Five Best Practices for Bending Sheet Metal
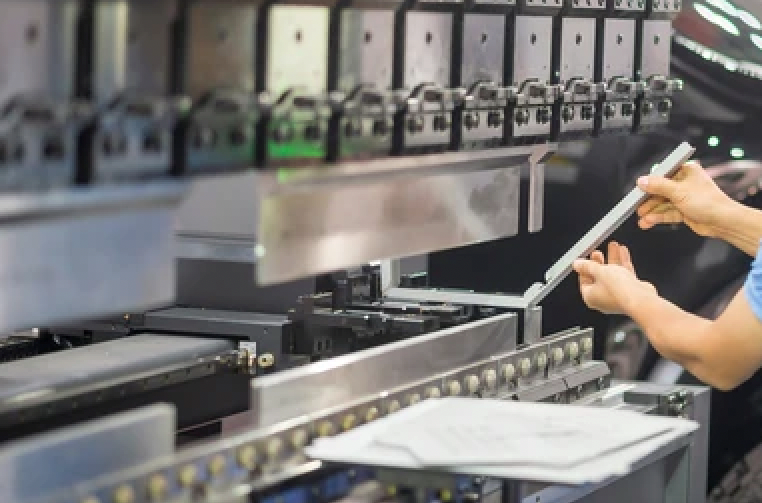
Sheet metal bending is a process that can be used to create a variety of objects from thin sheets of metal. It can be used to create everything from simple brackets to more complex shapes.
To get the best results from this process, it is essential to follow some best practices. In this blog post, we will discuss five of the most critical best practices for sheet metal bending.
1. Reduce Displacements
Displacements are caused by the material stretching as it is being bent. This can cause problems with the final shape of the object. To reduce displacements, the hydraulic press and sheet metal should be aligned and close together so that the sheet metal is bent along its natural grain.
The components should also be arranged to minimize the amount of stretching that occurs. By doing this, welders and fabricators can produce better results.
2. Choosing The Right Press
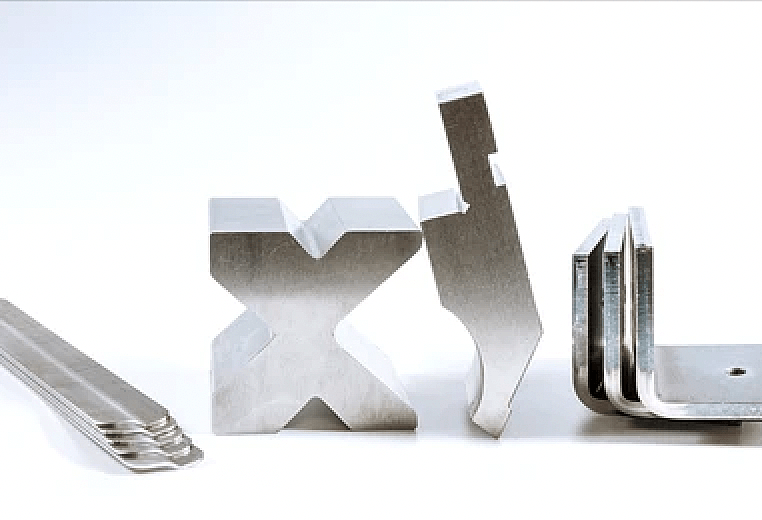
Many different types of presses can be used for sheet metal bending. Each type of press has its own advantages and disadvantages.
The best type of press to use will depend on the specific project that you are working on.
Choosing the right press is vital because it can help reduce the amount of time needed to complete the project. It can also help to improve the quality of the final product.
If you are unsure which press to use, you should consult with a professional.
Using the wrong type of press can damage the sheet metal or cause the final product to be of poor quality.New Paragraph
3. Having Standardized Manual
A manual is a document that provides instructions on how to complete a task.
It is important to have a standardized manual for sheet metal bending because it can help to ensure that the process is completed correctly.
The manual should include information on the best practices for sheet metal bending and the specific steps that need to be taken to complete the project. Without a standardized manual, it is easy to make mistakes that can damage the sheet metal or cause the final product to be of poor quality.
Having a standardized manual is especially important if you are working with a new team or new to sheet metal bending.
If you do not have a standardized manual, consider creating one.
Doing so will help to ensure that the process is completed correctly and that the final product is of high quality.
4. Being Proactive
Being proactive is important in all aspects of life, but it is especially important when working with sheet metal.
A lot of times, problems can occur during the bending process.
By being proactive and taking steps to prevent these problems from occurring, you can save time and money.
Some of the things that you can do to be proactive include performing regular maintenance on the equipment, keeping an eye out for potential problems, and being quick to fix any issues that do occur.
It can also help to prevent accidents from happening.
5. Learning and Communication
As metal bending technology advances, new methods and best practices are constantly developing.
It is essential to stay up-to-date on these advancements so that you can be sure that you are using the most effective methods.
One way to stay up-to-date is to attend seminars and conferences. You can also read trade journals and other publications.
Communication is also as important as learning. By sharing information with others, you can learn about new methods and best practices. You can also learn from the experiences of others - whether it's through networking, attending conferences, or even just having conversations with your colleagues.
We promote best practice & services for metal bending in Malaysia? Try Choong Ngai Engineering
As with any industry, there are always best practices that should be followed to produce the best results. The same is true for metal bending services.
By following these best practices, you can be sure that you are using the most effective methods for sheet metal bending. This will ultimately lead to better results and a higher quality final product.