What Are Metalworking Fluids And Their Main Functions?
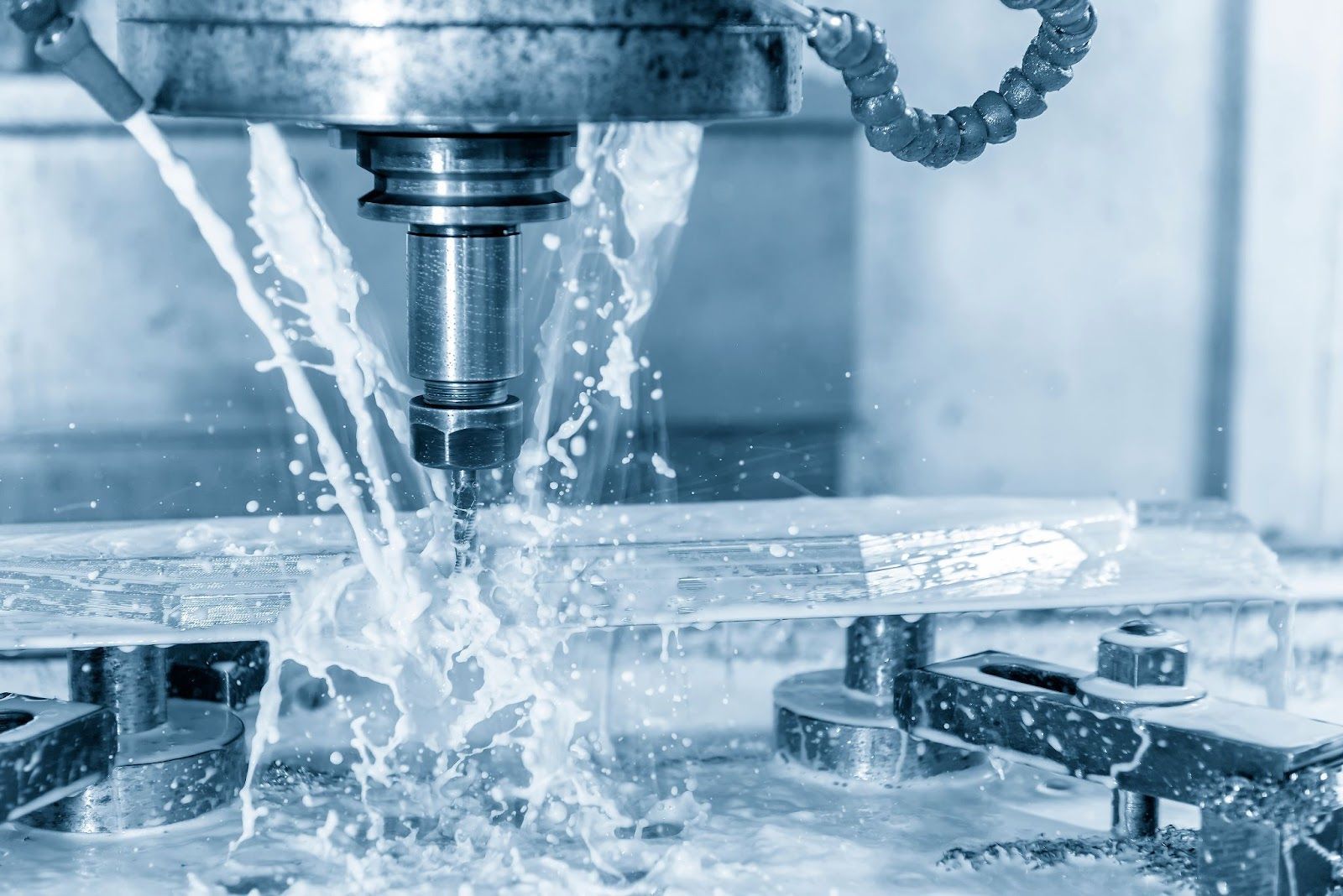
Metalworking fluids, often known as coolants or cutting fluids, are essential in various industrial operations that involve machining, shaping, and fabricating metal. Whether you're new to metalworking or looking for a deeper understanding of these vital fluids, this post will provide insights into the basics of metalworking fluids and cover their major functions in optimising production processes.
So let's get started and learn more about these crucial components that keep the metalworking sector operating smoothly.
What Are Metalworking Fluids?
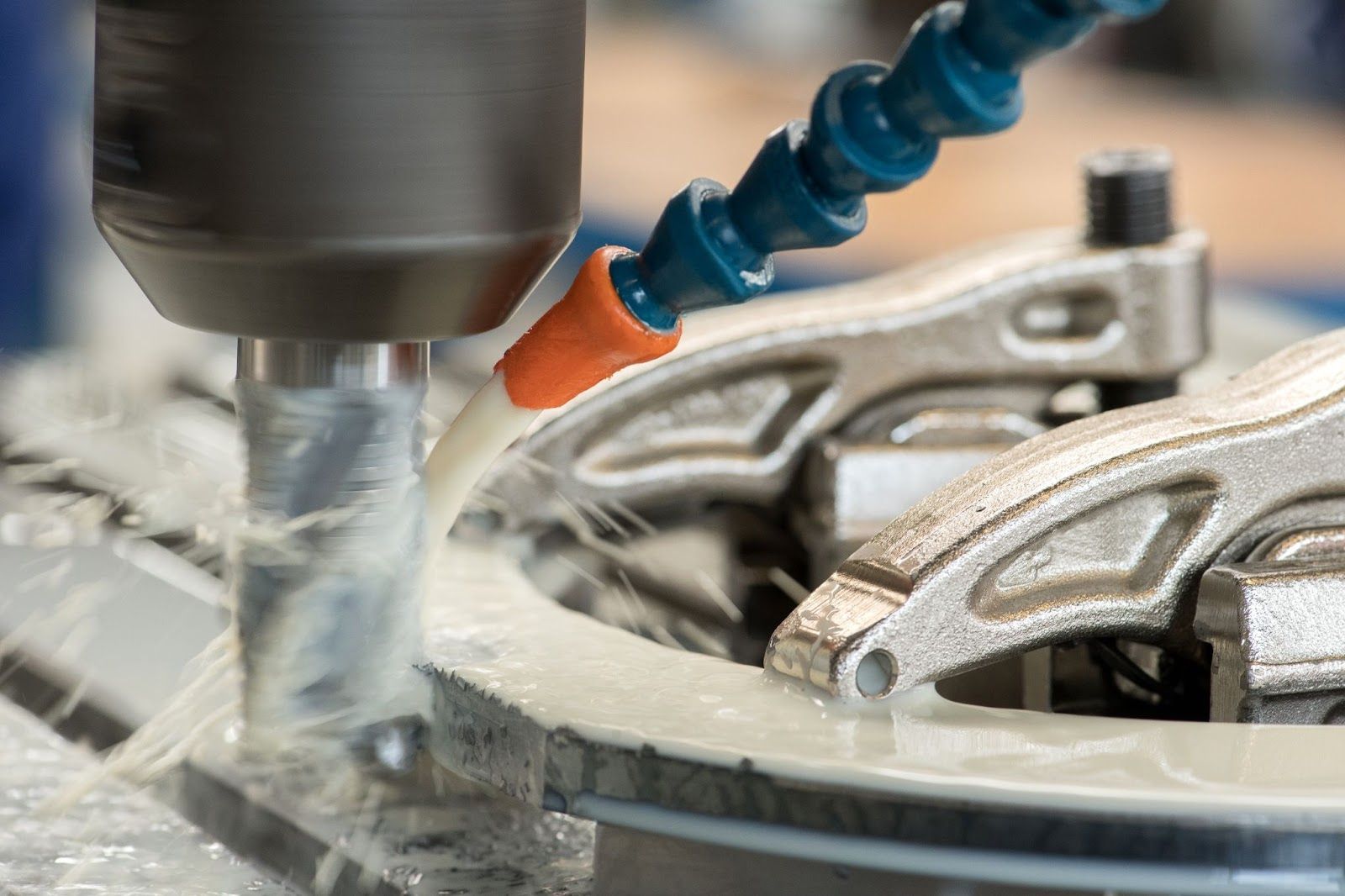
The term "metalworking fluid," usually referred to as "MWF" informally, refers to a variety of fluids, oils, and greases used to cool and/or lubricate metal workpieces during various processes such as:
- Milling
- Grinding
- Machining
To help avoid smoke and burning, metalworking fluids can efficiently reduce the friction and heat generated between a cutting tool and the workpiece. Moreover, using metalworking fluids helps a workpiece's quality by continuously removing the following elements from the workpiece's surface, including:
- Fines
- Swarfs (small shards of metal that the cutting tool removes)
- Chips from the tool being used
What Are The Main Functions Of Metalworking Fluids?
The metalworking cutting fluid can be used for a variety of cutting and grinding operations on a wide range of materials, including non-metallic materials, and it performs with remarkable stability. The product's excellent chemical lubricity and mechanical lubricating capabilities make it ideal for the most demanding cutting and grinding processing requirements. It is an ideal choice for manufacturers of high-quality parts in large quantities.
Here are the main functions of the metalworking fluids in the industry.
Creates a protective barrier
A metalworking lubricant's primary job is to keep the workpiece and tool apart, eliminating any metal-to-metal contact. To prevent contact, fluids must create a shielding film that protects the tooling.
This is crucial since expensive tooling is involved. Longer tool life and cost recovery are benefits of using an efficient metalworking lubricant.
Minimising corrosion
Corrosive forces need to be managed by the fluids used in metalworking. In addition to preventing corrosion, metalworking fluids have to safeguard the slides, punch, guides, and even the primary structure of the machinery from wear particles.
Minimising friction
Any metalworking fluid's ability to reduce friction where metal and tooling are in contact is a crucial component. Lowering friction provides various operational advantages, including lower energy consumption to form the parts and reduced drag on metal, resulting in an equal flow of metal through the forming die.
In general, reducing friction leads to fewer undesirable deposits blocking machine work areas since it reduces the number of particles in the punch region.
Improved sanitation
Metalworking fluids can also maintain and create a conducive work atmosphere and encourage cleanliness in all processes. The lubricants that are utilised must always be easy to wash off of the newly built part and have the ability to prevent the accumulation of unwanted residues.
The metalworking fluids must be entirely safe for use with degreasers and cleaners for health and safety.
Function of cooling
A significant amount of heat is bound to be produced during the machining process due to the simultaneous actions of shearing and friction. If this heat is not eliminated quickly enough, a high temperature will be created between the tool and the workpiece, weakening the tool. Even worse, the workpiece's surface will become less durable, and the tool wear and surface precision will all be impacted.
Additionally, the high temperature will result in a built-up edge, which will affect the precision with which the workpiece is processed. The heat that is produced during the machining process can be removed by flushing it out with a sizable flow of metalworking fluid.
Anti-rust capability
The majority of metals rust quickly when exposed to damp air and water, and during the metal machining process, if the metalworking fluid does not offer adequate rust protection between two distinct processes, it may result in the semi-finished product rusting and having to be scrapped.
Understanding The Role Of Metalworking Fluids Will Enhance The Quality Of The End Product
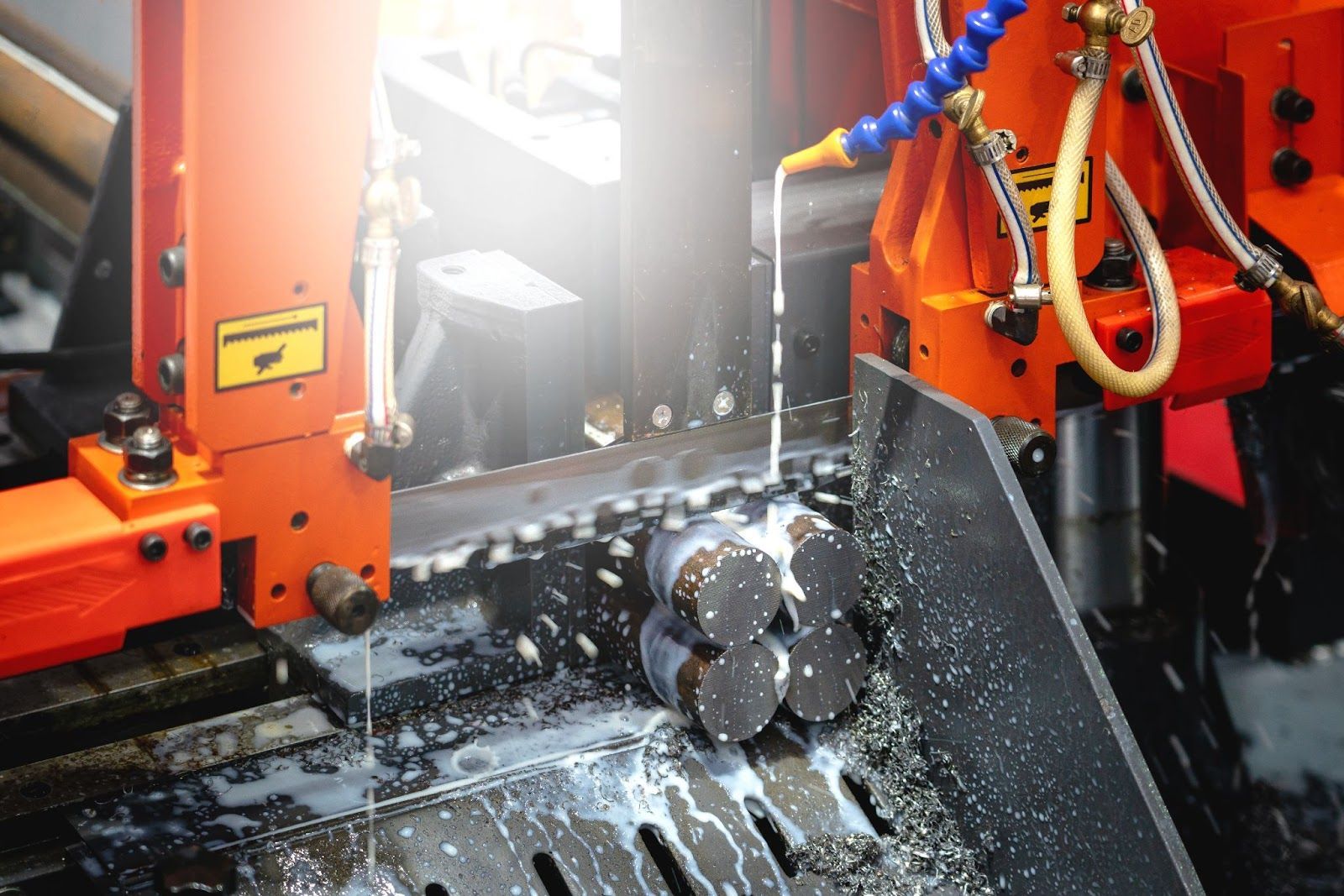
In order to ensure that cutting-edge solutions lead the way for more effective and ecologically friendly manufacturing practices, metalworking fluid formulation and application will continue to develop along with the metalworking sector.
By embracing the versatility of these fluids, businesses can move forward with confidence, using their production capacity while aiming for environmental responsibility and quality in their products.
Looking for high-quality custom metal fabrication in Malaysia? Choose Choong Ngai Engineering!
If you're looking for a custom
metal fabricator in Malaysia, visit us at
Choong Ngai Engineering today to speak to our experts. We at Choong Ngai Engineering have years of experience and knowledge to answer your doubts or concerns, and we ensure to provide you with the quality solution you're looking for.
Call us now!