The Different Types Of Industrial Storage Tanks Explained
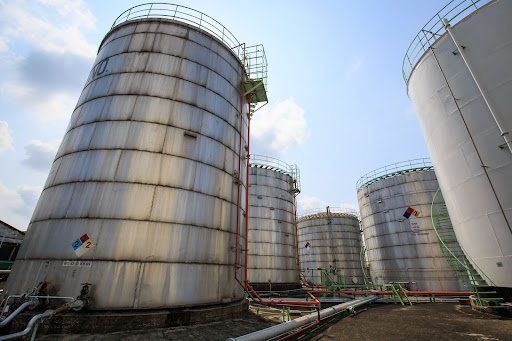
Choosing the right industrial storage tank for your business can sometimes be challenging due to the various types available in the market. Even more so with the advancement of new technology enhancing the features of the storage tanks.
Industrial storage tanks are essential for many types of businesses that deal with various elements, such as water, chemicals, fertilisers, petroleum, etc. Hence, picking the ideal type is important to ensure that the components will not be contaminated.
Let's take a look at some of the different types of industrial storage tanks.
Industrial Fuel Storage Tank
Industrial fuel storage tanks, also known as petroleum tanks, can hold a variety of liquids. They are commonly used for the storage of both organic and inorganic fluids. In addition to storing flammable liquids, they can also keep vapour. Fuel storage tanks come in a variety of shapes and dimensions. They are built to hold a range of fuels, vapour, and industrial liquids.
Here are some different types of industrial fuel storage tanks.
Underground fuel tanks (UST)
At least 10% of the stored volume of an underground storage tank (UST) is buried underground. These tanks must be registered with the EPA if they are used to store regulated hazardous items or fuels. These tanks are a good option for anyone wishing to increase their property's size or value.
Aboveground fuel tanks (AST)
Due to the lower upfront investments and regular maintenance, aboveground fuel tanks (AST) are rather popular. Compared to UST, these tanks are more affordable to build because they don't require costly backfilling, extensive excavation, or elaborate plumbing. Aboveground fuel tanks are also easier to maintain than underground tanks.
Industrial Chemical Storage Tanks
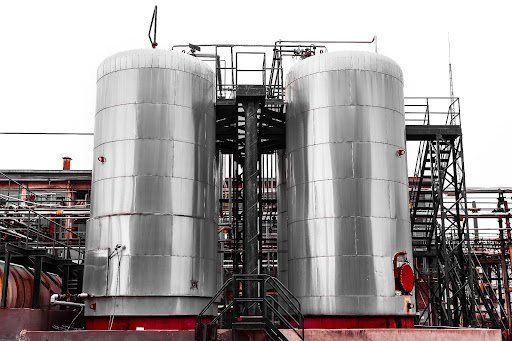
Materials that are stored in these tanks include:
- Fertilisers
- Propane
- Liquefied natural gas
- Petroleum products
- Crude oil
There are numerous sizes and shapes for industrial chemical storage tanks as well. In addition to storing chemicals, industrial chemical storage tanks can be used to do the following:
- Mixing
- Processing
- Static storage
- Transporting finished chemical products
The various types of these tanks include:
Fibreglass tanks
Due to its qualities that prevent corrosion, fibreglass has been employed more and more in piping applications for corrosive fluids since the 1950s. Fibreglass tanks have since been widely used in stock trade wastewater and chemical storage applications.
Polyethene storage
Chemical storage tanks made of polyethene are strong, durable, and inexpensive. Therefore, any chemical that you want to store can be stored in polyethene industrial storage tanks. Additionally, polyethene storage tanks are produced in moulds to eliminate the possibility of human error.
Stainless steel tanks
Stainless steel chemical tanks have evolved into a practical solution for everyone to meet the tremendous storage needs of companies. Various types of stainless steel tanks on the market are renowned for their strength, reliability, durability, storage capacities, affordability, a wide range of uses, and corrosion resistance. To meet your needs, they are meticulously manufactured and specially tailored.
Industrial Oil Storage Tanks
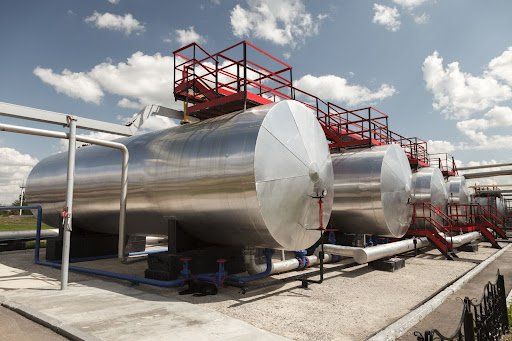
Oil storage tanks are reservoirs or vessels that temporarily store oil during the various processing stages into oil products of different types or before it is consumed or used. Industrial oil storage tanks are made of various materials depending on their intended use as well as the safety, environmental, and regulatory requirements of other types in the storage area.
From the initial production of crude oil to the distribution and refinement of various petroleum oil products, oil storage tanks of different sizes, forms, materials, and types are utilised.
Nowadays, modern industrial oil storage tanks are made of different materials, including:
- Carbon steel
- Stainless steel
- Reinforced concrete
- Plastic
Here are some of the different types of these tanks:
Bunded tank
Bunded tanks are either surrounded by another tank or a containment dike. The containment dike or outside tank serves as a catch system to stop leaks, spills, or other oil contamination from spreading to the surrounding area.
Floating roof tank
A floating roof that rises or lowers in response to the amount of oil in the tank makes up the floating roof tank. The floating roof is a safety precaution for these tanks to avoid the accumulation of vapour inside the tank.
Single-skin and double-skin tank
A single-skin tank has one layer of plastic or steel, while a double-skin tank has two layers. Tanks with two skins are often known as twin-walled tanks.
Industrial Hot Water Storage Tanks
Industrial hot water storage tanks are ASME-certified and designed for industrial applications where a steady hot water supply is necessary. In the water storage tank, water is heated and stored during times of low demand so that it will be ready for use when there is a high demand for hot water. As a result, hot food is always available while utilising energy efficiently.
A well-insulated industrial hot water tank can hold the heat for extended periods, lowering fuel consumption. Industrial storage tanks sometimes have electric immersion heaters and built-in oil or gas burner systems. Some hot water tanks use an external heat exchanger, like a central heating system.
Industrial Water and Liquid Storage Tanks

Aside from storing a wide range of the following liquids, industrial water and liquid storage tanks are designed for underground burial and pressurised application. The different types of liquids include:
- Kerosene
- Jet A
- Diesel
- Gasoline
- Waste oil
Here are some of the different types of industrial water and liquid storage tanks:
Corrugated steel tanks
The tanks made of corrugated steel for liquid storage are adaptable, strong, affordable, and have a long lifespan. They are created from corrugated steel that has been galvanised.
These tanks are used for the following:
- collecting rainwater
- industrial process water
- fire suppression
Poly tanks
Poly tanks can also be used in homes. These tanks have many uses, such as storing drinking water and collecting rainwater. There are various varieties of poly tanks, including:
- wastewater tanks
- transportable tanks
- aboveground tanks
Fibreglass tanks
Due to their resistance to rust and corrosion, fibreglass liquid storage tanks are long-lasting. The temperature resistance of these tanks is remarkable. They are available with various coatings to provide the best performance for different liquid storage demands, including:
- Rainwater
- Drinking water
- Waste water
Industrial Plastic Storage Tanks
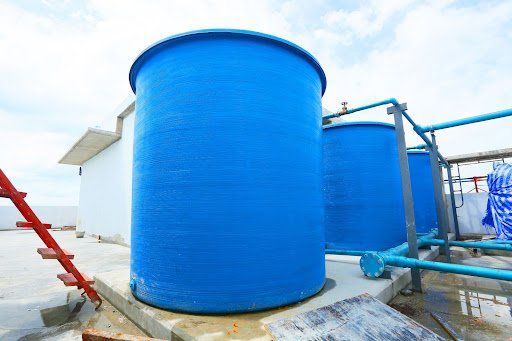
Water storage is essential for domestic, residential, commercial, industrial, and industrial needs. One of the greatest options for conventional water storage is plastic storage tanks. Plastic storage containers are more compact, lightweight, and highly durable than cement and concrete tanks. In addition, plastic tanks are more flexible than traditional storage tanks.
Your Business Deserves The Best Quality And Ideal Industrial Storage Tanks
Knowing a bit more about industrial storage tanks can help you choose the one that best suits your requirements. Make sure to consult a specialist if you have any questions. When operating any form of tank, always keep in mind to adhere to the manufacturer's guidelines.
Looking for a quality industrial storage tank fabrication company in Malaysia ? Choose Choong Ngai Engineering!
So, if you're looking for stainless steel tank fabrication in Malaysia, visit us at Choong Ngai Engineering today to speak to our experts. We at Choong Ngai Engineering have years of experience and knowledge to answer your doubts or concerns, and we ensure to provide you with the quality solution you're looking for. Call us now!