processes can result in incredibly strong bonds. But is one type of welding superior to the other?
Various factors can determine the strongest weld in addition to the welding process. A number of variables are involved, including:
- the type of metals used
- the size and length of the weld
- the filler that was used
- the operator's or welder's expertise
So, let's take a closer look at the different types of welding and which is the strongest technique.
The Two Types Of Welding: MIG (Metal Inert Gas) vs TIG (Tungsten Inert Gas)
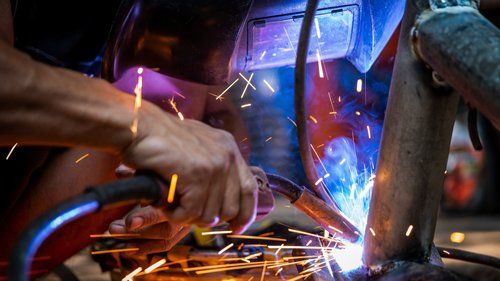
Welds come in a variety of types. MIG, TIG, Stick Welding, and Arc Welding are the most common ones. However, in this article, we will be focusing on MIG and TIG.
MIG (Metal Inert Gas)
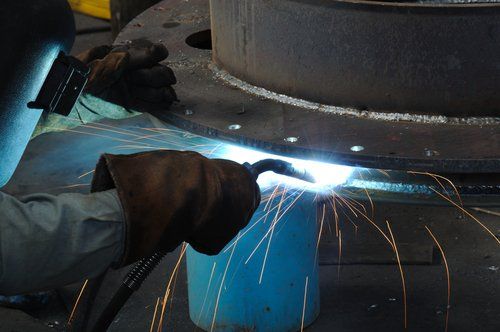
MIG, which stands for Metal Inert Gas, is also referred to as Gas Metal Arc Welding (GMAW). To do traditional MIG welding, you need the following:
- welding gun
- power source
- wire feed unit
- consumable welding electrode
- source of shielding gas
MIG welding parts are far more readily available and less expensive than TIG welding supplies. During MIG welding, the electrode wire forms an arc with the base metal being welded, melts, and fuses the two components. During this welding process, a gas bubble of protection is also created. This shields the weld from contaminants from the outside.
This type of weld is not recommended for
- Outdoors
- Locations with moving air
- Damp areas
Due to the difficulty of "fusing" with MIG welding, it has been dubbed the "hot glue gun" of welding. Contrary to TIG, which actually fuses the two materials, the MIG electrode wire serves as an adhesive between the two materials. This means that you can join different types of metals using MIG welding. It is more frequently applied to:
- Aluminium
- Steel
- Stainless steel
- Heavy-duty structural plates
- 26-gauge sheet metal
But, it is too weak for cast iron and too strong for thin aluminium. The ability to accelerate production and shorten lead times is a major advantage of MIG welding.
MIG is also quite straightforward to learn and master in a few weeks. However, MIG welding occasionally results in weak and less ductile welds, which are common quality issues. To solve these issues, avoid materials that are too thick or too thin, along with impure or unclean materials.
TIG (Tungsten Inert Gas)
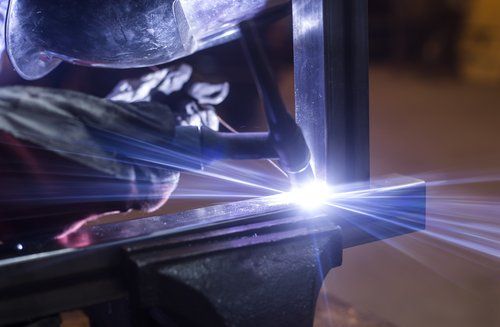
TIG, which stands for Tungsten Inert Gas, is also called Gas Tungsten Arc Welding (GTAW). Although TIG welding is difficult to master because of how hot it gets, welders have come up with some ingenious solutions over time. Some techniques include:
- Using minimum power
- Angle the torch appropriately
- Using the right type of tungsten
TIG welding is also done manually. For TIG welding, you will need:
- Welding torch
- Constant-current welding power supply
- An electrode of your choice
- Gas for shielding
- Grinder
- Filler metals
Additionally, you'll have to decide between hand control or pedal control, though most TIG welders use both hands. Since its electrode is non-consumable and constructed of tungsten, unlike MIG, you will eventually need to buy tungsten for maintenance after a few uses.
With the exception of zinc and zinc alloys, TIG welding is typically utilised for nonferrous materials like:
- Aluminium
- Magnesium
- Nickel
- Titanium
- Copper
To weld different metals with TIG, a compatible filler metal is required. The result of TIG welding is a durable and high-quality fusion. Since the tungsten rod is thinner than a stick rod, TIG welds are delicate and precise. It can therefore result in some appealing joins.
The drawback of TIG is that it can be time-consuming and slow. Moreover, despite the fact that its electrode is non-consumable, the TIG machine is initially expensive. It should only be managed and operated by trained employees.
MIG vs TIG
The materials you're working with will determine your best welding option. When done correctly, TIG welding may produce the best quality weld on any metal, but it fails to attach to thicker materials. Whereas MIG welding may be used on metals of any thickness, but it produces welds of lower quality and is mainly effective on steel and aluminium.
Despite having advantages and disadvantages of their own, TIG and MIG welding can both be the best option for your upcoming welding project. MIG welding is quicker and easier to do than TIG welding, but TIG welding provides you with better accuracy and a more attractive weld.
Which Welding Is The Strongest?
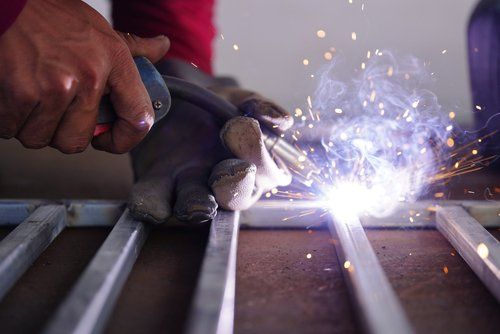
Due to the intense heat it generates and the delayed cooling rate that follows, TIG welding is frequently regarded as the strongest weld. Nevertheless, MIG is also a great option for the strongest type of weld because it may produce a strong joint.
The answer to this topic is fairly complex because the material to which a weld is applied determines its strength. There are three factors to consider when assessing a weld's strength which are:
- Length
- Size
- Filler
As a result, there is no simple answer to the question, "What is the strongest sort of weld?" The strength of the weld relies on the material and the welder's expertise.
Looking for metal welding services in Malaysia? Visit Choong Ngai Engineering now!
Prior to selecting a welding technique, it is crucial to consider the complexity and quantity of the parts that will be welded. Time and cost plays an important role as well so be sure to keep that in mind.
If you're looking for a reliable quality welding services provider in Malaysia, look no further than
Choong Ngai Engineering Works. We are a leading provider of
quality welding services Malaysia and provide the best possible service to our clients.
Contact us now!