The History And Benefits Of The Die-Casting Process
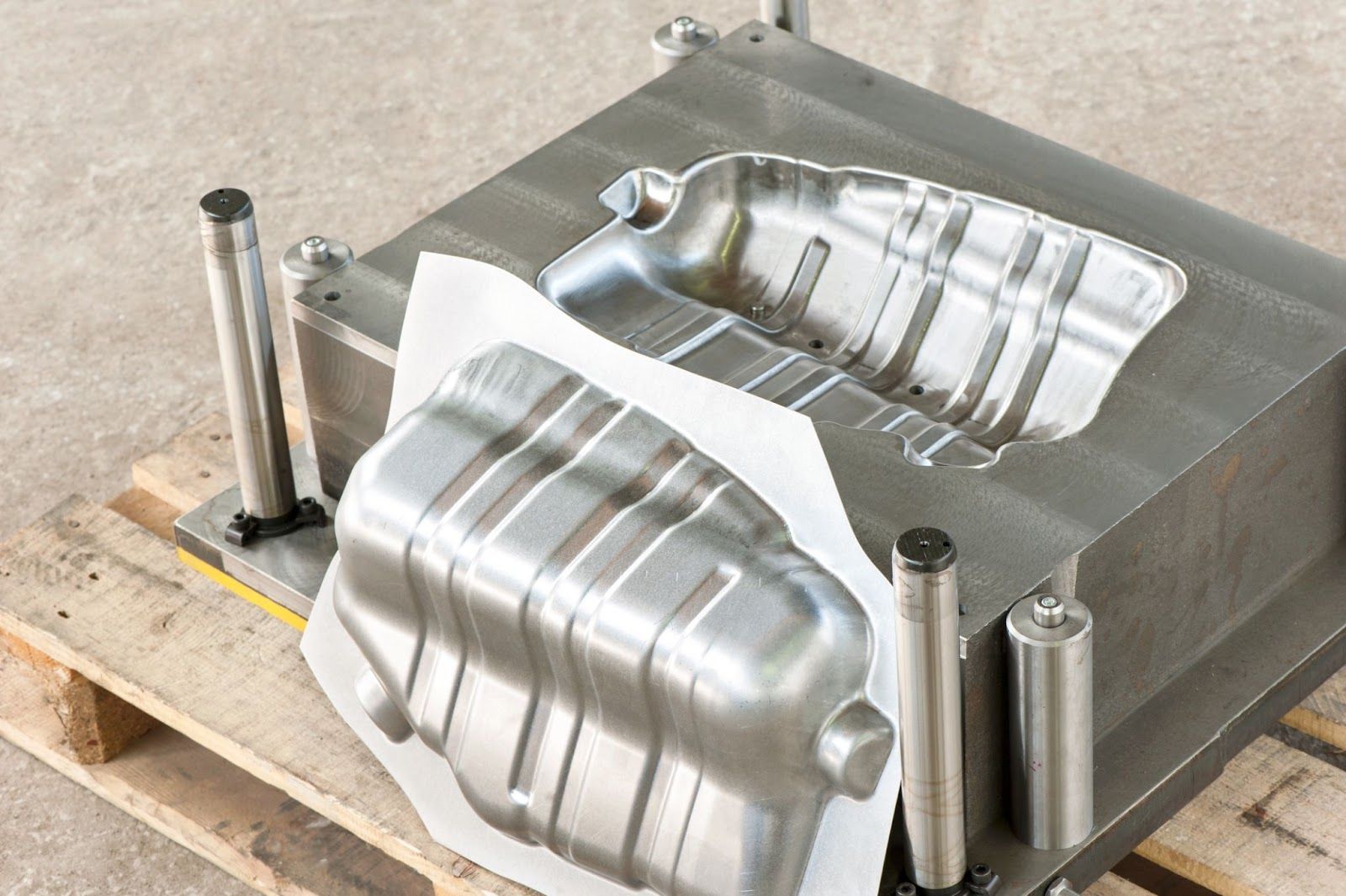
Die-casting has a long history and remains an essential method in current manufacturing. This process, which dates back to prehistoric times, has changed through the years and revolutionised the manufacturing of intricate and sophisticated metal components. We can learn a lot about the value of the die-casting technique and its ongoing influence on numerous industries by studying its origins in history and recognising its modern advantages.
Furthermore, die-casting has proven itself as a flexible and dependable process for making high-quality metal parts, owing to its ability to produce intricate designs with extreme precision and efficacy at an affordable cost. So let's explore more about die-casting and its origin.
What Is Die-Casting?
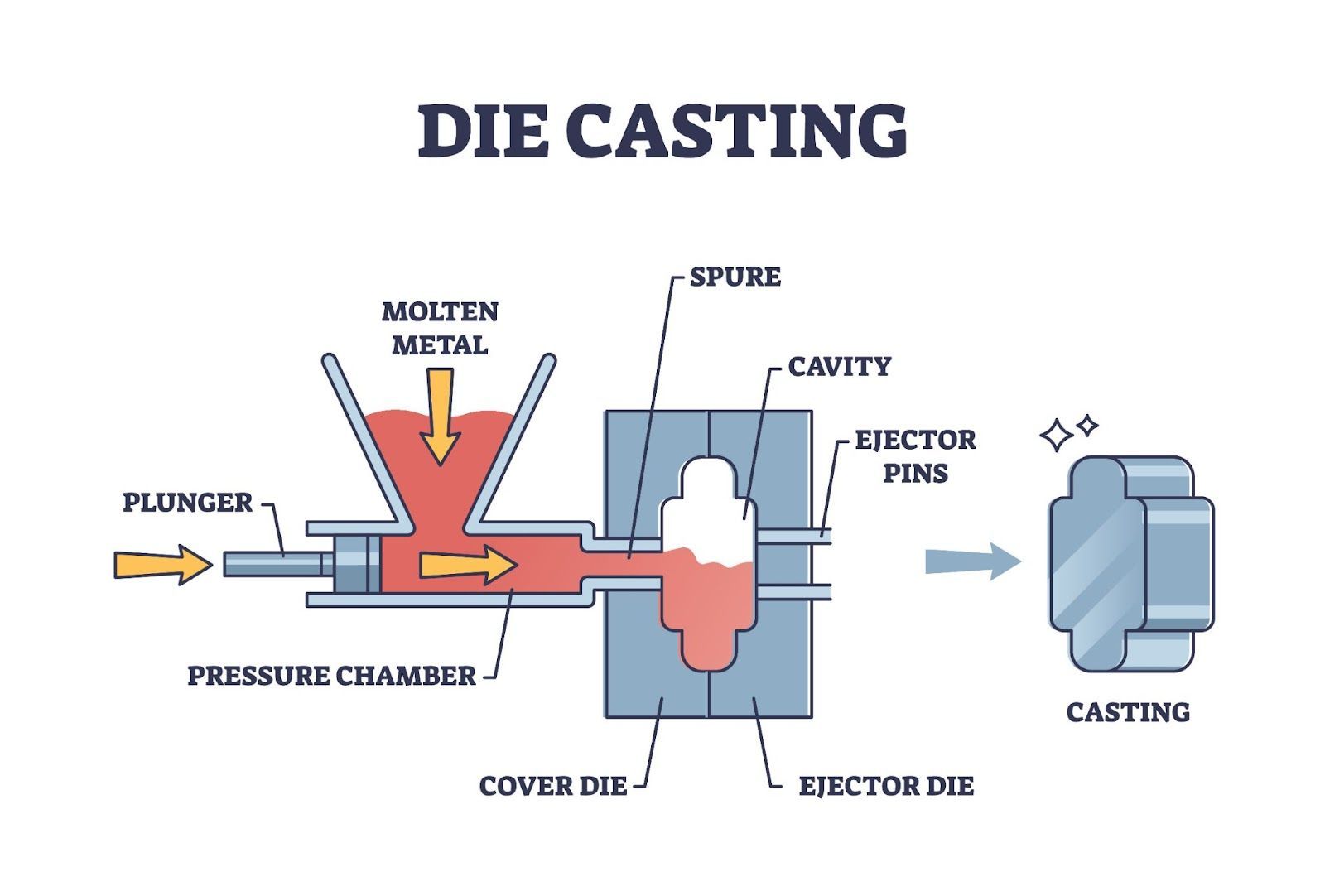
Die-casting is a technique of melting and casting metal materials. With the exception of molten metal, it is similar to plastic injection, which the majority of people are familiar with.
Due to the high temperature and pressure, and quick curing time of the molten soup, the die-casting mould materials, which are entirely different from plastics, include:
- Runner design
- Melting equipment
- Injection system
The hot and cold chamber die-casting machines are the two types of die-casting devices. A hot chamber cast equipment has an integrated furnace that melts metal before pouring it into moulds for shaping, which can speed up the manufacturing cycle. On the other hand, metals are heated in a separate furnace in a cold chamber machine.
Hot chamber devices cast metal alloys with low melting points, such as:
- Zinc
- Copper
- Lead
However, the cold chamber machine is favoured for metals with high melting points and corrosion resistance. As such, the equipment used depends on the material you select for the process.
The History Of Die-Casting
In 1838, movable type printing moulds led to the development of die-casting. The earliest manual piston hot chamber die-casting device in the United States, invented by J. J. Sturgiss in 1849, was continually used to create printing machine types.
Then in 1885, a German-American inventor, Ottmar Mergenthaler, created the Linotype typesetting. He transformed the entire row of independent type into an extended type, fundamentally altering the conventional printing method of manual typesetting and significantly boosting production efficiency.
To generate the necessary lead types, the printing industry has heavily utilised die-casting machines since the 1900s. Cast typesetting has advanced to the forefront of automation by then.
Czech engineer Jesef Pfolak later invented the contemporary cold-chamber die-casting machine. Furthermore, he also played a crucial role in the industry through the following:
- Solving the issue of the hot-chamber die-casting machine's molten soup corroding the injection system
- Isolating the crucible furnace for molten alloy
- Greatly increasing the pressure
Additionally, the shooting power is better suited to the demands of industrial mass manufacturing.
Various Benefits Of Die-Casting
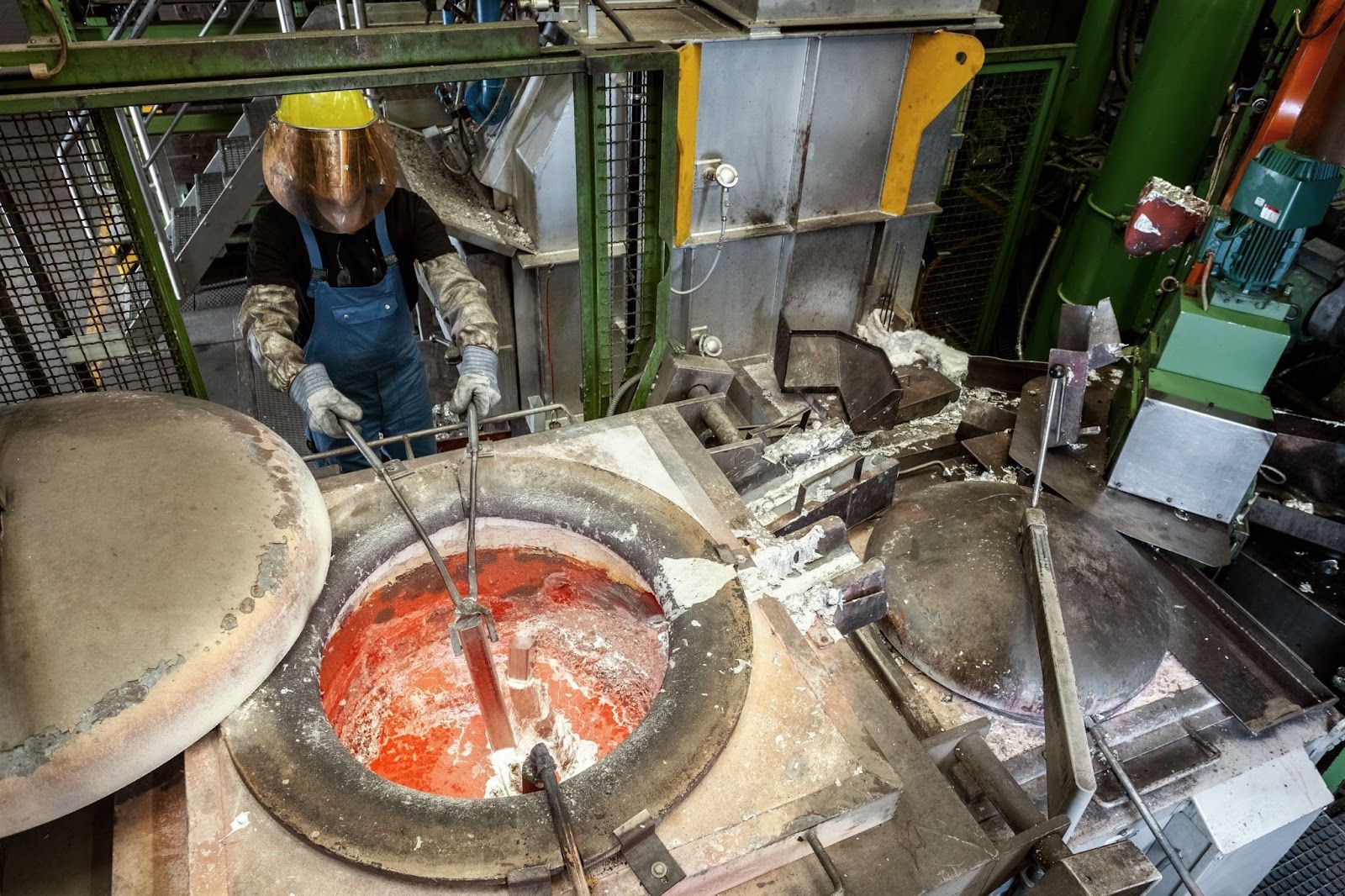
Die-casting is a metal part production process. The process involves pressing molten metal into a mould cavity, where it cools, solidifies, and takes shape. Today, anything from toys to car parts is still made using this method, which has existed for generations.
Here are some of the benefits of this process.
High Level Of Precision
Die-castings' dimensional tolerance may typically be managed to within +/-0.05mm depending on the following:
- Product's properties
- Area size
- Structural complexity
Integrity And Durability
The crystal grain size is incredibly small, only about 0.013mm, which makes die castings more durable than castings made using other casting techniques. Die-castings solidify quickly under high pressure and high temperature, experiencing a fairly low temperature in the outside atmosphere of the mould cavity.
Furthermore, compared to sand moulds or low-pressure metal mould castings, the thickness of high-pressure die castings may be considerably thinner. This reduces weight and costs while also reducing costs substantially.
Cost Effective
Die-casting moulds have a reasonably extensive mould life since they are constructed of special heat-resistant steel. As such, the die-casting technique is still the most cost-effective casting technique since it simultaneously reduces the time needed for each casting cycle due to the quick cooling speed.
Additionally, the method also reduces material and processing costs due to the narrow processing margin of the die-casting parts.
A Trusted Technique That Has Endured Through Time And Produces Great Results
Die-casting provides businesses with a productive technique to make huge quantities of parts swiftly and precisely. Studying the benefits and drawbacks of die casting can help you choose whether this process is best for your needs, whether you're a hobbyist or commercial manufacturer needing to create complex components or vast quantities of parts.
Looking for high-quality custom metal fabrication in Malaysia? Choose Choong Ngai Engineering!
If you're looking for a custom metal fabricator in Malaysia, visit us at Choong Ngai Engineering today to speak to our experts. We at Choong Ngai Engineering have years of experience and knowledge to answer your doubts or concerns, and we ensure to provide you with the quality solution you're looking for. Call us now!